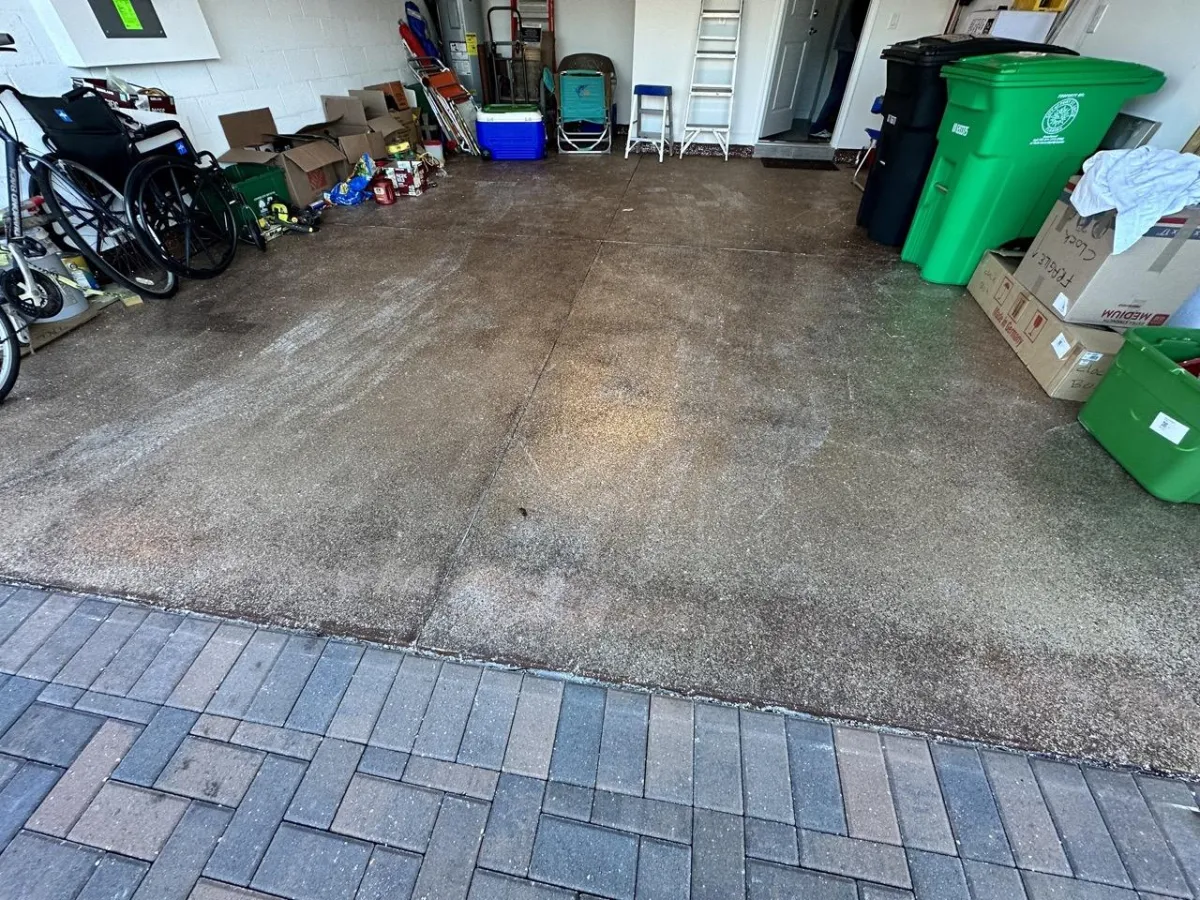
Polished Concrete vs. Sealed Concrete: Which Flooring Solution Is Right for Your Port St. Lucie Space?
Did you know concrete is one of the most versatile, durable materials you can use for your floors—and that it can look downright stunning too? At Floor Kings, we’ve spent years perfecting the art of concrete flooring. We’ve handled everything from elegant residential interiors in Port St. Lucie to massive industrial warehouses in nearby areas. And one of the most common questions we hear is, “Which is better: polished concrete or sealed concrete?”
The truth is, both are fantastic options, but each has unique characteristics that can make one method more suitable for certain environments. Below, we’ll explore the differences between polished and sealed concrete in detail—covering residential, commercial, and industrial use cases. You’ll also learn how to decide which approach best fits your vision and budget.
Strap in for a deep dive—this post is long and packed with insights gained from our decades of hands-on experience!
1. What Makes Floor Kings Different?
Here at Floor Kings, we treat every client like a partner. Whether you’re a homeowner in Port St. Lucie or a property manager overseeing a big warehouse in the surrounding region, our priority is clear communication, exceptional craftsmanship, and a can-do attitude.
Service Areas: Port St. Lucie and beyond!
Expertise: From anti-slip pool decks to custom countertops, we handle a wide range of projects, but our specialty lies in concrete coatings, epoxy flooring, and polished concrete.
Approach: We believe in doing it right the first time. We don’t cut corners, and we always aim for long-lasting results you can rely on.
Now that you know a bit about who we are, let’s dive into the heart of the matter: polished vs. sealed concrete.
2. Polished Concrete 101
Polished concrete floors begin with your existing concrete slab. We refine, grind, and polish the surface using industrial-grade diamond abrasives. Here’s a closer look at the process:
Initial Grinding
We start by removing any old coatings, adhesives, or blemishes on the surface using coarse diamond tools. This provides a level foundation for polishing.
Progressive Polishing
Next, we switch to finer and finer grit diamonds to achieve a smoother surface. Eventually, the floor develops a natural sheen—no topical film required.
Densifier Application
Partway through the polishing process, we apply a chemical densifier that hardens the concrete internally. It helps resist moisture and staining while adding durability.
Final Polish
As we reach 1,500 or even 3,000 grit diamonds, you’ll see a high-gloss, almost mirror-like finish. Some people prefer a matte or satin polish, so we can adjust to your taste.
Why Go Polished?
Extremely durable—there’s no coating to peel or chip.
Easy to clean (dust mopping and occasional damp mopping).
The reflective surface can brighten a space and reduce the need for overhead lighting.
Beautifully showcases the natural aggregate and character of your concrete slab.
3. Sealed Concrete 101
Sealed concrete involves placing a protective film or layer over the concrete surface. Depending on the project, this could be acrylic, epoxy, urethane, polyaspartic, or another sealer type. Here’s how it typically happens:
Surface Prep
We might do a light grind or etch to open the concrete’s pores, ensuring the sealer bonds well. Any cracks or imperfections are filled.
Sealer Application
We roll or spray on the chosen product, possibly in multiple coats. The final look depends on the sealer. Some are glossy, some matte, some can be tinted.
Curing
Each coat must dry and cure before foot or vehicle traffic can resume. Once cured, the floor benefits from an added protective layer against moisture, spills, and abrasions—up to the limits of that specific product.
Why Go Sealed?
Faster and often less labor-intensive than polishing.
Budget-friendly upfront cost.
Wide range of finish options, from high-gloss to matte, or even decorative flakes.
Works well in spaces that aren’t subject to extreme, long-term wear.
4. Polished Concrete vs. Sealed Concrete: Key Differences
Let’s break down some of the core differences in a more conversational way:
Process
Polished Concrete: Involves grinding, honing, and polishing. No real “top layer”—the shine comes from refining the slab itself.
Sealed Concrete: Uses a protective coating on top. The concrete itself isn’t ground to a high gloss; the appearance is determined by the sealer.
Durability
Polished Concrete: Extremely tough. Since there’s no coating to peel, it stands up well to heavy foot traffic and even vehicles like forklifts.
Sealed Concrete: Generally durable, but the sealer can wear down, scratch, or peel over time, especially in high-traffic commercial or industrial settings.
Maintenance
Polished Concrete: Minimal maintenance. Just sweep or mop. No waxing or stripping required.
Sealed Concrete: Also straightforward day-to-day, but the topcoat may require periodic resealing to maintain its protective qualities and appearance.
Cost Over Time
Polished Concrete: Higher initial cost, but fewer long-term expenses thanks to its longevity and durability.
Sealed Concrete: Lower upfront cost, but potential for higher cumulative maintenance expenses due to resealing.
Aesthetic
Polished Concrete: Showcases the natural beauty of the concrete, from exposed aggregate to a cream finish, with levels of gloss ranging from matte to mirror-like.
Sealed Concrete: Offers different sheen levels depending on the product. You can also add tints or decorative elements more easily, but the “depth” of shine isn’t the same as mechanical polishing.
5. Residential Applications: Style Meets Function
Polished Concrete in Homes
Homeowners throughout Port St. Lucie and beyond love polished concrete for its sleek, modern look. It’s especially popular in open-concept living areas, kitchens, and even bedrooms. If you have kids or pets, the floor’s durability and ease of cleaning are major perks. Plus, the slight thermal mass of concrete can help keep your home cooler during hot Florida summers.
Sealed Concrete in Homes
Sealed floors can also be a great option—especially if you want more color customization or if your budget leans this way. You can use tinted sealers or create decorative patterns with flakes. That said, you’ll likely need to reseal every few years in areas with heavy foot traffic, such as entryways or busy kitchens. For seldom-used spaces like basements, however, that might not be a big concern.
(Floor Kings Tip:) A few well-chosen rugs can add warmth and texture to concrete floors, whether polished or sealed. It’s a good way to balance modern design with cozy comfort.
6. Commercial & Industrial Spaces: Taking On Heavy Traffic
Polished Concrete for Commercial & Industrial
If you’re running a busy restaurant, a large retail store, or an industrial warehouse, polished concrete often stands out as the most robust solution. Its dense surface resists staining, scratching, and general wear. The reflective quality can also help brighten large spaces, potentially reducing energy costs by bouncing around overhead light.
Sealed Concrete for Commercial & Industrial
Sealed concrete can still work well in commercial or industrial settings, particularly if you use high-performance sealers or epoxy systems designed for heavier use. You can also add slip-resistant textures or aggregate to some sealers. However, intense traffic—such as forklifts operating around the clock—might wear down the sealer faster, necessitating periodic reapplication.
(Floor Kings Tip:) If you manage an industrial property or a large warehouse, we’ll help you evaluate the cost of polishing vs. sealing over the building’s lifespan. Sometimes paying more initially for polished floors saves a bundle in downtime and reseal costs later.
7. Installation: How Each Process Works
Polished Concrete Installation (The Long Game)
Grinding & Leveling: Remove old coatings, level the floor.
Progressive Polishing: Use increasingly fine diamonds to refine the surface.
Densifier Application: Hardens the slab from within.
Final Polish: Determine your ideal gloss level—matte, satin, or high shine.
The process can span days or weeks, depending on square footage and the condition of your existing slab.
Sealed Concrete Installation (Faster Turnaround)
Surface Prep: Light grind or acid etch, plus cleaning.
Sealer Application: Roll or spray on the product. Multiple coats may be needed.
Curing: Wait for each layer to fully cure before moving in.
Most sealed floors can be completed in a shorter timeframe than a full mechanical polish.
8. Cost Factors & Lifecycle Analysis
Polished Concrete
Higher Upfront Cost: The equipment and skilled labor for mechanical polishing can boost the initial quote.
Long-Term Savings: Fewer repairs, no resealing, and lower maintenance generally lead to cost savings over time.
Sealed Concrete
Lower Initial Cost: Less labor-intensive, fewer passes needed.
Possible Additional Costs: Resealing high-traffic areas, or dealing with worn or peeled coatings, can add expenses down the road.
When we consult with you at Floor Kings, we’ll break down these differences clearly so you can make an informed decision.
9. Climate Considerations for the Port St. Lucie Area
Port St. Lucie’s climate is famously hot and humid, with mild winters. Here’s how both flooring types handle it:
Polished Concrete: Because it’s densified internally, polished concrete typically has no issues with moisture vapor or heat expansion. It can handle temperature and humidity swings without delamination since there’s no film on top.
Sealed Concrete: High-quality sealers, especially those rated for UV stability and higher humidity, fare well here. Just be sure to choose a product formulated to withstand potential outdoor conditions if you plan to seal garages or patios.
10. Design & Customization Options
Polished Concrete
Aggregate Exposure: You can go for minimal aggregate (“cream finish”) or expose more stone for a more dynamic, terrazzo-like look.
Dyes & Stains: Add subtle earth tones or vibrant colors. Great for logos or accent areas in commercial spaces.
Patterns & Engravings: Saw-cut lines or stencils can create unique geometric or artistic designs.
Sealed Concrete
Tinted Sealers: Achieve a uniform color or a translucent wash.
Decorative Flakes: Popular in garages, showrooms, or retail spaces that benefit from a speckled, slip-resistant surface.
Metallic Epoxy: A dramatic, swirling effect that looks almost three-dimensional—perfect for making a bold statement.
11. Maintenance & Longevity
Polished Concrete
Daily: Sweep or dust mop to remove grit that could dull the finish.
Weekly: Light damp mop with a neutral cleaner if needed.
Long-Term: Under typical conditions, you won’t need additional coatings or polishes—just clean regularly.
Sealed Concrete
Daily: Similar sweeping or dust mopping routine.
Periodic: Depending on the type of sealer and traffic level, you’ll likely need to reseal every few years.
Careful with Cleaners: Abrasive chemicals or scrubbing pads can degrade the sealer’s surface faster, leading to patchiness.
12. Common Myths—Debunked
“Polished Concrete Is Too Slippery.”
It’s no more slippery than many tile or hardwood floors when dry. If you’re concerned, we can add slip-resistant compounds or opt for a slightly lower gloss level.“Sealed Concrete Looks Fake or Plastic.”
It doesn’t have to. High-quality, professional sealers—including epoxies—can look just as sleek as polished surfaces, though they will always be a thin layer on top.“Concrete Is Plain Gray and Boring.”
Dyes, stains, and decorative techniques can transform concrete into anything but boring. We’ve created everything from natural stone finishes to bold, metallic showpieces.“They’re All the Same in Terms of Durability.”
Not at all. Polished concrete’s mechanical refinement tends to stand up better to hardcore industrial wear, while sealed concrete excels in moderate or lighter traffic scenarios—or in specialty applications where color or decorative options need to be front and center.
13. Which Option Is Right for You?
High Traffic, Long-Term Use: Polished concrete usually excels in warehouses, restaurants, and large retail spaces due to its long-lasting durability.
Budget Constraints or Smaller Spaces: Sealed concrete can be more cost-effective upfront, perfect for residential areas or low-traffic commercial spaces.
Custom Designs: Both methods offer customization, but sealed concrete can be easier for large-scale color or metallic effects.
Climate & Maintenance: Polished concrete generally requires less upkeep, whereas sealed floors might need periodic reapplications—so factor that into your long-term budget.
14. Next Steps & How Floor Kings Can Help
We hope this thorough look at polished concrete vs. sealed concrete helps you weigh your options. Each approach offers unique advantages, and the best choice depends on factors like traffic levels, aesthetic goals, budget, and how long you plan to occupy the space.
How Floor Kings Can Assist
Consultation
We’ll evaluate your existing slab, usage patterns, and style preferences. Whether it’s for a home in Port St. Lucie or a full-blown industrial warehouse in the region, we’ll gather all the details.Recommendation
Based on what we learn, we’ll guide you toward polished concrete or sealed concrete—whichever aligns best with your objectives.Expert Installation
Our skilled team at Floor Kings handles the entire process—from initial prep to final finish—so you get a floor that’s installed correctly and built to last.Customer Satisfaction
We pride ourselves on our communication. You’ll know exactly what’s happening every step of the way, and we’ll make sure you’re thrilled with the results.
If you’re in Port St. Lucie—or anywhere nearby—we’d love to discuss your flooring project. Whether it’s a gleaming polished concrete surface for a modern office or a sealed garage floor with custom decorative flakes, Floor Kings has you covered.
Ready to Get Started?
Reach out to Floor Kings today:
Call: 772-370-7938
Email: [email protected]
Let us know about your project, and we’ll help you find the perfect flooring solution—one that brings durability, beauty, and real value to your space. From anti-slip pool decks to high-gloss retail floors, Floor Kings is your trusted partner for all things concrete!