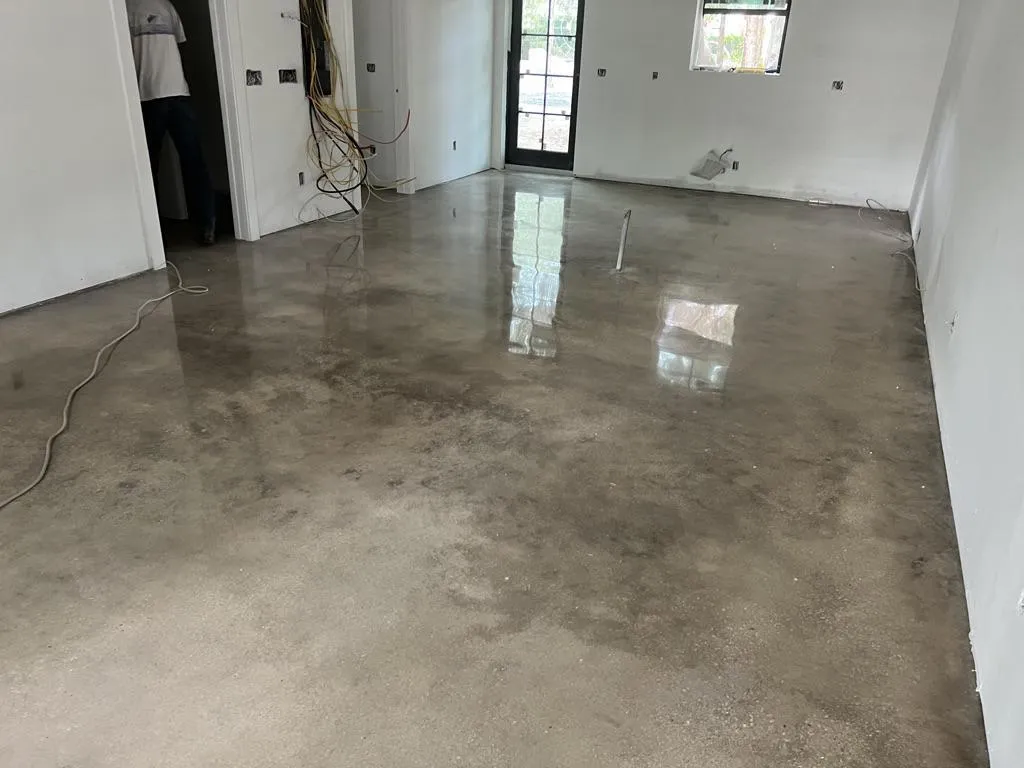
Is That Polished Concrete or Clear Epoxy
Flooring choices often set the tone for an entire space, especially in a place like Port St. Lucie where design preferences blend coastal charm with modern convenience. If you’ve ever walked into a sleek showroom or a contemporary home and wondered, “Is that polished concrete or clear epoxy?” you’re not alone. Both finishes can look remarkably similar at a glance, yet they differ in crucial ways that can impact your budget, maintenance routine, and even how the floor feels underfoot. In this post, we’ll dig deeper than surface shine to explore how these two flooring options compare, from installation and upkeep to which one holds up best in Florida’s famously humid climate.
Table of Contents
What Makes Polished Concrete Unique?
Understanding Clear Epoxy Coatings
Aesthetics: How Do They Look & Feel?
Installation Insights: Polished Concrete
Installation Insights: Clear Epoxy
Performance in Port St. Lucie’s Climate
Maintenance & Long-Term Care
Cost Factors & Return on Investment
Misconceptions & FAQs
Making the Choice: Key Considerations
Next Steps
1: What Makes Polished Concrete Unique?
Polished concrete has gained major traction in both residential and commercial spaces, and for good reason. Unlike coatings or overlays, polished concrete transforms the existing concrete slab into a sleek, durable surface through mechanical grinding and chemical treatments. This process doesn’t just add a shiny finish—it strengthens the concrete itself, making it more resistant to wear, stains, and moisture.
A Brief History of Polished Concrete
While polished concrete may seem like a modern design trend, it actually has deep industrial roots. For decades, warehouses and manufacturing plants have relied on this flooring method because it provides a seamless, high-durability surface without the need for coatings that can wear down over time. Today, the same principles are applied to retail stores, office buildings, and even high-end homes, proving that polished concrete isn’t just functional—it can be a design statement.
How Polished Concrete is Made
The process of achieving a polished concrete floor is all about grinding and refining the surface to the desired level of smoothness and shine. Here’s a quick breakdown:
Grinding – Heavy-duty machines equipped with diamond abrasives remove imperfections, stains, or old coatings from the slab.
Honing & Densifying – As the grinding process continues with finer grits, a densifier is applied to strengthen the concrete and reduce porosity.
Polishing – The floor is polished using increasingly fine abrasives until the desired gloss level is achieved—ranging from matte to ultra-glossy.
Sealing (Optional) – While polished concrete is naturally resistant to most stains, some homeowners and businesses opt for an extra sealer to enhance protection.
Where Polished Concrete Works Best
Because polished concrete relies on the existing concrete slab, it’s best suited for:
Retail & Commercial Spaces – Stores, offices, and hotels love it for its clean, modern look.
Warehouses & Industrial Facilities – Durability, low maintenance, and dust control make it ideal.
Modern Homes & Lofts – The minimalist aesthetic pairs well with contemporary interiors.
Polished concrete delivers a refined, high-performance surface without the need for additional coatings, making it a great long-term investment for high-traffic environments. But how does it compare to clear epoxy flooring? That’s what we’ll explore next.
2: Understanding Clear Epoxy Coatings
If polished concrete is all about enhancing the natural slab, clear epoxy coatings take a different approach—sealing and protecting the concrete with a durable, high-performance resin. Epoxy flooring is made from a two-part system: a resin and a hardener that, when combined, chemically bond to form a tough, non-porous surface. Unlike polished concrete, which is ground and refined, epoxy creates a protective layer on top of the concrete, offering additional resistance to chemicals, stains, and moisture.
What Makes Epoxy Flooring Different?
Epoxy flooring isn’t just a sealant or a thin coat of paint. It’s a multi-layer system designed to strengthen the concrete while also providing customizable finishes. Here’s what sets it apart:
Seamless, Glossy Finish – Epoxy creates a glass-like surface that enhances brightness and reflects light, ideal for showrooms, garages, and industrial spaces.
Chemical & Stain Resistance – Unlike polished concrete, epoxy won’t absorb oil, grease, or harsh chemicals, making it a top choice for automotive shops, kitchens, and warehouses.
Slip Resistance Additives – Epoxy can be modified with anti-slip agents to increase traction, making it safer in high-traffic or wet areas.
Customization – You can add color tints, decorative flakes, or metallic effects, which isn’t possible with traditional polished concrete.
How Clear Epoxy is Applied
The installation process for epoxy flooring is different from polished concrete and requires several key steps:
Surface Prep – The concrete must be mechanically ground to create a rough texture that helps the epoxy bond.
Primer Application – A bonding primer is applied to ensure a strong adhesion.
Epoxy Coating – The clear epoxy is poured and spread evenly, self-leveling as it cures.
Curing Time – Depending on temperature and humidity, epoxy takes 24-72 hours to fully cure before it can handle heavy traffic.
Where Clear Epoxy Works Best
Since epoxy creates a sealed protective layer, it’s commonly used in:
Garages & Auto Shops – It resists oil spills and tire marks better than polished concrete.
Medical & Laboratory Spaces – The non-porous surface prevents bacteria and chemicals from seeping in.
Showrooms & Retail Stores – The high-gloss finish enhances lighting and aesthetics.
Clear epoxy offers an extra layer of protection, especially in environments prone to spills, chemicals, or heavy impact. But when it comes to looks and feel, how does it stack up against polished concrete? Let’s dive into aesthetics next.
3: Aesthetics – How Do They Look & Feel?
At first glance, polished concrete and clear epoxy can look surprisingly similar, especially when both are finished to a high gloss. However, subtle differences in texture, color, and overall appearance set them apart. Whether you’re choosing flooring for a residential space, a showroom, or a commercial facility, the way these floors look and feel underfoot can make a big difference.
Polished Concrete: A Natural, Organic Look
Polished concrete enhances the natural characteristics of the concrete slab, which means no two floors look exactly alike. It’s a refined, high-end version of raw concrete, much like how marble is honed and polished to bring out its natural beauty. Here’s what you’ll notice:
Natural Variations – Since polished concrete reveals the stone and aggregate within the slab, every floor has a unique pattern.
Soft Sheen or High Gloss – The level of polish can be customized, from a low-luster satin finish to a mirror-like reflection.
Smooth but Not Glassy – While polished concrete looks sleek, it retains a slightly natural texture underfoot.
This organic, industrial-chic aesthetic is why polished concrete is popular in modern homes, lofts, and high-end commercial spaces.
Clear Epoxy: Glossy, Uniform Perfection
Epoxy coatings, on the other hand, create a perfectly smooth and uniform surface. Instead of enhancing the raw concrete, epoxy forms a protective layer that can be completely clear or tinted for added color depth. Here’s how it compares visually:
Consistent, Even Gloss – Unlike polished concrete, which has natural variations, epoxy provides a flawless, glass-like finish.
More Color Control – With clear epoxy, you can keep the look of raw concrete or opt for tinted versions to add warmth or depth.
Sealed, Almost Plastic-Like Surface – Epoxy has a slightly “soft” feel underfoot due to its resin-based composition.
Which Aesthetic Is Best for You?
If you love the natural, organic look and don’t mind some variation, polished concrete is the way to go.
If you prefer a perfectly smooth, high-gloss, sealed surface, clear epoxy flooring is the better fit.
Now that we’ve covered appearance, let’s move on to the installation process—because how these floors are created plays a big role in their final look and durability.
5: Installation Insights – Clear Epoxy
While polished concrete relies on grinding and refining the existing slab, clear epoxy flooring involves applying a protective resin coating that bonds to the concrete’s surface. This process creates a sealed, high-gloss, and highly durable finish that resists stains, chemicals, and abrasion. However, the success of an epoxy floor depends heavily on proper preparation and curing conditions.
Step-by-Step Process of Installing Clear Epoxy
Surface Preparation
The concrete must be clean, dry, and free of contaminants (dirt, grease, old coatings).
Mechanical grinding or shot blasting is used to roughen the surface, ensuring proper epoxy adhesion.
Primer Application
A bonding primer is applied to enhance adhesion and prevent bubbles from forming in the final coat.
The primer penetrates the concrete, sealing small pores and reducing the risk of moisture-related failures.
Epoxy Application
The clear epoxy resin and hardener are mixed and applied evenly across the floor.
This layer self-levels, creating a smooth and uniform surface.
Curing Process
Epoxy floors require 24–72 hours to fully cure, depending on temperature and humidity.
During this time, no foot or vehicle traffic is allowed to avoid imperfections.
Optional Topcoat for Extra Protection
A UV-resistant topcoat may be applied to prevent yellowing from sunlight exposure.
Anti-slip additives can be mixed in if extra traction is needed.
How Long Does It Take?
Small residential spaces (like a garage or basement) usually take 2–3 days from prep to full cure.
Larger commercial projects require several days to a week, depending on square footage and drying time.
Installation Challenges & Considerations
Epoxy Won’t Stick to Sealed Concrete – If the slab was previously sealed, it must be ground down first.
Moisture Problems Can Ruin Epoxy – If there’s moisture in the concrete, epoxy may peel or bubble over time.
Curing Conditions Matter – High humidity or cold temperatures can affect curing times and final durability.
When properly installed, clear epoxy creates a seamless, protective layer that outperforms polished concrete in terms of stain resistance. But what about how each floor performs in Port St. Lucie’s climate? Let’s explore that next.
6: Performance in Port St. Lucie’s Climate
Port St. Lucie’s warm, humid climate can be tough on many flooring materials, especially in areas exposed to moisture, heavy foot traffic, or outdoor elements. Both polished concrete and clear epoxy have strong durability, but how well they perform depends on temperature, humidity, and maintenance habits.
How Polished Concrete Handles Florida’s Climate
Polished concrete does well in Florida’s heat, but moisture can be a challenge:
-Heat Resistance – Because polished concrete is part of the existing slab, it doesn’t expand or soften under high temperatures. This makes it ideal for warehouses, garages, and commercial buildings that see a lot of sun exposure.
-Handles Humidity Well Indoors – When properly densified and sealed, polished concrete resists moisture buildup, making it a great option for indoor commercial spaces, kitchens, and showrooms.
-Susceptible to Moisture Issues – If not properly sealed, high humidity or flooding can darken and stain the surface. Coastal areas or places with poor drainage may need an additional moisture barrier.
-Condensation & Slipperiness – In extremely humid conditions, polished concrete can develop a thin layer of condensation, making it slippery—especially in high-traffic or air-conditioned spaces.
How Clear Epoxy Performs in Florida
Epoxy coatings provide a protective barrier against humidity, making them a strong choice for Port St. Lucie homes and businesses:
-Completely Sealed Surface – Unlike polished concrete, epoxy acts as a waterproof barrier, preventing moisture from seeping into the concrete. This makes it an excellent choice for garages, basements, and areas with potential flooding or spills.
-Chemical & Stain Resistance – Since epoxy doesn’t absorb moisture, it won’t discolor from salt air, chlorine, or household chemicals—making it perfect for coastal properties or poolside areas.
-UV Exposure Can Cause Yellowing – Clear epoxy coatings can turn yellow or chalky when exposed to direct sunlight. If using epoxy outdoors or near windows, a UV-resistant topcoat is essential.
-High Temperatures Affect Curing – In hot, humid weather, epoxy may take longer to cure or may not bond properly if conditions aren’t controlled. Working with an experienced installer ensures that the right curing methods and additives are used for Florida’s climate.
Which Flooring Option Works Best in Port St. Lucie?
If you’re installing inside a commercial space or home with controlled humidity, polished concrete is a sleek, low-maintenance option.
If you need maximum moisture protection, epoxy flooring is the safer bet, especially for garages, industrial spaces, and coastal properties.
Now that we’ve covered climate performance, let’s break down what it takes to maintain both flooring types over time.
7: Maintenance & Long-Term Care
No matter how durable a floor is, regular maintenance is key to keeping it looking and performing its best. Both polished concrete and clear epoxy are known for being low-maintenance compared to other flooring options, but they each have unique care requirements.
Caring for Polished Concrete
Polished concrete is easy to clean, but because it’s porous, it requires regular dust control and occasional deep cleaning to prevent surface wear.
Daily Maintenance
Sweep or dust mop to remove dirt, dust, and debris that could scratch the surface.
Use a microfiber mop and warm water for quick spot cleaning.
Weekly & Monthly Upkeep
Mop with a pH-neutral cleaner (avoid acidic or harsh chemicals like bleach or vinegar, which can dull the finish).
Use a concrete conditioner every few months to maintain the shine and protect against minor stains.
Long-Term Considerations
Avoid excessive water exposure—too much moisture can cause dark spots or weaken the concrete over time.
High-traffic areas may need periodic re-polishing to maintain their luster.
Oil or acidic spills (like citrus juice or wine) should be wiped up immediately to prevent staining.
Caring for Clear Epoxy
Since epoxy creates a non-porous barrier, it resists stains and doesn’t absorb spills, making it even easier to clean.
Daily Maintenance
Sweep or use a soft dust mop to keep grit from scratching the surface.
Wipe up spills immediately to prevent residue buildup.
Weekly & Monthly Upkeep
Mop with a gentle, ammonia-free cleaner (harsh chemicals can degrade the epoxy over time).
Avoid soap-based cleaners—they can leave a filmy residue that dulls the gloss.
Long-Term Considerations
Heavy objects or dropped tools can cause chips or gouges; use protective pads under furniture or machinery.
UV exposure can cause yellowing, so if your epoxy floor gets a lot of sunlight, consider a UV-resistant topcoat.
If the topcoat starts looking worn, a fresh recoat can restore the shine without having to replace the whole floor.
Which Option is Easier to Maintain?
Epoxy flooring requires less day-to-day maintenance since it’s sealed against moisture and stains.
Polished concrete is naturally long-lasting but may need occasional re-polishing to keep its high-gloss appearance.
Upkeep is just one factor when choosing the right flooring—cost and long-term value are just as important. Let’s dive into that next.
8: Cost Factors & Return on Investment
When choosing between polished concrete and clear epoxy, budget is often a deciding factor. While both options are cost-effective compared to other flooring materials, their price points vary based on installation complexity, customization, and long-term maintenance needs. Let’s break down what you can expect in terms of upfront costs and return on investment.
Upfront Installation Costs
Polished Concrete
Basic polishing (light grind with a matte finish): $3 – $5 per square foot
Mid-range polishing (higher gloss, densifiers, stain protection): $5 – $7 per square foot
High-end polished concrete (decorative finishes, extensive grinding): $7 – $12+ per square foot
Clear Epoxy Flooring
Single-coat epoxy sealer (basic clear finish): $4 – $6 per square foot
Multi-layer epoxy system (primer, epoxy, and topcoat): $6 – $10 per square foot
Decorative epoxy (metallic, flakes, UV-resistant topcoat): $10 – $15+ per square foot
Key Takeaways:
Polished concrete is often cheaper upfront if your existing concrete is in good condition.
Clear epoxy can be more expensive, especially for multi-layer applications that require grinding and surface prep.
Long-Term Cost & Maintenance
Polished Concrete ROI
Lifespan: 20+ years with occasional re-polishing.
Low maintenance costs (cleaning, periodic polishing every 5–10 years).
Good resale value for modern homes and commercial spaces.
Clear Epoxy ROI
Lifespan: 10–20 years, depending on traffic and exposure.
Higher maintenance potential (may need recoating every 5–7 years, especially in high-traffic areas).
Ideal for resale in industrial, garage, and high-end retail settings.
Which Flooring Offers the Best Value?
For large commercial spaces: Polished concrete is more cost-effective long-term because it doesn’t require recoating.
For garages, showrooms, or spaces exposed to spills: Epoxy justifies its higher price tag by offering superior stain resistance and a seamless protective layer.
Now that we’ve covered cost, let’s tackle some common misconceptions and FAQs about polished concrete and epoxy flooring.
9: Misconceptions & FAQs
There’s a lot of misinformation about polished concrete and clear epoxy, and we hear the same questions time and time again. If you’re deciding between the two, it’s important to separate fact from fiction—so let’s clear up some of the biggest myths.
Misconception #1: “Polished concrete is too slippery.”
False.
While polished concrete has a glossy look, it’s actually no more slippery than other hard surfaces like tile or hardwood.
If extra traction is needed, a non-slip treatment can be added to polished concrete to increase grip in high-traffic areas.
Misconception #2: “Epoxy flooring is only for garages.”
False.
Epoxy is commonly used in warehouses, medical facilities, restaurants, and high-end showrooms because of its stain resistance and seamless appearance.
Decorative epoxy finishes (like metallic or flake coatings) make it a popular choice for modern interior spaces as well.
Misconception #3: “Epoxy lasts forever.”
False.
While epoxy is highly durable, it can wear down over time—especially in high-traffic commercial spaces.
Unlike polished concrete, epoxy coatings may require reapplication every 5–7 years to maintain their shine and protective qualities.
Misconception #4: “Concrete can’t stain if it’s polished.”
False.
Unsealed polished concrete is still porous, meaning oils, acids, and chemicals can stain if spills aren’t cleaned up quickly.
A penetrating sealer can help protect against deep stains, but it’s not completely stain-proof like epoxy.
Frequently Asked Questions
Which is better for high-traffic areas?
Polished concrete is ideal for large spaces with constant foot traffic, while epoxy is better for areas exposed to chemicals, oil spills, or heavy equipment.
Can epoxy be applied over polished concrete?
Yes, but the concrete must be properly prepped first—a rough surface profile is needed for epoxy to bond correctly.
Which flooring type lasts longer?
Polished concrete: 20+ years with minimal upkeep.
Epoxy: 10–20 years, but may require recoating to maintain its appearance.
Now that we’ve addressed the common myths and concerns, let’s get to the final decision—which flooring is right for you?
10: Making the Choice – Key Considerations
Now that we’ve covered all the details—appearance, installation, durability, maintenance, and cost—you might still be wondering: Which flooring option is best for my space? The answer depends on your specific needs, environment, and long-term goals.
Choose Polished Concrete If…
Polished concrete is an excellent choice if you love the natural, industrial-chic look with its unique variations and subtle character. It’s especially well-suited for large commercial spaces, retail stores, offices, and modern homes where aesthetics and durability are equally important. Because polished concrete is incredibly long-lasting, it requires little maintenance beyond occasional re-polishing.
This option is also more budget-friendly upfront, making it ideal for large spaces where epoxy might be cost-prohibitive. However, it’s important to remember that polished concrete isn’t waterproof, and if left unsealed, it can absorb moisture or stains over time. If your space is prone to spills or heavy chemical exposure, a sealer may be needed for extra protection.
Choose Clear Epoxy If…
Epoxy flooring is the best choice if you need a seamless, waterproof, and stain-resistant surface. It’s especially beneficial in garages, workshops, commercial kitchens, warehouses, and industrial settings where durability and chemical resistance are essential. Unlike polished concrete, epoxy creates a protective barrier that completely seals the surface, preventing moisture, oil, and other substances from penetrating the floor.
Another major advantage of epoxy is customization. If you want a high-gloss, flawless finish, clear epoxy delivers that sleek, uniform look. Plus, it can be tinted, include decorative flakes, or even incorporate metallic effects for a unique, high-end appearance. However, epoxy may require occasional recoating to maintain its gloss, especially in areas with heavy foot or vehicle traffic.
Still Not Sure?
If you’re looking for a timeless, low-maintenance option with a natural look, polished concrete is a great fit. But if your space needs a high-performance, protective coating that resists stains and moisture, epoxy flooring is the smarter investment.
Still have questions? Let’s wrap things up with how to get expert advice for your space.
11: Next Steps
Choosing between polished concrete and clear epoxy comes down to more than just looks—it’s about how you use your space, your maintenance preferences, and your long-term investment. Both flooring options offer durability, style, and performance, but each excels in different environments.
If you love the natural, industrial-chic aesthetic and want a low-maintenance surface that lasts decades, polished concrete is an excellent choice. It’s perfect for modern homes, retail spaces, offices, and large commercial settings where durability and easy upkeep are priorities.
On the other hand, clear epoxy flooring offers superior stain resistance, a fully sealed surface, and a flawless high-gloss finish. If your space sees frequent spills, oil, or heavy machinery, epoxy provides the ultimate layer of protection. It’s a top pick for garages, warehouses, auto shops, and commercial facilities where functionality and resilience matter most.
Still Not Sure Which Floor is Right for You? Let’s Talk!
Every space is different, and choosing the right flooring isn’t always a one-size-fits-all decision. That’s why it helps to have a flooring expert who understands your specific needs and environment.
At Floor Kings, we’ve helped countless homeowners and business owners in Port St. Lucie find the perfect flooring solution. Whether you’re leaning toward polished concrete or clear epoxy—or just need advice on what works best for your space—we’re here to help.
Call Mike at (772) 370-7938 or email [email protected] to schedule a consultation. We’ll walk you through your options, discuss your budget, and help you make the best decision for your home or business.
The right floor makes all the difference—let’s make sure yours is built to last. Give us a call today!