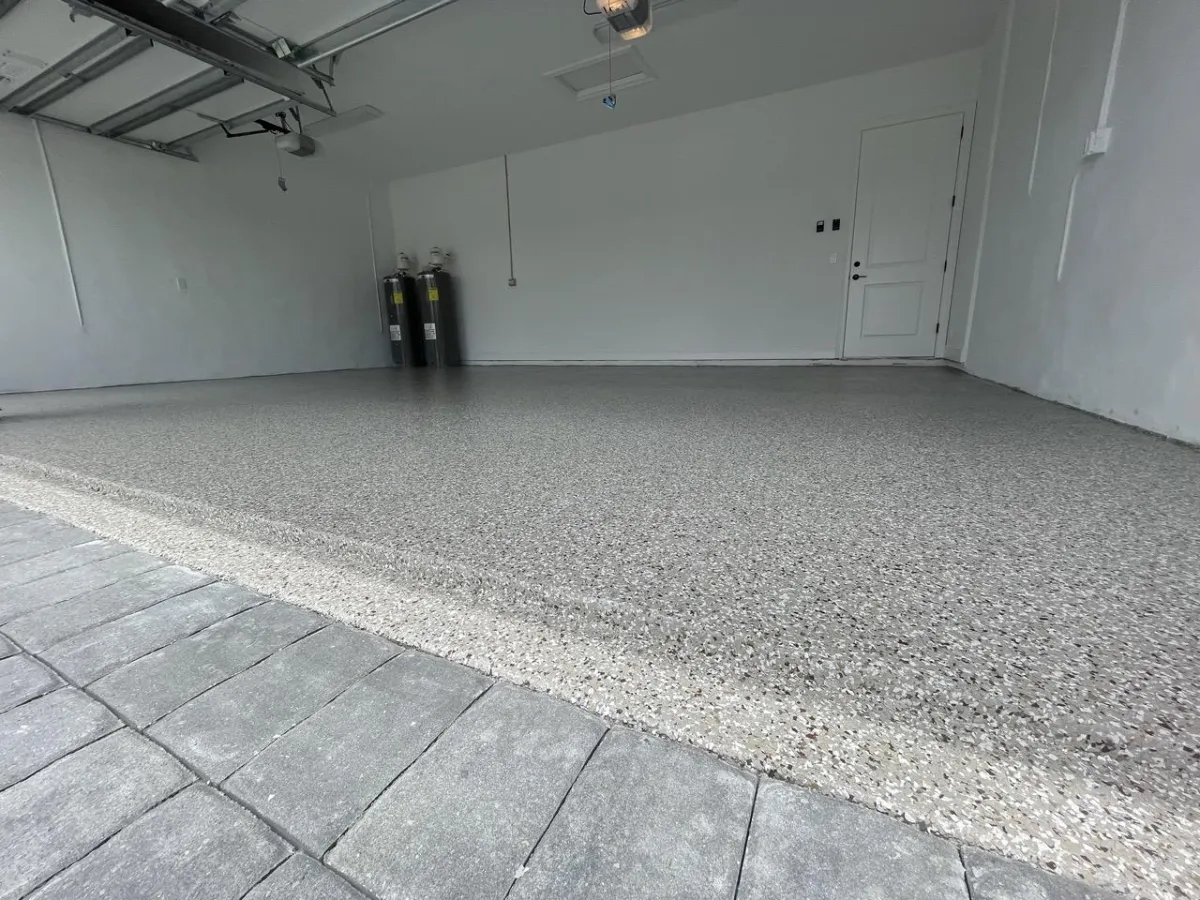
How Much Does Epoxy Flooring Cost in Port St. Lucie, FL?
If you’re thinking about upgrading your garage, shop, or commercial space with epoxy flooring, the first question that probably comes to mind is: “What’s it going to cost me?” Fair enough — budget matters. But here’s the thing: epoxy isn’t a one-size-fits-all product, and the final number depends on a lot more than just square footage.
At Floor Kings, we get asked this question all the time. And while we’d love to toss out a quick quote over the phone, doing it right means understanding your space, your goals, and the condition of your concrete. What works for a small home garage might not cut it for a busy auto shop — and pricing reflects that.
So instead of giving you a cookie-cutter price, let’s break down what really drives epoxy flooring costs in Port St. Lucie — and how to make sure you’re getting the right system for your money.
The Short Answer: There Is No One Price
Let’s just get this out of the way: there’s no flat rate for epoxy flooring. Not in Port St. Lucie, not anywhere else. If you Google “how much does epoxy flooring cost,” you’ll find numbers ranging from $3 to $15 per square foot—and every one of them could be right or wrong depending on the job.
Here’s the reality: pricing depends on dozens of factors. Are we talking about a small one-car garage with a clean slab? Or a 2,000-square-foot commercial kitchen that needs non-slip textures, a vapor barrier, and after-hours installation? Big difference.
Even within the same neighborhood, we’ve seen one floor go in at $5.50 per square foot and the next-door neighbor’s at $10 — all because of prep work, layout, and finish choice.
So, while we can give you ballpark numbers, the only way to get a real, honest estimate is to look at your space and understand what kind of performance and finish you're expecting. Anything less is just guesswork — and guesswork leads to bad flooring.
Key Factors That Affect Epoxy Flooring Costs
If you’ve ever asked three contractors for a quote and got three wildly different numbers, you’re not alone. That’s because epoxy flooring isn’t a product — it’s a process. And like any skilled trade, the process changes based on what we’re working with.
Here’s a breakdown of the biggest cost drivers we see every week in Port St. Lucie:
1. Size and Layout of the Space
Square footage matters, but not the way you might think. Sure, a bigger space usually costs more in total — but the price per square foot often drops with volume. That’s because setup, mixing, mobilization, and cleanup are part of every job, whether it’s 200 or 2,000 square feet.
Now, if your space has tight corners, built-ins, or awkward transitions, that adds labor. A wide-open garage is faster to coat than a cluttered back room with multiple thresholds and drain slopes.
2. Condition of the Concrete
This is a big one — and the one most people underestimate.
If your floor is clean, flat, and in good shape, you’re looking at standard prep. But if it’s oil-stained, cracked, spalling, or uneven, we’re talking additional steps: grinding deeper, patching, sometimes even resurfacing.
We’ve walked into garages where someone tried to DIY with paint or acid stain — and guess what? We had to remove it completely before doing it right. That adds time and material, which means a higher price tag.
Bottom line? Good prep is non-negotiable. It’s what separates a beautiful, long-lasting floor from one that peels in a year.
3. Type of Epoxy System You Choose
Not all epoxy is created equal. At Floor Kings, we install everything from basic 2-part systems for homeowners to industrial-grade polyaspartic blends for commercial clients.
Here’s a quick overview:
Solid-color epoxy: Affordable, durable, and clean-looking
Flake systems: Great for garages — hides dirt, adds grip, looks sharp
Metallic epoxy: High-end finish, great for showrooms and home gyms
Quartz broadcast systems: Ideal for commercial kitchens or wet areas where slip-resistance is key
Each system has different material and labor costs. Want a showroom-quality finish with three coats and a UV-stable top layer? That’s going to cost more than a single coat in a utility room.
4. Slip Resistance & Specialty Additives
Safety features and performance upgrades can add to your investment, especially in commercial or high-traffic environments.
For example:
Anti-slip textures for wet areas
Chemical-resistant coatings for auto shops or warehouses
Antimicrobial or food-safe options for restaurants and kitchens
These aren’t always necessary in residential spaces — but when they are, they’re worth every penny.
5. Scheduling, Access & Local Conditions
Sometimes it’s not the floor — it’s the logistics. Need us to install after business hours? Is the site in a gated community with limited access hours? Are we working in July humidity when moisture mitigation matters?
In Port St. Lucie, timing matters. Concrete reacts to heat and humidity, which means our prep and cure windows need to be precise. Getting it wrong can cost you later.
Every one of these variables — from the slab you’re starting with to the final finish — plays into the price. And that’s why we don’t do one-size-fits-all quotes. It’s not just about square footage — it’s about the full scope of the job.
Why Epoxy Flooring Costs Can Vary So Much
By now, you’ve probably figured out that epoxy flooring pricing isn’t black and white — and that’s the honest truth. What one homeowner pays can be wildly different from what the business down the road pays, even if their spaces are the same size.
The biggest reason? Prep work. If your concrete slab is clean, level, and ready to go, the job moves fast and the material goes down clean. But if it’s cracked, stained, or was previously painted or coated, we’re not just installing epoxy — we’re fixing the floor first. That adds time, labor, and materials.
Then there’s the type of epoxy system being installed. A single-coat epoxy in a residential utility room isn’t going to cost the same as a full flake broadcast system in a high-end garage or a polyaspartic topcoat in a commercial setting. The look, durability, and performance you want all factor into the final price.
And of course, there are logistical things people don’t always think about—tight working areas, poor access, jobsite restrictions, or specific installation windows.
So if you’re comparing prices online or between contractors, make sure you’re comparing more than just the number. Ask what’s included, what kind of prep is being done, and whether the product being used actually fits your space. That’s the only way to know if you’re getting a good deal — or a shortcut that might not last.
Cheap vs. Quality: Why Low Prices Can Cost You
We’ve all seen it — the guy advertising “epoxy floors” for a couple bucks a square foot. Sounds like a deal, right? Until that floor starts peeling six months later and you’re stuck paying someone else to rip it out and do it right.
Here’s the hard truth: most of the cost in a quality epoxy job isn’t the epoxy — it’s the prep. Grinding the surface properly, patching damage, applying the right primer, mixing the resin correctly — these steps take time, experience, and professional equipment. Cut corners here, and the floor might look good for a week, but it won’t last.
Low-cost installers often skip surface prep entirely or use the wrong type of product for the space. We've seen them roll on a thin coat of big-box-store epoxy paint over unprepped concrete and call it a day. That’s not professional epoxy — that’s a temporary Band-Aid.
If you're investing in epoxy flooring, do it once and do it right. It’ll cost more upfront, but you won’t be dealing with bubbles, peeling, or failed coatings a year from now. That’s where Floor Kings earns their name — delivering long-term results that hold up, even in tough Florida conditions.
Why Port St. Lucie Conditions Matter
Epoxy flooring in Florida isn’t the same as epoxy flooring in, say, Arizona or New York. Port St. Lucie has its own set of challenges—and if your installer doesn’t understand them, you could be setting yourself up for early failure.
Start with humidity. South Florida’s moisture levels can wreak havoc on concrete slabs. If a proper moisture barrier isn’t installed—or if the surface isn’t prepped with local climate in mind—you’ll start seeing bubbling, delamination, or discoloration.
Then there’s heat and UV exposure. Garages and outdoor areas in Port St. Lucie see a ton of sunlight, especially when those garage doors are left open. Not all epoxy systems are built to withstand that kind of abuse. Using the wrong topcoat can lead to yellowing, chalking, or fading.
At Floor Kings, we use materials and methods that are tested for Florida's climate. That’s the difference between a floor that lasts 3 years and one that holds up for 15.
Get a Quote That Makes Sense for Your Space
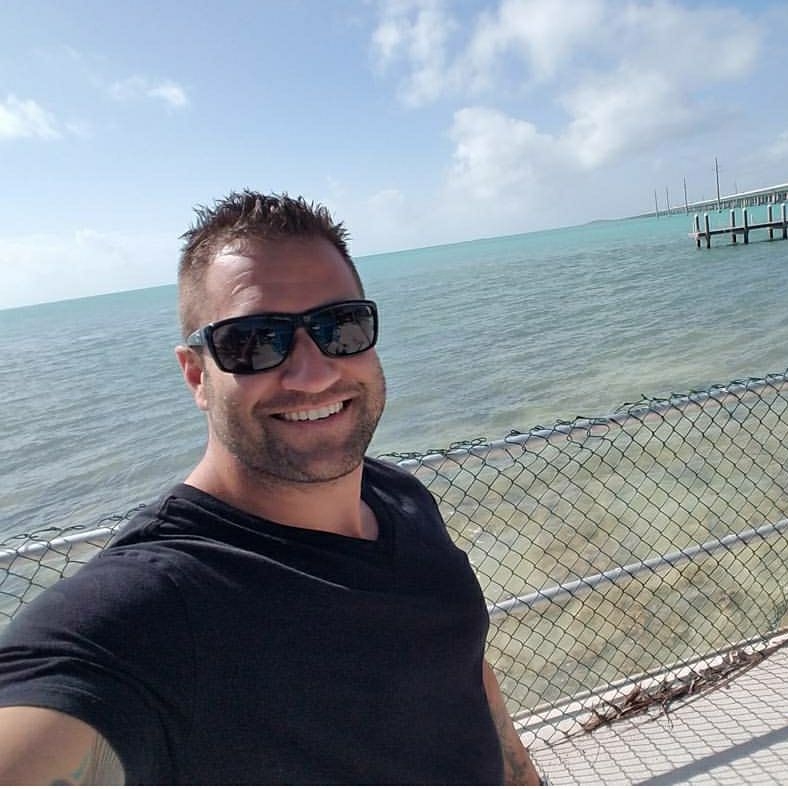
If you’re serious about epoxy flooring, the best thing you can do is stop guessing. No online calculator or national average can account for your concrete, your goals, and your layout — especially here in Port St. Lucie.
At Floor Kings, we don’t believe in one-size-fits-all pricing. We believe in honest estimates, based on what we see on-site and what you actually need. No upsells. No surprise charges. Just straightforward numbers and expert recommendations.
Give us a call 772-370-7938
Email us [email protected]
We’ll take a look and tell you what it’ll take to get the job done right — the first time.