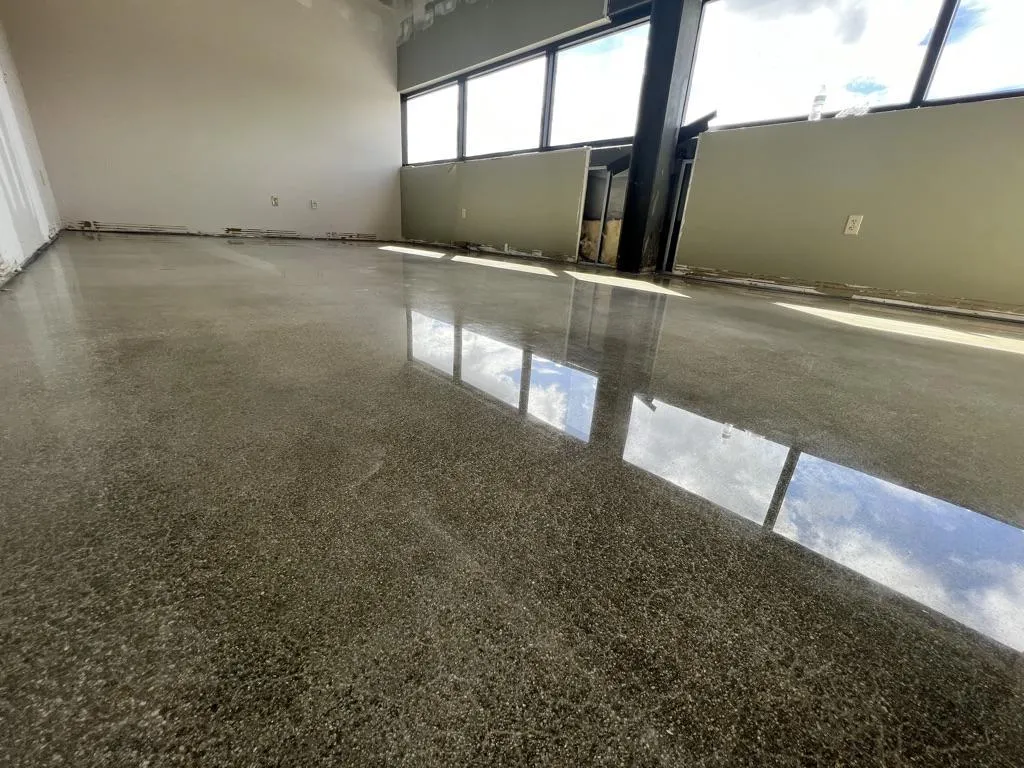
Grind & Seal vs. Polished Concrete: What’s the Difference—and Which One’s Right for Your Floor in Port St. Lucie?
Grind & Seal vs. Polished Concrete—Why It Matters
Here’s something we see all the time in Port St. Lucie: a customer calls thinking they want “polished concrete,” but when we show up, what they actually need—or already have—is a grind & seal. Or worse, they’ve been sold a cheap sealer job that’s already peeling, all because someone told them it was “just like polished concrete.”
Let’s clear something up right now—grind & seal and polished concrete are not the same thing. They may look similar when they’re first installed, but they perform very differently over time. And choosing the wrong one can leave you stuck with re-coating cycles, maintenance headaches, or floors that just don’t hold up.
So why do people confuse the two? Simple: a lot of contractors don’t explain the difference. Some don’t even know the difference. They throw around buzzwords like “polished,” “sealed,” “glossy,” and “industrial finish” like they all mean the same thing. They don’t.
Polished concrete is a mechanical process—it turns your slab into the finish. There’s no coating to peel or yellow because the concrete is the floor.
Grind & seal, on the other hand, exposes the concrete but protects it with a topical coating. That coating can look sharp out the gate, but it wears faster and needs re-application every few years—especially in high-traffic spaces or outdoor environments.
Both systems have their place. But if you’re spending good money to improve your home or commercial space, it pays to understand the difference before anyone fires up a grinder.
Next up, we’ll dig into what real polished concrete is—and why it performs like no other floor system when done right.
What Is Polished Concrete?
Polished concrete isn’t a coating—it’s a transformation. When done correctly, it turns your existing slab into a clean, durable, low-maintenance floor that doesn’t rely on anything sitting on top. No sealers. No layers to peel. Just raw concrete, ground and refined to a smooth finish.
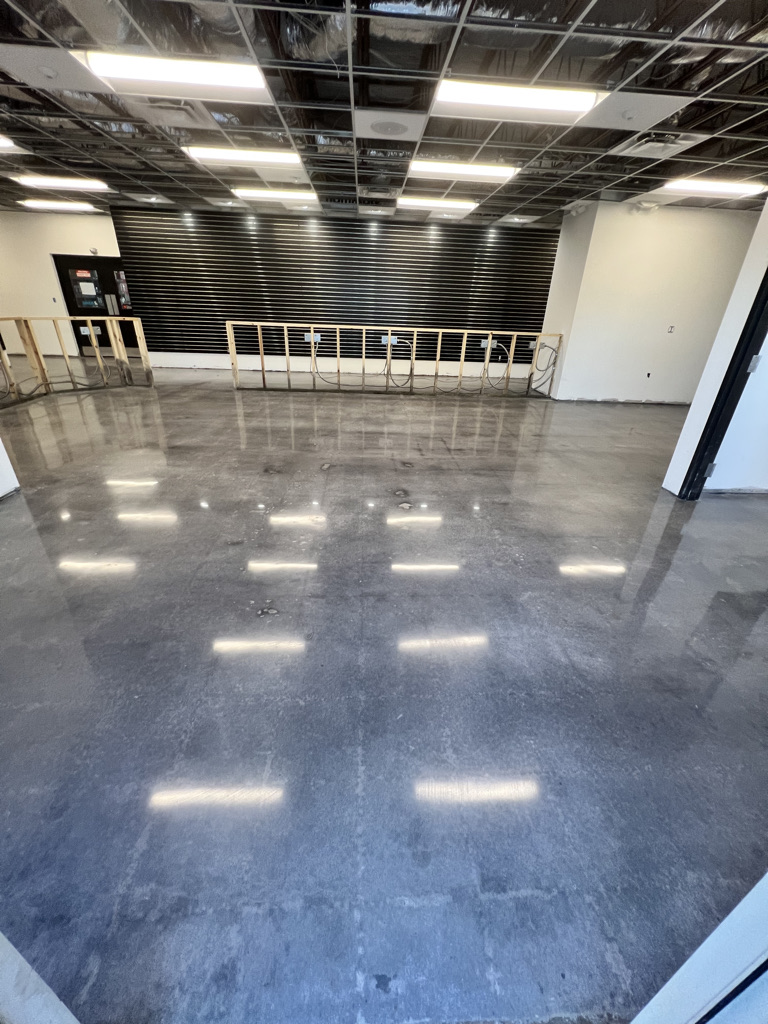
Here’s how it works: we use heavy-duty grinders with diamond tooling to cut into the surface. The grinding process removes the top layer of paste, flattens imperfections, and optionally exposes aggregate (those little stones inside the slab). Then we apply a densifier, which chemically hardens the concrete by filling in microscopic pores. After that, we polish the surface through a series of finer and finer grits—just like sanding wood, but with far more precision and muscle.
The result? A floor that reflects light, resists stains, doesn’t dust, and holds up to heavy traffic without breaking a sweat. There’s no coating to reapply, nothing to flake off, and no gloss to fake.
Polished concrete is ideal for:
Warehouses, retail spaces, and commercial facilities that need durability and cleanability.
Garages where hot tire pickup and abrasion are concerns.
Homes that want an industrial-modern look without high-maintenance flooring.
Showrooms that need a sleek, high-end aesthetic that still performs under foot traffic.
And because the polish is in the concrete, not on it, it won’t peel or yellow in the sun—and it’s incredibly easy to clean. Mop it, auto-scrub it, or just dust it off. That’s it.
But polished concrete isn’t always the right choice. Sometimes you want color. Or you need fast installation. Or you’re working with a slab that’s seen better days. That’s where grind & seal steps in—which we’ll break down next.
What Is a Grind & Seal Floor?
A grind & seal system is exactly what it sounds like: the concrete is ground to remove surface imperfections and open up the slab, and then a topical sealer is applied to protect and finish the surface. It looks similar to polished concrete when it's fresh—but under the hood, it's a totally different system.
Unlike polished concrete, which refines the concrete itself, grind & seal relies on a protective layer on top. That layer might be:
A clear acrylic (budget-friendly, but scratches easily),
A water-based or solvent-based epoxy (better durability, more chemical resistance),
Or a polyurethane or polyaspartic (higher-end, UV resistant, longer-lasting).
The key difference? That sealer is doing all the heavy lifting. If it wears out, yellows in the sun, or starts to peel—you’re left with bare, exposed concrete underneath. And it will eventually need to be stripped and reapplied, especially in high-traffic areas.
That said, grind & seal has its place, and when done right, it’s a solid choice:
Budget-conscious installs where the upfront cost of polished concrete is out of reach.
Outdoor patios and pool decks where UV-stable sealers can provide protection and gloss.
Restaurants, breweries, or creative spaces that want colored stains or a rustic industrial vibe.
Short-term commercial leases, where long-term durability isn’t necessary.
It also offers color and texture flexibility—you can stain the floor, add slip-resistant media, or use different sealers for gloss or satin finishes.
But keep this in mind: grind & seal is a coating system. It can scratch, it can peel, and it needs maintenance. If a contractor tries to pitch it as “polished concrete” without telling you it’s sealed, that’s not just misleading—it’s dishonest.
Let’s break down the differences side-by-side in the next section.
Head-to-Head: Key Differences
Alright—let’s line them up side-by-side. If you're trying to decide between polished concrete and grind & seal for your space in Port St. Lucie, here’s what actually matters when you're comparing the two.
Durability
Polished Concrete: Built to last. The concrete itself is hardened and refined—no layers to peel, nothing to fail. Holds up to forklifts, tire traffic, foot traffic, and Florida humidity.
Grind & Seal: Depends on the sealer. A high-quality urethane or polyaspartic topcoat can last a few years, but it will eventually need to be re-applied. Lower-end sealers? You’re lucky to get 12–18 months before scratches and wear show up.
Maintenance
Polished Concrete: Easy. Dust mop and damp mop. No wax, no re-coating, no nonsense.
Grind & Seal: Needs re-sealing every 2–5 years depending on foot traffic and UV exposure. Scratches more easily, and worn spots can look patchy unless maintained.
UV Stability
Polished Concrete: 100% UV stable. It’s concrete—nothing on top to yellow.
Grind & Seal: Only as UV stable as the topcoat. Acrylics and standard epoxies will yellow. Polyaspartics and specialized UV-stable sealers cost more, but hold up better outdoors or in bright sunlit areas.
Slip Resistance
Polished Concrete: Can be dialed in. Lower grit finishes offer more traction. Even high gloss can be slip-resistant if densified properly.
Grind & Seal: Varies based on topcoat and additives. Slip-resistant grit can be added to the sealer, but it often reduces visual clarity and gloss.
Cost
Polished Concrete: Higher upfront cost—but long-term savings from virtually zero maintenance and no re-coating.
Grind & Seal: Cheaper up front. Great for short-term or low-budget projects. Just be ready for ongoing upkeep.
Visuals
Polished Concrete: Natural, sleek, industrial, refined. Reflects light. Shows off the character of the slab.
Grind & Seal: Can offer color, gloss, and creative finishes—but doesn’t have the same depth or clarity as true polish.
Bottom line? If you want something long-term, low-maintenance, and built to last—go polished. If you’re on a tighter budget or need color flexibility—grind & seal might be your move.
Which One Should You Choose? Let’s Break It Down
Look, there’s no one-size-fits-all answer here. It all comes down to how the floor’s going to be used, how long you want it to last, and what your budget looks like.
Want a floor you can pretty much forget about for the next 10+ years?
Go polished. It’s more up front, sure—but you’ll make it back in savings from not having to reseal, recoat, or replace anything. That makes it ideal for warehouses, retail, commercial offices, homes, and garages where you want clean, durable, and professional-looking floors with minimal upkeep.
Need something that looks good without breaking the bank?
Grind & seal might be the right call—especially if it’s a short-term space, a residential patio, or a creative studio where you want more control over colors and gloss. It’s also a solid option for outdoor or UV-exposed areas, as long as you go with a UV-stable sealer like a polyaspartic or polyurethane.
Still not sure?
That’s where a good contractor (read: someone who actually knows both systems) earns their keep. At Floor Kings, we don’t walk into a space with a one-size-fits-all pitch. We look at the slab, ask the right questions, and then recommend the system that’s right for your needs—not just the one that’s easiest to sell.
Because at the end of the day, it’s not about which system is “better.” It’s about what’s going to work best for your space, your goals, and your timeline—without creating maintenance problems down the road.
Don’t Gamble on Guesswork. Call Floor Kings.
Choosing between polished concrete and grind & seal isn’t something you should have to figure out alone—and you definitely shouldn’t have to rely on a contractor who’s just pushing what’s easiest or most profitable for them.
At Floor Kings, we do it differently. We’ve installed both systems all over Port St. Lucie—from garages and restaurants to warehouses and retail spaces—and we know exactly when each one makes sense. No sales pitch. No upsell. Just a straight answer based on your floor, your space, and your long-term goals.
Want to know what’s right for your concrete?
Call Mike at 772-370-7938 or send a message to [email protected]. We’ll set up a time to walk your slab, talk through your options, and build a plan that fits—whether it’s a long-lasting polish or a clean, sealed finish that fits your budget.
We don’t do guesswork. We do great floors. Let’s make yours the next one.