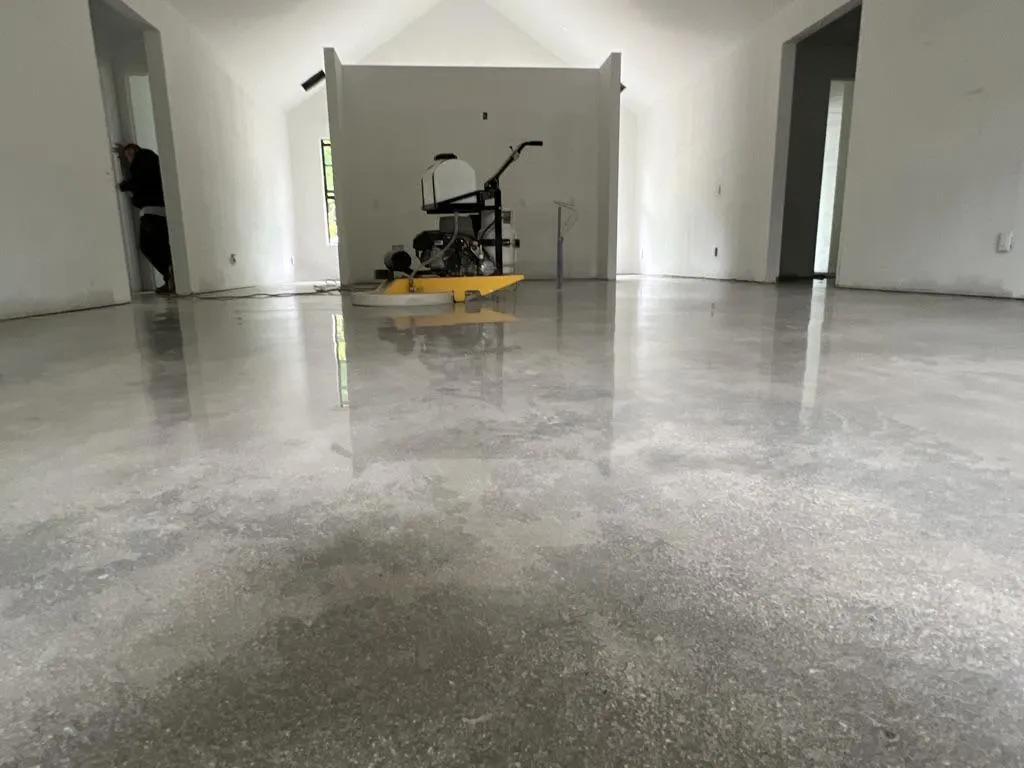
Polished Concrete in Port St. Lucie: The Ultimate Guide to Specialized Sealing and Maintenance
Port St. Lucie blends coastal elegance with a relaxed Floridian lifestyle, and polished concrete floors fit right into that breezy aesthetic. They reflect natural light, offer a cool underfoot feel, and resist much of the humidity that can afflict other flooring materials in this region. Yet even a polished concrete floor needs a layer of defense. That’s where specialized sealers step in, shielding against sand, salt-laden air, and the constant foot traffic of friends and family seeking sunshine.
As one local pro told me, “Polished concrete is like a hidden gem. You can uncover it and polish it to perfection, but you need a sealer to lock in its brilliance.” Let’s unravel why standard sealers often fall short, how to apply the right product for polished concrete, and what maintenance looks like in a coastal city like Port St. Lucie. Because if you want your floor to remain dazzling for years, an exceptional sealer is non-negotiable.
Why Standard Concrete Sealers Won’t Cut It
Typical sidewalk or driveway sealers aim to repel water and protect rough surfaces from freeze-thaw damage. They often rely on soaking into large pores. Polished concrete, however, has been ground to a finer finish, closing many of those pores. A generic sealer can end up sitting on top, failing to bond well, and eventually flaking or hazing. Specialized polished concrete sealers, by contrast, fuse with the densified surface, maintaining clarity and boosting shine.
This difference is huge in Port St. Lucie, where high humidity and coastal breezes can accelerate wear on poorly sealed floors. You want a sealer specifically formulated for polished concrete, something that can handle moisture and resist the salt in the air. Without that, your carefully polished slab might lose its luster in record time, leaving you with a blotchy or dull finish that demands a costly redo.
Moreover, standard sealers don’t necessarily address the unique chemical environment of polished concrete. Many polished concrete installations involve lithium or sodium silicate densifiers that chemically react with lime in the slab, creating a harder surface. A typical sealer might not adhere to this densified layer or could cause a cloudy appearance. Specialized formulations are tested for that synergy, ensuring the sealer not only sticks but also enhances the hardness and glossy reflectivity of your polished concrete. By investing in a high-grade, polished concrete–friendly product, you skip the pitfalls that plague those who opt for a one-size-fits-all approach.
The Art of Sealing a Polished Floor
Here at Floor Kings, we treat sealer application like the final artistic flourish. Polished concrete already has a captivating sheen, but the right sealer can take it from striking to downright unforgettable. We start by making sure the surface is immaculate—every grain of sand or trace of dust removed—because even a tiny speck can mar the final finish. Then, using a sprayer or microfiber pad, we lay down a thin, uniform layer of a specialized sealer.
Some sealers call for a second pass once the first has dried, or a burnishing step that uses friction to meld the sealer into the micro-surface of the polished concrete. When done carefully, this process intensifies the reflective property, giving that “mirror-like” allure so many clients crave. Rush it, and you’ll see visible streaks or patchy sections that ruin the floor’s uniform glow.
Timing also plays a big part. Port St. Lucie’s warmth can speed up cure times, so we keep a close eye on how quickly the sealer is setting. If it dries too fast, you can end up with overlap marks or uneven absorption. Humidity levels also matter; on especially muggy days, certain sealers might take longer to set, leaving the polished concrete vulnerable to dust or footprints. We adjust our application plan based on real-time conditions, ensuring each coat dries properly and bonds seamlessly. That adaptability is why professional sealing often achieves more reliable results than quick DIY attempts, especially in a coastal environment.
The Resealing Question
A freshly sealed polished concrete floor can look like something out of a design magazine. Yet the question remains: how often must you reseal to keep it that way? For a modestly trafficked home, you might get away with two or three years before needing a refresher. In a bustling commercial space—perhaps a restaurant near the water—yearly or even biannual touch-ups could be the norm.
Resealing doesn’t mean starting from scratch. Often, it’s as simple as lightly cleaning and scuffing the surface before adding a fresh coat of the same sealer. Some floors also benefit from periodic burnishing sessions that restore shine without needing a full re-coat. Either way, it’s about proactive care. You don’t wait until the floor is covered in scratches or showing water infiltration. A little maintenance now prevents bigger headaches later, ensuring your polished concrete retains its coastal glam indefinitely.
In between reapplications, daily cleaning routines make a tremendous difference. A gentle dust mop or soft-bristle broom can remove the sand grains that inevitably follow us home from Port St. Lucie’s beaches. When these abrasive particles grind into the surface, they can diminish the sealer’s protective layer on your polished concrete. Quick spot-cleaning of spills or drips also helps avert permanent stains. Though a sealed polished concrete floor provides a significant window of forgiveness, it’s not an excuse to let puddles of juice or coffee linger. The sooner you address minor mishaps, the longer your floor stays pristine.
Stained and Dyed Floors Under Seal
When owners in Port St. Lucie really want to go bold, they often introduce color into their polished concrete. Whether it’s an aqua tint that mirrors the ocean or an earthy stain reminiscent of driftwood, these hues can radically transform the ambiance. A sealer specifically built for colored polished concrete ensures that the pigment doesn’t fade under strong Florida sunlight or wash out from repeated cleaning.
Acid stains require special attention, since leftover chemical residues might interfere with sealer adhesion or cause blotchiness. Dyes tend to be more straightforward, but each color approach has its quirks. A small test patch can reveal if the sealer will deepen the color significantly or alter the tone. If you’re layering multiple colors or stenciling patterns, each step might require a light sealing or setting agent to lock it in before adding the next shade. This methodical layering keeps your artistic vision crisp on the polished concrete surface.
One technique we’ve used with success is applying a transparent “color guard” sealer between different dyes. This method segregates each hue, preventing any bleeding or overlap. Once the design is finalized, a final topcoat sealer wraps the entire polished concrete floor in a glossy shield. It’s a bit more work, but for those who want intricate color motifs—like a faux-tile effect or nature-inspired patterns—it’s a game-changer. Without these specialized sealing steps, the lines between colors might blur or fade more quickly under Port St. Lucie’s sun. Think of your floor as a layered painting, each coat preserving the masterpiece beneath.
Exterior Spaces: Polishing in the Florida Sun
Polished concrete isn’t just an indoor trend. Some Port St. Lucie homeowners polish their patios or pool decks to create a sleek, resort-like atmosphere. Outdoor polishing poses unique challenges: UV exposure, puddling, salt from ocean breezes, and frequent heavy rains can all degrade inferior sealers. That’s why picking a UV-stable, weather-tested sealer is a must for exterior polished concrete.
You also want to consider slip resistance. A polished deck near the pool can become slippery when wet, so a sealer that allows for a finely textured additive may be essential. This additive is usually broadcast onto the wet surface, then locked in with a final clear coat. The result? You get the sophisticated gloss of polished concrete without turning the deck into a slipping hazard. Striking that balance between high shine and safe footing is crucial in any outdoor project.
We’ve seen clients opt for penetrating sealers beneath a film-forming top layer outside. That dual approach addresses moisture intrusion at a deeper level—especially relevant near pool areas—while the outer coat boosts gloss and wards off surface-level scuffs. It’s a system well-suited to Florida’s humidity and occasional storms. Just remember that polished concrete in direct sun can heat up quickly, so if you’re aiming for comfort underfoot, consider lighter-toned dyes or reflective sealers that minimize heat absorption. That attention to color and reflectivity can keep your polished surfaces inviting, even on sweltering summer afternoons.
Mistakes to Avoid
One glaring error is assuming any leftover sealer will do. If it’s not formulated for polished concrete, you may get peeling within weeks or a hazy film that obliterates the floor’s sparkle. Another misstep is piling on the sealer too thick in hopes of “extra protection.” Often, that leads to milky streaks or drips that never fully cure. Proper technique means multiple thin coats, each allowed to dry or burnish as instructed by the manufacturer.
Foot traffic too soon is yet another culprit. Even if the top layer feels dry, the deeper portions of the sealer may remain tacky, risking footprints or permanent impressions. A little patience goes a long way. In commercial settings, scheduling can be tricky, but skipping adequate cure time undermines everything you just paid for. If you ever see hazing, delamination, or streaks, there’s a good chance at least one of these pitfalls occurred.
Also worth noting is the risk of “ghosting” patterns if the polished concrete slab had tile or carpet before. Sometimes, if the sealer reacts with residual adhesives or contaminants, you’ll see faint outlines of the old layout. Thorough prep is essential—grinding away old glue, cleaning thoroughly, and ensuring the slab is free of chemical residues. If you’re repurposing a space in Port St. Lucie where previous flooring left behind adhesives, double-check that your selected sealer and application method can handle that scenario. Overlooking these details can spell disaster for the final sheen of your polished concrete transformation.
Behind the Chemistry
When it comes to polished concrete sealers, you’ll encounter terms like, acrylic, polyurethane, polyurea, and more. Acrylic is simpler and user-friendly but may wear faster in high-traffic zones. Polyurethane stands strong against chemicals and physical abrasion, though it takes skillful handling to avoid roller marks or bubbles.
In Port St. Lucie, with near-constant sunshine and humidity, UV stabilization and moisture tolerance are key. If you anticipate daily exposure to salty air (closer to the coastline) or if your polished concrete floor will see a lot of foot traffic, double-check the sealer’s specs. It’s not just about initial gloss; you want that shine to endure. A high-quality product can keep your floors looking freshly polished for years, while a subpar formula might degrade after just one season.
You might also see sealer hybrids that incorporate densifiers, effectively blending the final polishing step with sealing. These can be convenient but might not offer the same level of UV or chemical resistance as a dedicated topcoat. Always read the fine print. Some polished concrete projects benefit from using separate products—one to densify, one to seal, and one to add slip resistance. It all depends on where your floor is located, how it will be used, and how frequently you plan to maintain it. By matching the chemistry to your real-world needs, you avoid the dreaded cycle of strip-and-reseal that plagues many who rush the decision.
Protecting Your Investment
A polished concrete floor can be a beautiful asset, but it won’t stay that way without the right sealer and timely upkeep. Constant sanding from beach sand, the humidity that creeps in through open doors, or the occasional spilled frozen drink can all conspire to dull your floor’s sparkle. Sealing wards off these threats and ensures you aren’t forced to re-polish prematurely—a process that can be costly and disruptive.
When you weigh the cost of sealing against the potential savings in maintenance and restoration, the choice is clear. Once you’ve committed to polished concrete in Port St. Lucie, going the extra mile with a specialized sealer is a no-brainer. It’s the difference between a floor that’s occasionally impressive and one that consistently wows visitors with a deep, glossy finish.
The other hidden benefit is resale value. Potential buyers often appreciate the upscale look of polished concrete but may hesitate if they suspect it hasn’t been cared for properly. Demonstrating that you’ve used the correct sealer and kept it in good shape adds credibility and desirability. Whether you’re planning to stay put for decades or might list your property someday, that polished sheen can be a selling point. A well-sealed, well-maintained floor signals to buyers that the entire home or business is equally well-tended.
What Next?
Ready to get started on a fresh seal for your polished concrete? Or maybe you’re still weighing the pros and cons of polishing your slab in the first place. At Floor Kings, we’re here to guide you. We understand Port St. Lucie’s unique environment—salt air, sand, humidity—and we tailor our product recommendations to match real-world conditions. Fill out our contact form today or connect directly with Mike at 772-370-7938 or [email protected].
We’ll walk you through every step, from assessing your current floor condition to selecting a top-tier sealer that merges beauty with serious protection. Don’t let your polished concrete lose its luster to the elements. Let’s safeguard that striking shine so you can enjoy a floor that radiates Florida flair for years to come.