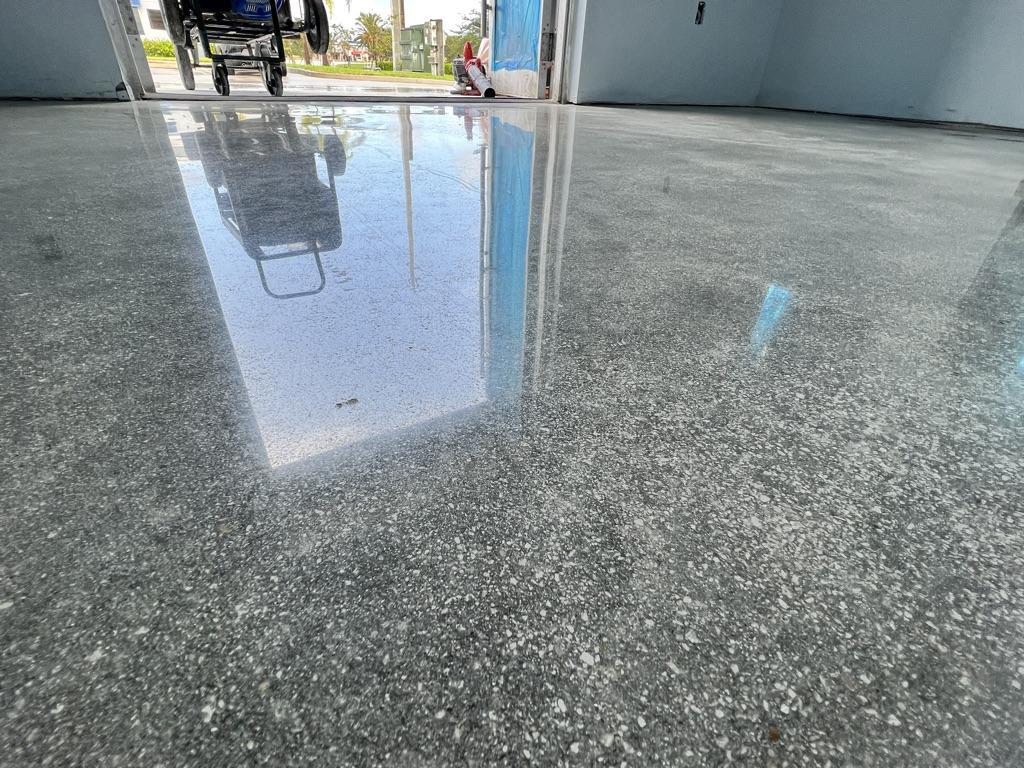
Polished Concrete in Port St. Lucie: What It Is, What It Isn’t, and Why So Many Contractors Get It Wrong
Polished Concrete: More Than Just Shiny Cement
If you think polished concrete is just regular concrete with a glossy sealer on top, you’ve been lied to—and you're not alone. We’ve lost count of how many times someone in Port St. Lucie calls us up thinking they got a polished floor, only to find out what they really got was a sealer job that’s already peeling, scratching, or turning cloudy after six months.
Here’s the truth: real polished concrete isn’t a coating at all. It’s a process. A technical, multi-step system that turns your actual concrete slab into a finished floor—no top layer, no shortcuts, no gimmicks. When it’s done right, the concrete becomes the finish. We’re talking diamond grinding, chemical densification, and multiple passes of progressively finer polishing to achieve that smooth, durable, low-maintenance surface everyone loves.
And no, you can’t fake it with a buffing pad and a bottle of gloss. You can’t just pour a glossy acrylic sealer over a dirty garage and call it “polished.” That might fool the eye for a few weeks, but the first time you drive over it, mop it, or leave something wet on it overnight—you’ll know the difference.
Durable enough to handle forklifts and daily foot traffic without wearing out.
Easy to clean, because the densified surface resists dusting, staining, and spills.
Customizable, with options for aggregate exposure, sheen level, even decorative cuts or stains.
It’s not for every space, and it’s not a cheap shortcut. But when you want a concrete floor that lasts, looks clean, and doesn’t need to be re-done every couple of years, polishing is the top dog.
Now let’s talk about all the myths (and straight-up lies) that float around about polished concrete—and how to spot them.
The Most Common Myths (and Contractor Lies) About Polished Concrete
Let’s be honest—half the reason polished concrete gets a bad rap is because too many contractors are out here selling “fake polished” floors. And if you’re not in the coatings industry, you might not even realize you’ve been sold snake oil until it’s too late.
Let’s clear the air.
“We can polish over your painted floor!”
Nope. Not a chance. If the concrete has paint, glue, mastic, or any coating on it, it has to come off completely before polishing can even begin. Why? Because polishing works the actual concrete—not what’s on top of it. Anyone who tells you they can just polish right over a painted slab is either clueless or lying.
“We’ll put down a glossy sealer—same thing!”
Absolutely not. That’s not polishing—that’s coating. It might look shiny at first, but it’ll wear out fast, especially in garages, warehouses, or high-traffic areas. Sealers peel. Polished concrete doesn’t. There’s a reason big box stores, breweries, and airports use real polished concrete: it performs, and it lasts.
“Polished concrete is slippery.”
Wrong again. Polished concrete can be slick if it’s polished to a high gloss and left bone-dry, but when installed correctly—with the right grit level for the use case—it can meet or exceed ADA slip resistance requirements. Most garages and shops benefit from a satin or matte finish, which offers plenty of grip even when dusty or wet.
“You don’t need a densifier if your slab is hard.”
False. Densifiers are critical, even for hard concrete. They chemically react with the slab to fill in pores and increase abrasion resistance. Without it, the polish won’t hold, the floor will dust, and surface wear will show up fast—especially in Florida where the concrete tends to be softer than other parts of the country.
Bottom line? If the contractor you’re talking to can’t explain these differences—or worse, tries to convince you they’re not important—you’re about to write a check for something that’s going to disappoint you.
And now, let’s dig into what really separates a beautiful, long-lasting polished floor from a patchy, hazy disaster.
What Makes or Breaks a Polished Concrete Job
Here’s the part most people don’t realize until they’re already halfway into a mess: the quality of a polished concrete floor has almost nothing to do with the polish—and everything to do with the prep. The tools, the process, the slab, the technician—it all has to line up. Otherwise, you're left with a dull, streaky surface that never looks right and wears out fast.
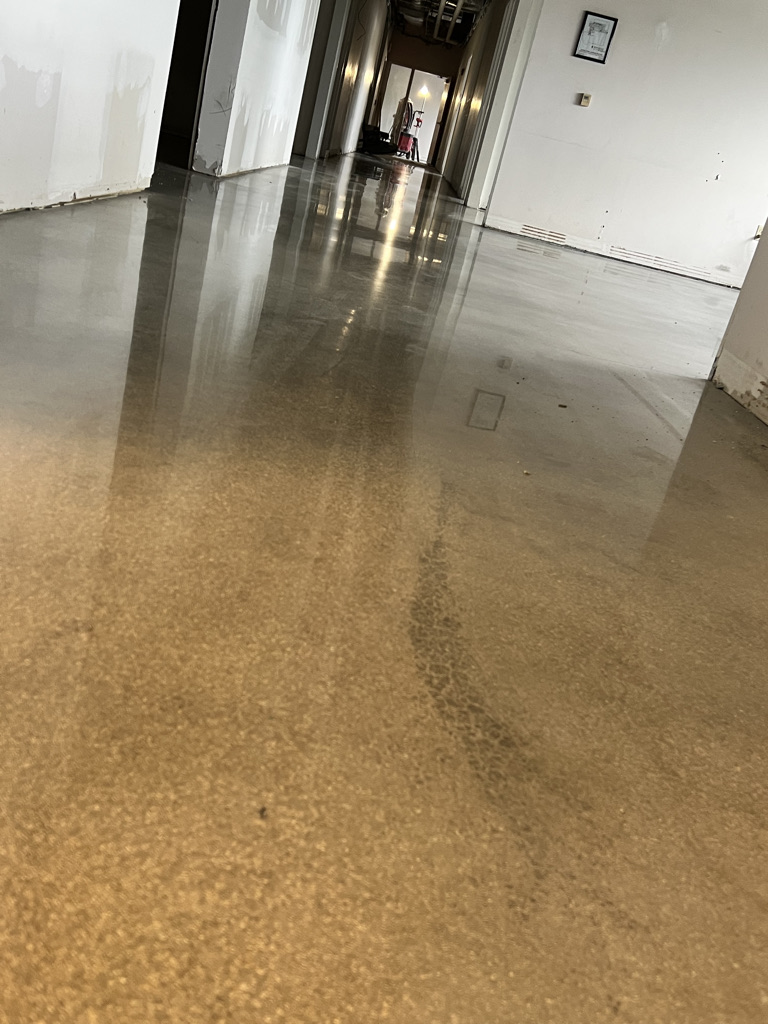
Want beautiful polished concrete like this for your business in Port St. Lucie? Give us a call!
Let’s start with the slab.
Not all concrete is created equal. The strength of the mix, how it was poured, how long it cured, whether it was power troweled too tight—all of that affects how it will polish. In Port St. Lucie, we often run into slabs with high moisture content or uneven finish work, and if you don’t know how to read the concrete before grinding, you’re setting yourself up for failure.
The grind sequence is everything.
Polishing isn’t one pass with a shiny pad. It’s a step-by-step system that can include six to twelve different grits—starting with aggressive metal-bond diamonds to flatten and expose the surface, and moving into resin-bond grits to refine and smooth. If a contractor skips grits, you’ll see swirls, ghosting, and an inconsistent finish. There’s no shortcut here. You either do it right, or you don’t do it at all.
Densifier isn’t optional.
A good polished concrete job always includes densification. This liquid treatment chemically hardens the slab by filling in the microscopic voids. Without it, you don’t get the wear resistance or long-term durability. Worse, the floor will start to dust, especially in hot, humid areas like Florida where unsealed slabs break down faster.
Gloss level needs to match the use case.
You want a showroom shine? We can take you to 1500 grit. But if it’s a busy garage, a restaurant kitchen, or a retail shop with high foot traffic, we may recommend a lower grit finish—like 400 or 800—for better traction and easier maintenance. We don’t just chase shine. We build floors that work for the space.
You’d be shocked how many polished concrete floors in Port St. Lucie fall apart not because of the materials—but because someone skipped a step to save time. And by the time the client realizes it, they’re stuck.
Want to know what failure looks like? Let’s get into that next.
Why Some Floors Fail—and How We Fix Them
Not all polished concrete jobs end well. In fact, we get called all the time to fix floors that should have been done right the first time—but weren’t. And you know what we see more often than not? The same mistakes, over and over, by contractors who either didn’t know what they were doing or simply didn’t care.
Sealer masquerading as polish.
This one’s the most common. A contractor sells the customer on “polished concrete,” then rolls on a high-gloss acrylic sealer. It looks shiny for a couple weeks—maybe even a couple months. But the first time someone drags a tool chest across it or hits it with hot tire traffic, the coating scuffs, peels, or flakes. That’s not polished concrete. That’s a scam with a short fuse.
Skipped grinding steps.
Some crews try to rush through the job with minimal passes—using cheap equipment or skipping metal-bond grits altogether. The result? A floor that looks blotchy, has visible swirl marks, or feels inconsistent underfoot. And once those missed steps are buried under densifier and polish, you can’t fix it without starting over.
No densifier, no joint work, no long-term durability.
We’ve seen “polished” floors in commercial spaces that weren’t densified at all. Within months, the surface started dusting, edges began chipping, and every joint turned into a crack. Without proper densification and joint treatment, polished concrete just doesn’t hold up.
Moisture problems ignored.
Florida concrete sweats—especially older slabs with no vapor barrier. If a contractor doesn’t test for moisture, you could end up with efflorescence (that white powdery residue), or worse, a floor that won’t take polish evenly. We’ve had to grind back entire installs because someone rushed it and ignored the science.
When these floors fail, customers are left disappointed, frustrated, and out thousands. And that’s usually when they call us.
At Floor Kings, we don’t show up with excuses—we show up with grinders, densifier, and a plan to do it right.
Want to know what makes our approach different? Let’s go there.
How Floor Kings Gets It Right Every Time
We’re not here to sell the cheapest job. We’re here to deliver a floor that works—for years. At Floor Kings, polished concrete isn’t a buzzword. It’s a craft. And we treat every job like we’re polishing our own shop floor.
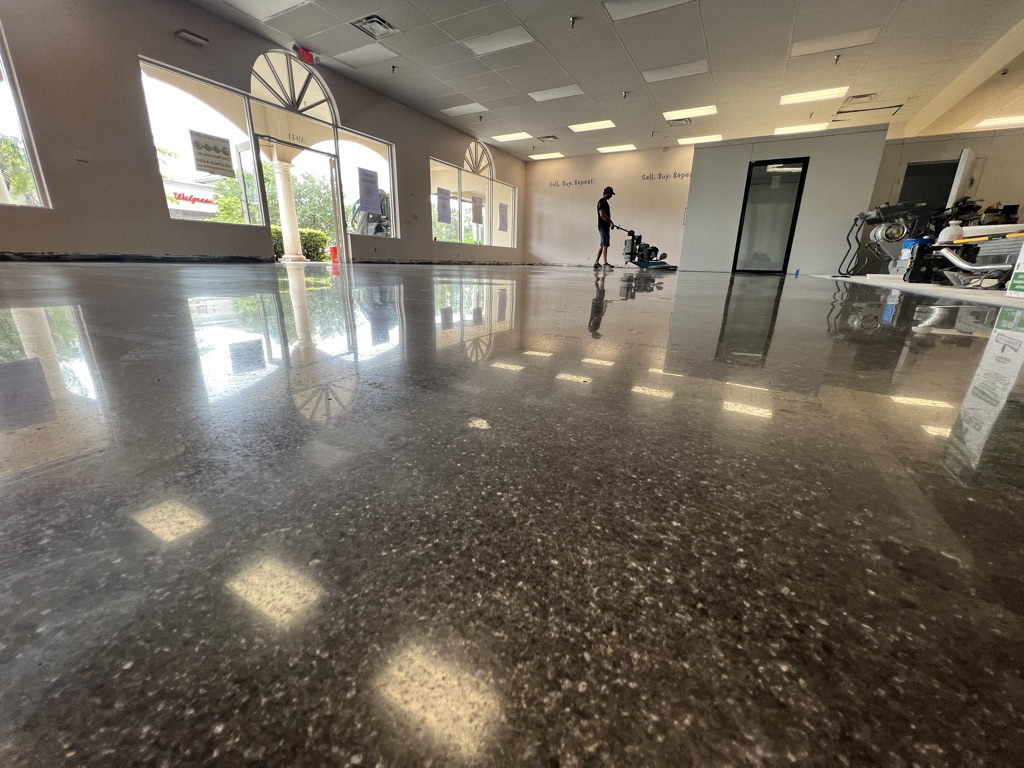
Real polished concrete with a real shine (no sealers) that will last for years in Port St. Lucie FL
It starts with the walk-through.
Before we even quote a project, we come out and look at the slab. We check for cracks, coatings, trowel patterns, joint conditions, and moisture. Because no two slabs are the same—and if a contractor is quoting you without seeing the floor, they’re guessing. We don’t guess.
We grind like we mean it.
Our crew doesn’t roll in with a buffer and call it good. We bring heavy-duty planetary grinders, industrial vac systems, and the right diamond tooling for your concrete’s hardness. Whether we’re exposing aggregate or just refining the cream surface, we follow the full grit sequence. Every. Single. Time.
We densify properly.
We don’t spray and pray. We apply densifier at the right stage in the process, let it absorb, and burnish it in as needed. That densifier becomes part of the slab—it’s what gives polished concrete its hardness, stain resistance, and longevity.
We tailor the finish to your needs.
Want high-gloss? We’ll take it to 1500 grit and make it shine. Need a more functional satin finish for traction or easier maintenance? We’ll stop at 400 or 800. Every space has different demands, and we match the polish to the purpose.
We never cut corners—and we never outsource.
Our team is in-house, trained, and experienced. No subs. No mystery crews. Just skilled tradespeople who show up on time, respect your property, and do the job right the first time.
That’s why homeowners, business owners, and facility managers across Port St. Lucie trust Floor Kings when they want polished concrete done properly.
Want Concrete That Actually Performs? Let’s Talk.
You don’t need a floor that just looks good on day one—you need a floor that still looks good after five years of foot traffic, Florida humidity, and real-world use. That’s what real polished concrete delivers when it’s done right.
At Floor Kings, we don’t sell surface shine—we build durable, low-maintenance floors that work. Whether you’re renovating your garage, upgrading your retail space, or planning a new commercial build-out, we’ll help you figure out if polished concrete is the right move—and if it is, we’ll make sure it’s done to spec, no shortcuts.
Want to see what your concrete can really become?
Call Mike at Floor Kings at 772-370-7938, email [email protected] or fill out our contact form. We’ll schedule a time to walk the job, explain your options, and give you a quote that’s based on facts—not fluff.
If you’re tired of the gimmicks and just want it done right, we’ve got you.