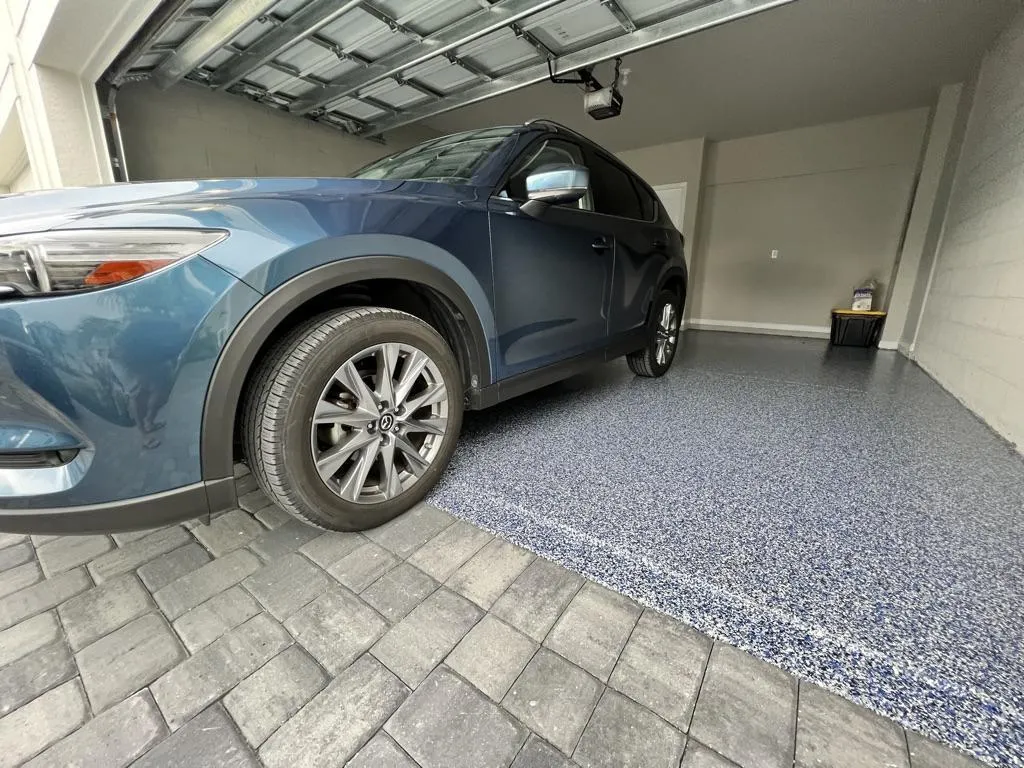
Epoxy Flooring vs. Sealed Concrete: Which Is Right for Your Port St. Lucie Space?
Concrete floors don’t have to be dull or purely utilitarian—they can be transformed into surfaces that are as functional as they are beautiful. At Floor Kings, we often get asked: “Should I choose epoxy flooring or sealed concrete for my project?” Both are great choices for protecting and enhancing your concrete slab. However, they differ in appearance, maintenance, durability, and cost over time.
In this detailed post, we’ll explore epoxy flooring vs. sealed concrete—covering everything from residential to commercial uses, essential installation details, and how to decide which option best suits your style and budget. Strap in for a comprehensive look at these two popular flooring solutions!
1. What Makes Floor Kings Different?
Here at Floor Kings, we’re committed to helping you select and install the perfect flooring. Whether you’re sprucing up your home or remodeling a commercial space in Port St. Lucie, our focus is on delivering exceptional workmanship, transparent communication, and results built to last.
Service Areas: Port St. Lucie, along with surrounding regions
Expertise: Polished concrete, epoxy flooring, sealed concrete coatings, and more
Approach: We believe in getting it right the first time. No shortcuts—only durable, beautiful floors that meet your exact needs
2. Epoxy Flooring 101
Epoxy flooring involves applying a two-part resin (epoxy) system onto a properly prepped concrete slab. When mixed and applied correctly, epoxy creates a hard, glossy surface that can stand up to heavy traffic, chemicals, and daily wear.
How Epoxy Flooring Works
Surface Preparation
We begin by cleaning, repairing, and sometimes lightly grinding the concrete to ensure a strong bond for the epoxy. Any cracks or imperfections are patched.Primer or Base Coat
Depending on the system used, a primer or initial coating is applied to promote adhesion and seal the concrete’s pores.Epoxy Application
The mixed epoxy (resin and hardener) is applied evenly. Multiple coats may be used, especially if additional effects—like color flakes or metallic finishes—are desired.Curing
Epoxy typically takes 24 to 72 hours to cure, during which it chemically hardens. Once cured, it forms a solid, durable layer over your concrete.
Why Go Epoxy?
High Durability: Ideal for garages, workshops, and even commercial kitchens
Chemical Resistance: Withstands oil, solvents, and other harsh substances
Customizable Appearance: A wide range of colors, flakes, and metallic effects
Seamless Finish: No grout lines or seams, making it easy to clean and maintain
3. Sealed Concrete 101
Unlike epoxy, which forms a thick, fully cured resin layer, sealed concrete involves applying a protective film—or penetrating sealer—over the slab. This film can be made from acrylic, urethane, polyaspartic, or other sealing agents.
How Sealed Concrete Works
Surface Prep
As with epoxy, the concrete is cleaned, and any damage is repaired. A light grind or etch may be done to help the sealer adhere properly.Sealer Application
The chosen sealer (water-based or solvent-based) is rolled or sprayed on. Some sealers need multiple coats, while others may only require one.Drying/Curing
Each coat must dry or cure according to the manufacturer’s specifications. Once complete, the floor is ready for traffic.
Why Go Sealed?
Simplicity: Usually faster to apply and cure than epoxy
Budget-Friendly: Lower initial costs for most sealing products
Finish Options: Can be matte or glossy, tinted, or even have decorative flakes
Moisture Barrier: Adds protection against spills and mild chemical exposure
4. Epoxy Flooring vs. Sealed Concrete: Core Differences
Let’s break down the key distinctions between these two flooring solutions:
Thickness & Appearance
Epoxy Flooring: A thicker, resin-like layer. It can create a high-gloss, showroom-quality finish. Color chips, metallic swirls, or custom designs are common.
Sealed Concrete: A thinner, often transparent or lightly tinted film. It preserves more of the slab’s natural look unless color tints or decorative elements are added.
Durability & Wear
Epoxy Flooring: Generally more resistant to heavy impacts, abrasions, and chemicals. Great for industrial, commercial, and high-use residential areas.
Sealed Concrete: Durable, but the thinner sealer may wear faster in high-traffic zones. More frequent reseals might be needed.
Maintenance
Epoxy Flooring: Simple cleaning—regular sweeping and occasional mopping. If damaged, repairs may require partial reapplication of epoxy.
Sealed Concrete: Also easy to clean, but you may need to reseal periodically if the top layer shows signs of wear.
Cost Over Time
Epoxy Flooring: Higher initial cost, but minimal upkeep if correctly installed. Can be cost-effective in busy environments with heavy traffic.
Sealed Concrete: Lower upfront investment, but potential for additional resealing expenses over the years.
5. Residential Applications
Epoxy Flooring at Home
Homeowners love epoxy flooring for garages, workshops, or basements. If you’re looking for a hard-wearing surface that resists oil stains and hot tire marks, epoxy excels. It can also be a stylish option for interior living spaces when you opt for decorative flakes or metallics.
Sealed Concrete in Homes
Sealed concrete is often chosen for patios, driveways, and indoor floors where you want a simpler application and a less glossy look. A tinted sealer can add warmth or color to your floors without the high shine of epoxy.
6. Commercial & Industrial Uses
Epoxy Flooring for Heavy-Duty Environments
Epoxy floors can handle forklifts, frequent foot traffic, and harsh chemicals. They’re a favorite in automotive shops, manufacturing plants, and commercial kitchens. The seamless, non-porous surface also aids in keeping facilities clean and compliant with certain hygiene standards.
Sealed Concrete for Medium-Traffic Spaces
Sealed concrete works well in retail settings, restaurant dining areas, and office buildings where the wear-and-tear isn’t as intense as in an industrial environment. It provides a protective layer at a relatively lower cost, with the option to add slip resistance or decorative touches.
(Floor Kings Tip:) If you have an extremely high-traffic facility, epoxy flooring may pay for itself over time due to fewer repairs and less frequent recoating. Sealed concrete can be more cost-effective in moderate-use areas.
7. Installation & Cure Times
Epoxy Flooring Installation
Preparation: Concrete must be clean, dry, and free of loose materials.
Multiple Layers: Primer, base coat, color or flake layer, and sometimes a topcoat.
Longer Cure: Full chemical curing can take up to several days.
Sealed Concrete Installation
Surface Prep: Cleaning, light grinding, or etching.
Single or Double Coat: Usually rolled or sprayed on, and each coat cures in hours, not days.
Faster Turnaround: Great if you need quick results.
8. Cost Factors & Lifecycle Analysis
Initial Outlay
Epoxy: Higher material and labor costs, especially for decorative or multi-layer systems.
Sealed Concrete: Generally more affordable upfront, with fewer layers and simpler application.
Maintenance
Epoxy: Durable, minimal routine maintenance—especially if it’s installed correctly.
Sealed Concrete: May require resealing every few years, depending on traffic and environment.
Long-Term Value
Epoxy: If your space demands a high-performance floor, the investment might save you money over time by reducing maintenance or replacement costs.
Sealed Concrete: Excellent for medium-traffic areas where heavy-duty performance isn’t a constant requirement.
9. Climate Considerations in Port St. Lucie
Port St. Lucie’s climate is hot and humid, with occasional heavy rainfall. Both epoxy and sealed concrete can handle Florida’s warmth, but there are a few things to keep in mind:
Moisture Vapor: Epoxy systems can be sensitive to moisture in the slab; a proper moisture test is crucial before installation.
UV Exposure: If you’re sealing or epoxying an outdoor slab, make sure the product is rated for UV exposure to avoid yellowing or premature wear.
Temperature Swings: Rapid changes in temperature can affect curing times. Always follow manufacturer guidelines for best results.
10. Style & Design Possibilities
Epoxy Flooring
Color Chips: Sprinkle decorative flakes in various colors for a unique look—popular in garages and showrooms.
Metallic Epoxy: Swirling patterns create a stunning, high-gloss finish that’s perfect for modern spaces.
Solid Colors: Keep it simple with a single hue that complements your décor.
Sealed Concrete
Tinted Sealers: Add a subtle wash of color while maintaining the concrete’s natural texture.
Decorative Flakes: Yes, you can add flakes to sealed concrete—though it typically appears less integrated than in epoxy.
Matte or Gloss: Choose a finish that aligns with your aesthetic, whether you prefer low-key satin or a light-reflecting gloss.
11. Maintenance & Cleaning
Epoxy Flooring
Routine Sweeping: Remove grit or debris to prevent scratching the surface.
Mopping: A mild, non-abrasive cleaner works best; avoid harsh chemicals that can degrade epoxy over time.
Inspect for Chips: If heavy objects fall on the floor and chip the epoxy, timely repairs help maintain a seamless finish.
Sealed Concrete
Regular Dust Mopping: Eliminates fine particles that can scuff the sealer.
Neutral Cleaners: Harsh chemicals may wear down the sealer prematurely.
Resealing: Pay attention to areas showing wear; a quick reseal may extend the lifespan of your floor.
12. Common Myths—Busted
“Epoxy Is Always Slippery”
Epoxy can be smooth, but additives like sand or aluminum oxide can boost slip resistance.“Sealed Concrete Doesn’t Last”
A good-quality sealer applied correctly can last for years. The key is proper prep and timely resealing.“All Epoxies Are the Same”
Not true! Different epoxy formulations vary in thickness, chemical resistance, and durability. A professional installer can specify the best type for your needs.“Sealed Concrete Looks Cheap”
With decorative tints, flakes, or stains, sealed concrete can appear high-end and refined—especially if you opt for a gloss finish.
13. Which Option Is Right for You?
High-Traffic, High-Performance Environments
Epoxy often wins for garages, industrial sites, or commercial kitchens where chemical resistance and durability are paramount.Moderate-Traffic, Budget-Conscious Projects
Sealed Concrete is a great middle-ground for retail shops, office floors, or residential areas with normal wear.Aesthetic Considerations
Epoxy can offer a striking, glossy look with endless color/flake possibilities, while Sealed Concrete tends to be subtler, highlighting the slab’s natural character.
14. How Floor Kings Can Help
We hope this overview clarifies the differences between epoxy flooring and sealed concrete. At Floor Kings, we’re here to guide you through each step—from initial consultation to the final coat.
Our Process
Assessment
We evaluate your slab, traffic levels, design preferences, and budget.Recommendation
Based on our findings, we suggest either epoxy flooring or sealed concrete—whichever aligns best with your goals.Installation
Our expert team handles everything from surface prep to curing, ensuring a top-quality result.Ongoing Support
Have questions post-installation? Need advice on cleaning or resealing down the line? We’re just a call away.
15. Ready to Elevate Your Floors?
If you’re in Port St. Lucie or the surrounding areas, Floor Kings is here to help you find the perfect flooring solution—be it epoxy or sealed concrete. Reach out today to discuss your project, request a quote, or learn more about our services.
Call: 772-370-7938
Email: [email protected]
From heavy-duty commercial floors to stylish residential upgrades, Floor Kings has the expertise and passion to make your floors look incredible while standing the test of time. Let’s make your concrete floors shine—your way!