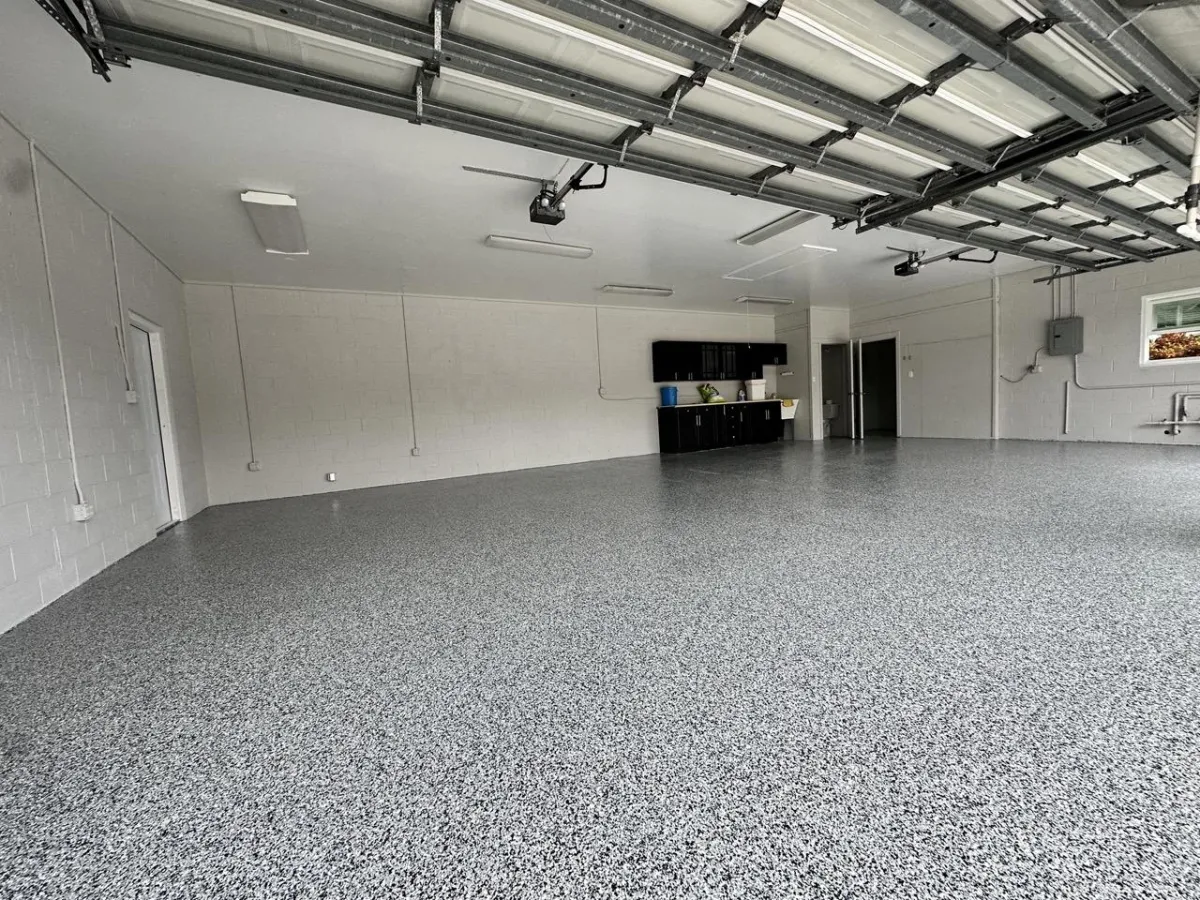
How to restore damaged polished concrete and epoxy flooring
Restoring Polished Concrete and Epoxy Floors: A Complete Guide
Polished concrete and epoxy floors are some of the most durable and long-lasting flooring options available, but even they can show signs of wear over time. Whether it’s from heavy foot traffic, improper installation, harsh cleaners, natural disasters, or simple aging, damaged floors don’t necessarily need to be replaced—most can be fully restored with the right techniques. In this guide, we’ll cover every possible type of floor damage and explain the best methods for restoring polished concrete and epoxy flooring to like-new condition.
Table of Contents
1️⃣ Common Causes of Polished Concrete and Epoxy Floor Damage
Aging Floors – Loss of shine, surface wear, minor scratches
Improper Installation Issues – Uneven finish, bubbling epoxy, weak adhesion
Harsh Chemicals & Cleaning Mistakes – Etching, dulling, and surface degradation
Natural Disasters & Environmental Damage – Water, fire, hurricanes, and foundation shifts
Heavy Equipment & Mechanical Impact – Chipping, cracks, and surface dents
UV Damage & Fading – Sunlight exposure leading to yellowing or discoloration
2️⃣ How to Restore Polished Concrete Floors
Step 1: Assessing the Damage – Identifying surface issues, deep cracks, and wear patterns
Step 2: Grinding & Honing – Restoring smoothness and prepping for resealing
Step 3: Polishing & Densifying – Reapplying densifiers for durability
Step 4: Sealing & Protecting – Choosing the right sealers for long-term performance
3️⃣ How to Restore Epoxy Floors
Step 1: Diagnosing the Issue – Peeling epoxy, adhesion failures, deep scratches
Step 2: Removing the Damaged Coating – Grinding, chemical stripping, or mechanical removal
Step 3: Surface Repair – Filling cracks, addressing moisture problems
Step 4: Reapplying Epoxy – Choosing the best epoxy type (100% solids, water-based, metallic)
Step 5: Adding Protective Topcoats – UV-resistant and impact-resistant finishes
4️⃣ Preventative Maintenance: How to Keep Your Floors Looking Like New
Daily & Weekly Cleaning Best Practices – Proper cleaning techniques and products to use
Avoiding Common Mistakes – Harsh chemicals, excessive water, improper scrubbing tools
Routine Inspections & Minor Touch-Ups – Spot repairs and early intervention
How Often to Schedule Professional Maintenance – Polished concrete vs. epoxy
5️⃣ When to Call a Professional for Floor Restoration
Signs You Need Expert Help – Deep cracks, peeling coatings, severe discoloration
Why DIY Fixes Sometimes Fail – When home remedies aren’t enough
Cost of Restoration vs. Full Floor Replacement – When repair is the better investment
6️⃣ Why Choose Floor Kings for Polished Concrete & Epoxy Floor Restoration in Port St. Lucie
Proven Expertise in Polished Concrete & Epoxy Repair
Fast, Reliable, and Affordable Restoration Solutions
Custom Solutions for Homes, Businesses, and Industrial Properties
Free Inspections & Consultations
7️⃣ Restoring Your Floors Is Easier Than You Think
Most polished concrete and epoxy floors can be restored without full replacement.
Common causes of damage can be repaired with grinding, resealing, and reapplying coatings.
Proper maintenance ensures your floors last 20+ years.
Need expert help? Contact Floor Kings today!
1. Common Causes of Polished Concrete and Epoxy Floor Damage
Polished concrete and epoxy floors are some of the most durable flooring options available, but no surface is completely indestructible. Over time, exposure to heavy traffic, chemicals, weather conditions, and poor maintenance can cause wear, cracks, peeling, or dulling. While these issues don’t always require a full floor replacement, identifying the root cause is essential for effective restoration.
Below are the most common reasons polished concrete and epoxy floors get damaged, along with how to recognize the problem and the best solutions for restoration.
1.1 Aging Floors: When Wear and Tear Takes Its Toll
Over time, even the best flooring starts to show signs of wear—especially in high-traffic areas. Polished concrete gradually loses its shine, while epoxy coatings may become dull or start to thin out.
Signs of Aging Floors
Dull, lifeless appearance—less reflectivity in polished concrete
Small surface scratches and scuff marks
Light staining from spills that no longer wipe away easily
Minor surface pits or exposed aggregate
Why It Happens
Polished concrete: Natural wear from foot traffic, dirt, and improper cleaning techniques gradually dulls the surface.
Epoxy floors: The topcoat wears down over time, reducing stain resistance and sheen.
How to Fix It
Polished Concrete: A light re-polish with fine diamond abrasives (800 to 3,000 grit) restores the sheen. Applying a penetrating sealer helps maintain durability.
Epoxy Flooring: A fresh topcoat or recoating can restore shine and protective properties.
1.2 Improper Installation: When Shortcuts Lead to Big Problems
If polished concrete or epoxy flooring wasn’t installed correctly, problems can start showing up within months instead of years.
Signs of Improper Installation
Uneven finish—visible variations in sheen or texture
Epoxy bubbles, peeling, or weak adhesion
Polished concrete has an inconsistent gloss or cloudy appearance
Why It Happens
Inadequate surface preparation before applying epoxy or polishing concrete
Skipping moisture tests, leading to bonding failures
Not following curing times—rushing the installation process weakens adhesion
How to Fix It
Polished Concrete: Requires re-grinding and re-polishing to even out the surface.
Epoxy Flooring: The failed layer must be completely removed (via grinding or chemical stripping) before reapplying epoxy properly.
1.3 Harsh Chemicals & Cleaning Mistakes
Polished concrete and epoxy are low-maintenance, but using the wrong cleaning products can severely damage them.
Signs of Chemical Damage
Dull, etched, or cloudy surface (polished concrete)
Epoxy starts to peel, fade, or lose its topcoat protection
Stains that won’t wipe away or appear to have "burned" into the surface
Why It Happens
Acidic cleaners (like vinegar or bleach) eat away at concrete’s protective sealers.
Degreasers and ammonia-based cleaners strip epoxy’s topcoat.
Over-wetting concrete floors can lead to surface deterioration.
How to Fix It
Polished Concrete: Use a neutral pH cleaner, then apply a polishing compound or reapply a penetrating sealer.
Epoxy Flooring: If the topcoat is stripped, a new topcoat application can restore shine and protection.
1.4 Natural Disasters & Water Damage
Flooding, fire, and foundation shifts can all take a toll on concrete and epoxy floors.
Signs of Natural Disaster Damage
Flood damage: Water seeping into cracks, causing flaking or spalling (pieces breaking off)
Fire damage: Discoloration, weakened surface strength, or charred areas
Foundation shifts & earthquakes: Large cracks, uneven surfaces, or peeling epoxy
Why It Happens
Water infiltration weakens concrete, making it more porous.
Extreme heat from fires can cause surface damage and require deep grinding to restore.
Structural shifts cause cracking and detachment of coatings.
How to Fix It
Polished Concrete: If water damage has caused severe deterioration, deep grinding and repolishing may be needed. Cracks can be filled with epoxy crack fillers.
Epoxy Flooring: Water-damaged epoxy often requires complete removal and reapplication with a moisture-resistant primer.
1.5 Heavy Equipment & Mechanical Impact Damage
Industrial environments, garages, and warehouses put floors under extreme stress. Dropped tools, forklifts, and dragging pallets can lead to cracks, dents, and chips.
Signs of Mechanical Damage
Concrete cracks & pitting (small holes forming in the surface)
Deep scratches or gouges in epoxy coatings
Epoxy peeling up in sections due to impact
Why It Happens
Heavy loads and dropped objects cause surface fractures.
Pallet jacks and forklifts create impact points and tire marks.
Dragging furniture or equipment over epoxy can lead to scratches and scuffs.
How to Fix It
Polished Concrete: Small chips can be filled and blended, while large areas may require re-grinding and repolishing.
Epoxy Flooring: Deep scratches and chips need patch repairs before recoating.
1.6 UV Damage & Fading (For Outdoor Spaces & Bright Interiors)
Sunlight exposure can cause polished concrete and epoxy floors to fade or discolor over time.
Signs of UV Damage
Polished concrete appears lighter or "washed out" in sun-exposed areas
Epoxy coatings turn yellow (especially in garages or outdoor areas)
Glossy finishes appear dull and uneven in UV-exposed sections
Why It Happens
Epoxy coatings that aren’t UV-resistant gradually turn yellow.
Outdoor polished concrete loses vibrancy due to weather exposure.
Sunlight accelerates oxidation, affecting some sealers.
How to Fix It
Polished Concrete: Apply a UV-resistant sealer to protect against fading.
Epoxy Flooring: If yellowing occurs, remove and reapply a UV-stable epoxy topcoat.
2. How to Restore Polished Concrete Floors
Polished concrete is one of the most durable flooring options available, but even the strongest surfaces require maintenance and restoration over time. Whether your floor has lost its shine, developed cracks, or suffered from chemical damage, restoration can bring it back to like-new condition without the need for a full replacement.
The restoration process depends on the extent of the damage. Minor issues like dullness and light scratches can be resolved with a simple repolish, while deeper problems like cracks and surface deterioration may require grinding, patching, and resealing.
This section covers a step-by-step guide to restoring polished concrete floors, from assessing the damage to resealing and maintaining your restored surface.
2.1 Step 1: Assessing the Damage
Before beginning the restoration process, it’s important to determine the extent of wear and damage. The right repair method depends on whether the problem is surface-level (dullness, light scratches) or structural (cracks, deep stains, spalling).
Signs Your Polished Concrete Needs Restoration
Loss of shine and reflectivity
Surface scratches, scuff marks, or minor pitting
Stains from chemicals, oils, or harsh cleaners
Cracks or chips forming in the concrete
Dusting (fine concrete particles accumulating on the surface)
Water damage or efflorescence (white mineral deposits)
How to Evaluate the Floor
Water Test: Pour a small amount of water on the surface. If it absorbs quickly instead of beading up, the protective sealer is worn out.
Scratch Test: Run a metal object over the surface. Light scratches indicate wear, while deeper gouges may require patching.
Moisture Test: Use a moisture meter to check if water infiltration has weakened the slab.
If the damage is minor, polishing and resealing may be enough. For moderate to severe damage, grinding, patching, and densifying will be required.
2.2 Step 2: Grinding & Honing the Surface
If the concrete is dull, scratched, or uneven, mechanical grinding and honing will remove imperfections and prepare the surface for repolishing.
Choosing the Right Grit for Grinding
200 to 400 grit – Removes deep scratches, stains, and surface contamination.
800 to 1,500 grit – Restores moderate dullness, bringing back light reflectivity.
3,000 grit – Achieves a high-gloss, mirror-like finish.
Process for Grinding Polished Concrete
Deep Restoration (Severely Worn Floors)
Start with coarse grinding (40-100 grit) to remove surface damage.
Progress to medium grit (200-400 grit) to refine the finish.
Intermediate Restoration (Moderately Dull Floors)
Begin with 400-800 grit for moderate wear.
Follow with 1,500-3,000 grit to restore full gloss.
Light Restoration (Minimal Damage)
Skip coarse grinding and polish directly with 800-3,000 grit to refresh the surface.
Proper dust extraction is essential during grinding to prevent airborne particles from settling into the floor.
2.3 Step 3: Filling Cracks, Chips, and Surface Defects
For cracked or chipped concrete, repairs must be made before polishing to ensure a smooth, even surface.
How to Repair Cracks in Polished Concrete
Small Cracks (< 1/8 inch): Use a concrete crack filler or epoxy-based patching material.
Larger Cracks (> 1/8 inch): Fill with a polyurea or epoxy-based crack repair compound for added durability.
Spalling & Surface Pitting: Use a self-leveling concrete repair product before grinding and polishing.
Once the repairs have cured, the area is re-ground to blend seamlessly with the surrounding concrete.
2.4 Step 4: Applying a New Polishing Compound & Densifier
After grinding, a densifier is applied to strengthen the concrete and prepare it for polishing.
Why Use a Densifier?
Increases surface hardness – Helps prevent dusting and wear.
Enhances stain resistance – Reduces porosity for better protection against spills.
Extends the lifespan of the polished surface – Reduces future maintenance.
2.5 Step 5: Polishing & Refinishing the Surface
Once the floor is properly densified, polishing begins using progressively finer abrasives. The goal is to restore the desired sheen level, whether matte, satin, or high-gloss.
Polishing Levels
Matte (400 grit) – Soft, low-sheen finish for industrial and high-traffic areas.
Satin (800-1,500 grit) – Moderate gloss with improved reflectivity.
High-Gloss (3,000 grit) – Mirror-like finish with a sleek, modern appearance.
Polishing is performed using resin-bond diamond pads, and the process typically requires 3-5 passes with increasingly finer abrasives.
2.6 Step 6: Sealing & Protecting the Surface
The final step is applying a sealer to protect the polished surface from stains, moisture, and wear.
Types of Sealers for Polished Concrete
Penetrating Sealers – Absorb into the concrete without altering its appearance. Best for matte or satin finishes.
Acrylic Sealers – Provide a light sheen and enhance stain resistance.
Polyurethane or Epoxy Sealers – Create a protective barrier, ideal for high-traffic commercial spaces.
The sealer is applied with a microfiber mop or sprayer, then allowed to cure for 24 to 48 hours before the floor is used.
2.7 Step 7: Maintaining Restored Polished Concrete Floors
To keep the restored floor looking new:
Sweep and mop regularly with a neutral-pH cleaner.
Avoid acidic or ammonia-based cleaners that degrade sealers.
Use soft pads for buffing instead of abrasive brushes.
Reapply sealer every 3-5 years to maintain protection.
Proper maintenance extends the lifespan of polished concrete, reducing the need for frequent restoration.
3. How to Restore Epoxy Floors
Epoxy flooring is highly durable and resistant to most types of damage, but over time, wear and tear, improper installation, and exposure to chemicals or heavy impact can cause peeling, chipping, fading, or even full delamination (when the epoxy coating separates from the concrete). Fortunately, most epoxy floor issues can be fixed without replacing the entire system.
The restoration process depends on the type and severity of the damage. In some cases, a simple topcoat reapplication is enough, while in others, the floor may require complete removal and resurfacing.
This section outlines a step-by-step process for restoring epoxy floors, including how to diagnose the issue, repair localized damage, and recoat the surface for long-term durability.
3.1 Step 1: Identifying the Type of Epoxy Damage
Before starting restoration, it’s important to diagnose the specific problem affecting the epoxy floor.
Common Epoxy Floor Issues and Their Causes
Epoxy floors can experience several types of damage over time. Identifying the specific issue is crucial for determining the right restoration approach.
Peeling or Bubbling Epoxy – This occurs when sections of the epoxy start lifting from the concrete, or blisters form beneath the coating. The most common causes are improper surface preparation, moisture issues, or trapped air during installation.
Cracking or Chipping – If there are visible cracks, chips, or gouges in the epoxy surface, it is likely due to impact damage, shifting concrete, or a weak epoxy application that didn't bond properly.
Fading & Discoloration – When epoxy coatings begin to turn yellow, white, or dull, the primary culprits are UV exposure, chemical reactions, or the use of non-UV-stable epoxy products that degrade under sunlight.
Chemical Damage – Stains, softening, or etching of the epoxy surface often result from spills of harsh chemicals like acids, solvents, or industrial cleaners that break down the epoxy’s protective properties.
Loss of Gloss – If the epoxy looks dull and lacks its original reflectivity, it is likely due to surface abrasion, frequent use of harsh cleaning agents, or general lack of maintenance over time.
Once the specific issue is identified, the appropriate restoration method can be applied to bring the floor back to its original condition.
3.2 Step 2: Removing the Damaged Epoxy Layer
If the epoxy coating is peeling, bubbling, or has widespread wear, the old layer must be removed before reapplication.
Methods for Removing Epoxy Flooring
Diamond Grinding – Best for large areas of peeling or worn-out epoxy. A floor grinder equipped with diamond abrasives removes the epoxy while prepping the concrete for a new coat.
Chemical Stripping – Used for small areas of epoxy removal. A specialized epoxy remover softens the coating for easier removal.
Shot Blasting – Suitable for industrial settings. A machine blasts steel beads at high velocity to remove epoxy quickly.
For localized damage, such as a small peeling section, only that portion may need to be removed before repairs begin.
3.3 Step 3: Repairing the Substrate (Concrete Base)
Once the damaged epoxy is removed, the underlying concrete must be inspected and repaired before applying a new coating.
Concrete Surface Repairs Before Epoxy Application
Cracks & Chips: Filled with epoxy crack filler or polyurea joint compound.
Surface Pitting & Holes: Use a self-leveling concrete repair product to create a smooth finish.
Moisture Issues: If water damage is present, apply a moisture vapor barrier to prevent future adhesion failures.
A properly prepped surface ensures the new epoxy coating will adhere correctly and last longer.
3.4 Step 4: Reapplying Epoxy Coating
Once the substrate is repaired, a new epoxy layer is applied to restore the floor. The choice of epoxy type depends on the intended use and required durability.
Choosing the Right Epoxy for Restoration
100% Solids Epoxy – Best for industrial and high-traffic areas, offering maximum durability.
Water-Based Epoxy – Good for light-duty applications and residential spaces.
Solvent-Based Epoxy – Provides a strong bond but has higher VOC emissions.
Metallic & Decorative Epoxy – Used for showrooms, retail spaces, and custom aesthetics.
Clear Epoxy Over Concrete – Ideal for achieving a polished concrete look with epoxy’s benefits.
Application Process
Primer Coat – A bonding agent that ensures adhesion to the concrete.
Base Coat – The main epoxy layer, applied evenly across the surface.
Optional Decorative Elements – Color flakes, metallic effects, or custom textures can be added.
Topcoat – A protective layer that enhances durability and stain resistance.
Epoxy is typically applied using a squeegee and roller, with drying times ranging from 12 to 24 hours per coat.
3.5 Step 5: Adding Protective Topcoats & Enhancements
To extend the life of the newly restored epoxy floor, a topcoat should be applied for added protection.
Types of Topcoats for Epoxy Floors
UV-Resistant Topcoat – Prevents yellowing from sun exposure.
Polyurethane Topcoat – Provides extra scratch resistance for high-traffic areas.
Anti-Slip Additive – Mixed into the topcoat to improve traction in wet environments.
Chemical-Resistant Sealers – Protect against spills of oils, acids, and cleaning chemicals.
Adding a topcoat ensures the epoxy floor remains glossy, durable, and resistant to everyday wear.
3.6 Step 6: Maintaining Restored Epoxy Floors
Proper maintenance helps extend the life of a restored epoxy floor and prevents premature wear.
Best Practices for Epoxy Floor Maintenance
Sweep and mop regularly to remove dust and debris.
Use pH-neutral cleaners to avoid breaking down the topcoat.
Avoid dragging heavy objects that could scratch or gouge the surface.
Apply a refresher coat every 5-7 years in high-traffic areas.
Routine maintenance keeps the epoxy looking its best and reduces the frequency of major restorations.
Restoring epoxy flooring is a cost-effective alternative to full replacement and can be done for a variety of issues, including peeling, cracking, chemical damage, and discoloration. The key to a successful restoration is proper surface preparation, high-quality epoxy application, and the use of protective topcoats.
Next, we’ll cover preventative maintenance strategies to ensure polished concrete and epoxy floors stay in peak condition for years to come.
4. Preventative Maintenance: How to Keep Your Floors Looking Like New
Polished concrete and epoxy floors are designed for durability, but proper maintenance is essential to ensure they remain in top condition. While these flooring systems require less upkeep than traditional materials like wood or tile, neglecting regular care can lead to dullness, scratches, stains, or premature wear. Implementing a routine cleaning and maintenance schedule helps extend the lifespan of the flooring, maintain its appearance, and prevent the need for costly restoration.
4.1 Best Cleaning Practices for Polished Concrete and Epoxy Floors
The foundation of good maintenance is regular cleaning using the correct methods and products. A daily routine helps remove dust and debris, while deeper cleaning should be done periodically to prevent buildup and preserve the protective surface.
For daily cleaning, polished concrete and epoxy floors should be swept or dust mopped to remove dirt, sand, and other particles that could scratch or wear down the surface. Using a microfiber mop or a dust mop is recommended to avoid dragging rough debris across the floor.
A weekly damp mopping is effective for removing residues that accumulate over time. It’s important to use a neutral pH cleaner, as harsh chemicals, acidic solutions, and ammonia-based products can break down the protective sealer on polished concrete and dull the gloss on epoxy coatings. A soft mop or an auto-scrubber with non-abrasive pads should be used to prevent surface damage.
Spills should always be wiped up immediately, as leaving liquids on the floor for prolonged periods can lead to staining or damage. This is especially true for oil, grease, acids, or strong cleaning agents, which can react with the floor’s coating and compromise its durability.
4.2 Avoiding Common Mistakes That Can Damage Floors
Even with a good cleaning routine, certain maintenance mistakes can accelerate wear and tear. Understanding what to avoid can help protect the flooring and reduce the need for frequent restoration.
One common mistake is using abrasive scrubbers or harsh cleaning tools. On polished concrete, abrasive pads can dull the surface, reducing its reflectivity. For epoxy floors, scrubbing with hard bristles or steel wool can create micro-abrasions, making the surface more susceptible to staining and chemical damage.
Another issue arises when heavy furniture or equipment is dragged across the floor. This can leave scratches or gouges, especially on epoxy coatings. To prevent this, furniture should be lifted when moved or placed on felt pads to minimize friction.
On polished concrete, failure to reapply sealer as needed can lead to surface deterioration. Over time, the protective layer wears down, leaving the floor more vulnerable to stains and moisture infiltration. Resealing should be scheduled periodically to maintain durability.
For epoxy floors, exposure to prolonged moisture or standing water can be damaging, particularly if the epoxy was not properly installed with a moisture barrier. Keeping the surface dry and addressing any water leaks immediately helps prevent peeling or lifting.
Additionally, parking hot tires directly on an epoxy floor—especially in garages—can cause hot tire pickup, where the heat from vehicle tires weakens the bond between the epoxy and concrete, leading to peeling or delamination. Using a protective mat or ensuring a high-quality topcoat is applied can help prevent this issue.
4.3 Routine Inspections and Minor Touch-Ups
Regular inspections allow for early detection of minor damage, preventing more extensive repairs down the line. Every few months, floors should be checked for surface wear, fading, cracks, or signs of moisture damage.
For polished concrete, small surface scratches or areas that appear dull can often be restored with light buffing or the application of a polishing compound. If the sheen is significantly reduced, professional repolishing may be required.
For epoxy flooring, checking for peeling edges, discoloration, or worn areas can help determine when a refresher coat is needed. If minor scratches or dull spots are found, applying a fresh topcoat can restore the floor’s gloss and protective properties.
Cracks in the underlying concrete should also be addressed promptly, as they can expand over time and lead to more severe structural problems. Using an appropriate crack filler before they grow larger can prevent costly repairs in the future.
4.4 How Often to Schedule Professional Maintenance
Even with regular cleaning and preventative care, both polished concrete and epoxy floors benefit from periodic professional maintenance to preserve their longevity. The frequency of professional service depends on the level of foot traffic and the overall condition of the flooring.
For polished concrete, resealing is typically recommended every three to five years, depending on wear and exposure to moisture or chemicals. High-traffic commercial spaces may need sealing more frequently, while residential floors can often go longer between applications. Light buffing and repolishing may also be needed annually to maintain the desired gloss level.
For epoxy floors, applying a new protective topcoat every two to three years helps maintain resistance to wear, chemicals, and UV exposure. In areas with heavy traffic, such as warehouses, factories, or garages, an additional recoating every five to seven years may be necessary to prevent peeling or discoloration.
Routine inspections by a professional can also identify potential issues before they become major problems, helping to extend the life of the flooring system and reduce long-term maintenance costs.
Preventative maintenance is essential to ensuring polished concrete and epoxy floors retain their durability and visual appeal. Regular cleaning, avoiding damaging habits, and scheduling periodic professional care can extend the life of the flooring while minimizing the need for costly restorations.
The next section will cover when it’s time to call a professional for floor restoration and how to decide between repair and full replacement.
5. When to Call a Professional for Floor Restoration
While regular maintenance and minor touch-ups can help preserve polished concrete and epoxy floors, there are times when professional restoration is necessary. Certain types of damage—such as deep cracks, widespread peeling, severe discoloration, or structural issues—cannot be fixed with simple cleaning or DIY solutions. Knowing when to seek professional help can prevent further deterioration and ensure the flooring remains functional and visually appealing for years to come.
This section outlines the key signs that indicate a professional restoration is needed, explains why DIY fixes may not be sufficient for certain issues, and compares the cost of restoration to full floor replacement.
5.1 Signs You Need Expert Help
There are several warning signs that polished concrete or epoxy floors require professional attention. If any of the following issues are present, it may be time to consult a specialist.
For Polished Concrete Floors
Deep cracks or structural fractures – Small surface cracks can sometimes be patched, but large, deep cracks may indicate foundation movement or excessive wear that requires professional grinding and filling.
Significant dullness or uneven sheen – If polishing compounds and buffing no longer restore the shine, a full regrind and repolish may be needed.
Heavy staining that won’t lift – Chemical spills, oil penetration, or acid damage that have etched into the concrete may require grinding and resealing.
Spalling or surface deterioration – When concrete starts flaking or chipping away, the surface must be repaired and reinforced before polishing.
For Epoxy Floors
Large areas of peeling or bubbling – If the epoxy is lifting from the concrete in multiple sections, the coating likely failed due to poor adhesion, moisture issues, or improper installation. A professional will need to grind away the old epoxy and reapply a fresh layer.
Extensive cracking or chipping – If epoxy coatings have cracked due to impact damage or substrate movement, patching alone may not be enough. A full resurfacing may be required.
Discoloration and fading – If the epoxy floor has turned yellow or lost its original color due to UV exposure or chemical reactions, a new topcoat or full recoating is often the best solution.
Loss of slip resistance – If the surface has become too smooth and slippery, a professional can apply an anti-slip additive or texture coat to restore safety.
Ignoring these issues can lead to worsening damage, requiring more extensive and costly repairs down the line.
5.2 Why DIY Fixes Sometimes Fail
While DIY methods can work for minor repairs and maintenance, attempting to restore a severely damaged floor without the right equipment or expertise can cause further problems. Some common pitfalls of DIY restoration include:
Uneven grinding or polishing – Without professional-grade machinery, it’s difficult to achieve a smooth, consistent finish on polished concrete. Improper grinding can leave visible marks or uneven sheen.
Poor epoxy adhesion – Many DIY epoxy kits fail due to improper surface preparation, leading to peeling or weak bonding. Professional installers use industrial grinders and moisture mitigation techniques to ensure proper adhesion.
Wrong choice of sealers or coatings – Not all sealers and epoxy products are the same. Using the wrong type for the specific application can result in premature wear or incompatibility with the existing floor.
Moisture-related failures – If moisture is present in the concrete slab, it can cause epoxy coatings to bubble or concrete to spall over time. Professionals perform moisture tests before applying new coatings to prevent these issues.
For serious damage or large-scale restorations, hiring a professional is the best way to ensure a high-quality, long-lasting result.
5.3 Cost of Restoration vs. Full Floor Replacement
Many property owners hesitate to restore their floors due to cost concerns, but in most cases, restoration is significantly more affordable than full replacement.
Cost Breakdown for Restoration
Polished Concrete Restoration:
Light repolishing: $1 – $3 per square foot
Grinding & resealing: $3 – $7 per square foot
Full resurfacing: $8 – $15 per square foot
Epoxy Floor Restoration:
Topcoat reapplication: $2 – $5 per square foot
Patch repairs and recoating: $4 – $8 per square foot
Full removal and new epoxy application: $8 – $15 per square foot
By contrast, full floor replacement (which involves demolishing and re-pouring a new concrete slab or installing a different flooring system) can cost $20 – $50 per square foot or more, depending on the material.
In most cases, restoring an existing floor is the better financial decision—it extends the lifespan of the current floor without the expense of total replacement.
Recognizing when professional restoration is necessary can help prevent further damage and ensure a cost-effective solution for maintaining polished concrete and epoxy floors. When floors exhibit deep cracks, peeling coatings, heavy staining, or surface deterioration, calling in a professional is the best way to restore their strength, durability, and appearance.
Next, we’ll discuss why Floor Kings is the best choice for polished concrete and epoxy floor restoration in Port St. Lucie and how they can help extend the life of your floors.
6. Why Choose Floor Kings for Polished Concrete & Epoxy Floor Restoration in Port St. Lucie
When it comes to restoring polished concrete and epoxy floors, expertise and quality workmanship matter. A poorly executed repair can lead to short-term fixes that don’t last, forcing property owners to spend even more on additional repairs or replacements. Floor Kings has built a reputation in Port St. Lucie for providing high-quality, long-lasting flooring restoration solutions for homes, businesses, and industrial properties.
Here’s why Floor Kings is the top choice for polished concrete and epoxy floor restoration in Port St. Lucie.
6.1 Expertise in Polished Concrete & Epoxy Restoration
Floor Kings specializes in both installation and restoration of polished concrete and epoxy flooring, ensuring that every repair or refinishing job is done with precision and industry-best techniques. Their team is trained in grinding, patching, repolishing, resealing, and epoxy resurfacing, allowing them to handle all types of floor damage—from surface scratches to full restoration projects.
Unlike general flooring contractors who may not have experience with advanced concrete restoration methods, Floor Kings uses specialized equipment and industrial-grade materials to ensure durability and long-term performance.
6.2 Tailored Solutions for Every Type of Floor Damage
Every flooring restoration project is different. Floor Kings takes a custom approach to each job, carefully assessing the condition of the floor, the extent of the damage, and the specific needs of the client before recommending the best restoration method.
For polished concrete floors, their services include:
Grinding & repolishing to restore the original shine
Crack and surface damage repairs to fix structural issues
Resealing and densifying for long-term protection
Custom stain or color enhancements for aesthetic improvements
For epoxy floors, their restoration services include:
Epoxy recoating and resurfacing to repair peeling or worn-out coatings
Crack and chip repairs to restore a smooth, seamless surface
Application of UV-resistant topcoats to prevent fading and discoloration
Anti-slip treatments for improved safety in high-traffic areas
By offering a full range of services, Floor Kings ensures that clients get the right solution for their specific flooring issues—without unnecessary costs or excessive downtime.
6.3 High-Quality Materials for Long-Lasting Results
Not all sealers, densifiers, or epoxy coatings are created equal. Floor Kings uses industrial-grade materials designed for maximum durability, chemical resistance, and aesthetic appeal. They select the right type of sealer, densifier, or epoxy formula based on the client’s environment, ensuring that the flooring will stand up to wear and tear for years to come.
Some of the high-performance materials used by Floor Kings include:
100% solids epoxy coatings for maximum strength and chemical resistance
Moisture-blocking primers to prevent peeling and adhesion failures
Penetrating concrete sealers that enhance stain resistance without changing the look of the floor
Polyurethane and polyaspartic topcoats for added durability in high-traffic areas
Using the right materials ensures that restored floors not only look great but also provide long-term protection against daily use, spills, and environmental exposure.
6.4 Fast, Reliable, and Cost-Effective Restoration Services
Restoring a floor shouldn’t mean weeks of downtime or an unpredictable repair process. Floor Kings is committed to efficient project completion, ensuring that floors are restored quickly without cutting corners.
Their streamlined restoration process includes:
On-Site Inspection & Consultation – A thorough evaluation to determine the best restoration approach.
Surface Preparation – Grinding, patching, or cleaning to ensure proper adhesion and a smooth finish.
Application of Polishing, Epoxy, or Sealers – Using industrial-grade equipment and materials.
Final Protective Treatments & Quality Check – Ensuring longevity and high performance.
By following proven restoration techniques, Floor Kings minimizes downtime for businesses, warehouses, and homeowners, allowing them to get back to normal operations quickly.
6.5 Free Consultations & No-Obligation Quotes
Floor Kings believes in transparency and honesty when it comes to flooring restoration. They offer free consultations and on-site inspections to help clients understand their options and get an accurate estimate before committing to a project.
Whether the project requires simple refinishing or full resurfacing, Floor Kings provides detailed explanations of the process, upfront pricing, and customized recommendations—ensuring that clients know exactly what to expect.
6.6 Local, Trusted, and Committed to Quality
As a local flooring company in Port St. Lucie, Floor Kings understands the unique challenges that Florida’s climate can pose for polished concrete and epoxy floors. High humidity, heavy foot traffic, and exposure to UV rays require specialized solutions, and Floor Kings has the experience needed to deliver results that last in this environment.
By working with a trusted local team, clients can expect:
Personalized service and direct communication
Faster response times for restoration projects
Accountability and a commitment to long-term customer satisfaction
For residential, commercial, or industrial flooring restoration, Floor Kings is the go-to choice in Port St. Lucie.
Get a Free Quote for Floor Restoration Today
If your polished concrete or epoxy flooring is worn, peeling, or losing its original look, Floor Kings can restore it to like-new condition with expert craftsmanship and high-quality materials.
Contact Floor Kings today for a free consultation and no-obligation quote.
📞 Call Mike at 772-370-7938
📧 Email: [email protected]
Restoring polished concrete and epoxy floors requires expert knowledge, the right materials, and professional execution to ensure lasting results. Floor Kings brings years of experience, industry-leading products, and a commitment to customer satisfaction to every restoration project in Port St. Lucie.
7. Restoring Your Floors Is Easier Than You Think (with the right help)
Polished concrete and epoxy floors are some of the most durable flooring solutions available, but like any surface, they require proper care and occasional restoration. Whether your floor has lost its shine, developed cracks, or suffered from peeling, restoration is a cost-effective alternative to full replacement.
Through grinding, repolishing, resealing, and resurfacing, a worn or damaged floor can be brought back to life, enhancing its durability and appearance for years to come. The key is identifying the type of damage early and using the correct restoration methods to prevent further deterioration.
Key Takeaways from This Guide
Common Causes of Damage – Floors can deteriorate due to wear and tear, improper installation, harsh chemicals, natural disasters, and heavy impact.
How to Restore Polished Concrete Floors – Grinding, repolishing, crack repair, and sealing can bring dull or damaged concrete back to a smooth, glossy finish.
How to Restore Epoxy Floors – Peeling, bubbling, fading, and cracks can be fixed by removing the damaged layer, repairing the substrate, and reapplying epoxy coatings.
Preventative Maintenance Matters – Regular cleaning, avoiding harsh chemicals, and periodic resealing can extend the life of your floors.
When to Call a Professional – Deep cracks, extensive peeling, moisture damage, or severe wear often require expert restoration to ensure lasting results.
Floor Kings is the Best Choice for Floor Restoration in Port St. Lucie – With expert craftsmanship, high-quality materials, and cost-effective solutions, Floor Kings ensures polished concrete and epoxy floors look and perform like new.
Restore Your Floors with Floor Kings Today
If your polished concrete or epoxy floors need professional restoration, now is the time to act. Whether it’s a small touch-up or a full resurfacing, Floor Kings delivers expert service with top-tier materials and industry-best techniques.
📞 Call Mike at 772-370-7938
📧 Email: [email protected]
Schedule your free consultation today and bring your floors back to life!