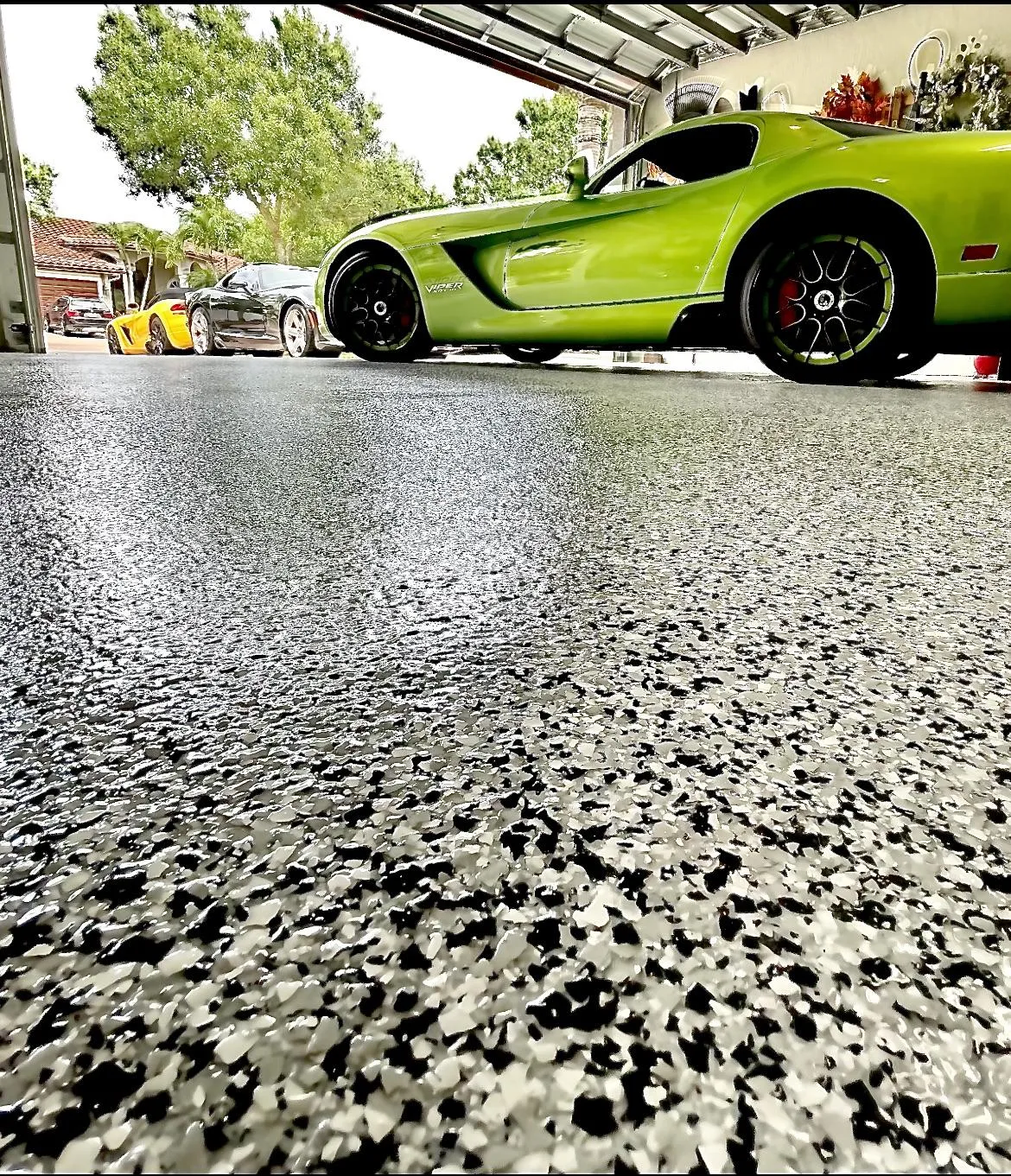
Epoxy Flooring in Port St. Lucie, FL: Is it possible to coat over existing flooring?
“Quality is not an act; it is a habit.” Aristotle’s centuries-old wisdom still holds true, even for something as seemingly modern as epoxy flooring. When you’re upgrading floors in a coastal area like Port St. Lucie, FL, you want a solution that resists humidity, salt air, and regular foot or vehicle traffic. Epoxy delivers on all those fronts. It’s a robust, versatile coating that can transform lackluster floors into eye-catching, durable surfaces. It can protect concrete from spills and chemical damage, and it can do wonders for the overall look of your property.
Yet, the success of an epoxy floor hinges on two main factors: the condition of the surface you’re coating and the level of preparation you invest in. In this comprehensive piece, we’ll explore which surfaces can host epoxy, how to handle each one, and whether you should remove your existing floor or simply overlay the epoxy. We’ll also talk about why local expertise—specifically Floor Kings in Port St. Lucie—matters in achieving a floor that can stand up to Florida’s unique conditions. By the time you’re done reading, you’ll know how to make informed decisions about your next epoxy project and who to trust with the work.
Epoxy on Bare Concrete
Bare concrete is the most straightforward foundation for an epoxy floor because it offers a natural texture that epoxy can grip. If the slab is in good shape and properly cured, epoxy can merge with the top layer of concrete, creating a seamless and highly durable floor. The Sunshine State’s humidity can make moisture testing especially critical, though. Even if the surface appears dry, there might be moisture vapor traveling upward. A professional can test the slab, often with a calcium chloride kit or probes that measure relative humidity within the concrete.
When you confirm that moisture levels are acceptable, you’ll need to grind or shot blast the surface to remove laitance (the weak, powdery layer on top) and open the pores of the concrete. That prep ensures the epoxy penetrates for a superior bond. After cleaning away dust, you may choose a primer. Primer helps seal micro-pores, levels out minor irregularities, and can reduce the risk of bubbles forming in the main epoxy coat. Florida’s climate can sometimes accelerate or slow down the curing process, depending on temperature and humidity, but a knowledgeable contractor will adjust accordingly.
The beauty of applying epoxy on bare concrete is that you get maximum performance with minimal worry about hidden issues. The main catch is that you must repair any cracks or spalling beforehand, or they’ll show up through your epoxy. If you want the best possible epoxy floor that can handle your hot, humid summers—and the occasional hurricane-level weather—this route is often the gold standard.
Epoxy Over Painted or Sealed Concrete
Sometimes your concrete floor might already have a coat of paint, sealant, or even a previous epoxy layer. As long as that existing layer is well-adhered, you can usually prep the surface and go right over it. You’ll need to scuff or sand the surface to create enough texture for the new epoxy. If the existing coating is peeling, you’ll have to remove it in those areas to avoid problems.
An adhesion test is a simple but effective tool. Professionals can cut a small grid into the coating and apply tape, then pull the tape off to see if large flakes come away. If the old coating peels right up, it’s not a good candidate for overlaying. If it stays put, you might be good to go. This can save you time and disposal costs. However, relying on an older layer means relying on its strength and bond to the concrete. If it fails later, your new epoxy will come with it.
Florida’s coastal climate can cause older coatings to degrade faster from salt, sun, and high moisture. If your existing floor looks chalky or feels brittle, that’s a red flag. Don’t let the allure of a shortcut lead you to invest in an overlay that’s doomed. When in doubt, consult a seasoned contractor who can help you weigh the risks and benefits.
Epoxy Over Tile
If you walk into many Florida homes or businesses, you’ll see tile floors. Tile holds up well to moisture, but eventually styles change, or you want something more seamless. Epoxy can go over tile. The tile needs to be stable, with no loose or cracked pieces that could cause the epoxy to delaminate. You’ll also have to deep clean the tile and possibly grind off any glaze or finish to help epoxy adhere.
Filling the grout lines is usually recommended if you want a perfectly smooth surface. That can be done with an epoxy patching product or similar material. Skipping that step might leave an imprint of the lines on the final floor. The main advantage of coating tile is you avoid the hassle of demolition, which can be loud and generate a lot of dust. The downside is that if any tile is hiding moisture or has a hollow pocket underneath, you may experience problems later.
Still, many Floridians opt for this approach because tile removal can be disruptive and time-consuming. If your tile floor is already structurally sound, epoxy can unify and modernize the look with less downtime, and that’s a big deal if you’re running a business or can’t vacate your home for long periods.
Epoxy Over Vinyl
Vinyl floors—especially VCT—are common in commercial settings like schools, hospitals, and offices. People like vinyl because it’s budget-friendly and relatively easy to clean, but it can wear out, dull, or peel over time. You can freshen things up by applying epoxy right over the vinyl if it’s still well-bonded to the subfloor.
Lightly sanding the surface and removing any wax or polish is essential. If the vinyl is curling at the edges, or if there’s a tear in a heavy traffic zone, you’ll want to repair or remove that section. One risk is that any existing adhesive might degrade in the future, which would cause the epoxy to peel as well. Another risk is that older vinyl adhesives can contain asbestos, so always test or consult a professional if you suspect your floor predates modern guidelines.
If everything checks out, epoxying over vinyl is a cost-effective and time-saving approach. The new floor will be more durable, chemical-resistant, and visually appealing than most outdated vinyl floors. You’ll also appreciate the reduction in daily maintenance. Just remember that you’re only as strong as your weakest layer, so do your due diligence before proceeding.
Epoxy Over Wood
Wood floors are a rarity when it comes to epoxy, at least in typical Florida homes. But in certain commercial or industrial scenarios, it might be a possibility. Wood subfloors can flex, expand, and contract with humidity, which is a big concern in Port St. Lucie. If you decide to epoxy over wood, you want to ensure the subfloor is stable, squeak-free, and thoroughly screwed down or supported. Sanding off any finish or seal is crucial, and sometimes you apply a special underlayment before the epoxy to reduce movement. Even then, you’re taking a risk if the environmental conditions fluctuate often.
If you’re set on an epoxy-over-wood setup, maybe for a unique design or an industrial-chic vibe, talk to a contractor with specific experience. The margin for error is slim. Make sure you thoroughly discuss how to handle temperature and humidity changes. Florida’s climate can be a challenge for wood, and you don’t want to see cracks or bubbles forming in your brand-new epoxy.
Epoxy Over Metal
Metal floors, catwalks, or industrial platforms can also take epoxy. The key is removing rust, existing coatings, or grime, then roughening the surface so the epoxy can get a firm grip. Typically this is done with sandblasting or aggressive grinding. A specialized metal primer is applied before the epoxy. This approach provides a protective layer against corrosion and an easy-to-clean surface. The only major concern is metal’s tendency to vibrate or flex under certain loads. That can stress the epoxy over time. If you’re working with a specialized industrial space, an experienced contractor can account for that.
The Role of Prep in Port St. Lucie
One pattern you may have noticed is that proper surface preparation is the central pillar of every successful epoxy job. Florida’s humidity can wreak havoc on a poorly prepared floor. If the top layer is contaminated with oils, cleaning residues, or even just dust, the epoxy might not cure or bond correctly. If the substrate is damp from humidity or ground moisture, you’ll see bubbling or lifting. If cracks go unfilled, they’ll become visible in the epoxy.
A thorough approach often involves mechanical abrasion to the correct depth, cleaning with industrial vacuums and degreasers, and addressing moisture with vapor barriers or specialized primers if needed. Homeowners sometimes balk at the cost of prep, but it’s critical if you want a floor that lasts. Think of it like building a house. You wouldn’t skimp on the foundation. The same logic applies to epoxy. The better your prep, the fewer nightmares you’ll have down the line.
Overlay vs. Substrate Removal: Pros and Cons
Deciding whether to epoxy directly over your existing floor or rip it out to reach bare concrete is a matter of balancing time, budget, and risk. If the underlying floor is stable and well-bonded, overlaying saves you from the mess and expense of demolition. That’s great for retail stores, restaurants, or busy households that can’t afford a lengthy shutdown. On the other hand, if you suspect any hidden moisture or questionable adhesives, you run the risk that your new epoxy floor could fail because of issues below the surface. That might cost you double in repairs.
Removing everything down to bare concrete provides a fresh start. It might be pricey, but it allows you to address cracks, moisture, or leveling problems and ensure maximum bond strength. That’s the route to choose if longevity is your top concern or if there’s significant doubt about the condition of the old flooring. It can also give you peace of mind knowing that no unknown layers are lurking beneath your new investment.
Practical Insights for a Successful Epoxy Floor
If you’re planning to install epoxy in Port St. Lucie, keep a few tips in mind. First, always schedule a consultation and thorough moisture testing. Florida’s water table is high, and ground moisture can come up through concrete slabs more than you might expect. Second, think about your usage patterns. Are you parking heavy vehicles on the floor? Do you anticipate chemical spills from pool supplies or workshop chemicals? Are you aiming for a decorative, showroom-quality finish? Each of these uses might dictate different types of epoxy or additives, such as decorative flakes for traction or UV-stable topcoats.
Another practical point is to keep your space climate-controlled if possible during the curing process. Extreme heat or humidity changes can alter how the epoxy sets. If you have to do the job in the middle of summer, talk to your contractor about early morning or late evening pours, or about specific formulations designed for warmer conditions.
Finally, factor in cure time before you start moving furniture or vehicles back onto the floor. Epoxy might be hard to the touch in a day or two, but full chemical cure can take longer. Rushing it can lead to permanent marks or indentations. Resist the urge to push it. A few extra days of patience can prevent years of regret.
Why Floor Kings in Port St. Lucie, FL?
Floor Kings is a local business that lives and breathes epoxy. They understand that coastal living presents unique challenges—high humidity, salt-laden air, and sudden downpours that come with Florida’s weather patterns. They also know how to evaluate an existing floor’s condition, whether it’s tile, vinyl, or sealed concrete, to determine the best approach for a lasting epoxy installation.
Communication is a top priority for Floor Kings. They don’t just show up, slap on some epoxy, and disappear. They walk you through each step—moisture testing, prep, product selection, color choices, topcoat preferences—so you can feel confident. Their portfolio includes residential garages that withstand daily driving, commercial kitchens that need easy sanitization, and everything in between. They also understand that homeowners want a gorgeous finish and a fair price, while commercial clients might value uptime and quick turnaround. Floor Kings tailors their approach to each scenario.
When you call Mike at Floor Kings, you’ll get transparent advice on whether overlaying your existing floor is wise or if you’d be better off removing it entirely. You’ll also get valuable insights into caring for your new epoxy floor—like which cleaning products to use and how to handle minor repairs if they ever pop up. It’s not just about the install; it’s about the long-term relationship you’ll have with your floor.
Closing Thoughts
Epoxy flooring is one of the most versatile and long-lasting upgrades you can make to your home or business. Whether you’re starting with bare concrete or an older floor covered in tile or vinyl, there’s a path to achieving a gleaming, durable epoxy surface. The crucial ingredient is knowledge. Know your substrate, understand its condition, and don’t cut corners on prep.
Port St. Lucie’s climate demands extra vigilance for moisture control and temperature management. That’s where a reliable local contractor like Floor Kings shines. They can customize their process to your specific environment, usage needs, and aesthetic preferences. The end result is a floor that not only looks fantastic but stands up to the rigors of daily life in Florida.
If you’re ready to take the plunge, gather your questions, do a little research, then reach out for a professional consultation. Epoxy might be the best choice you ever made for your floors, but it’s a decision that’s worth doing right the first time. In the end, you’ll be able to walk across that glossy surface with confidence, knowing you have a floor that’s both form and function at its finest.
Contact Information for Floor Kings
You can connect with Mike at 772-370-7938 or send an email to [email protected]
He’ll guide you through all your epoxy flooring considerations and help make your vision a reality.