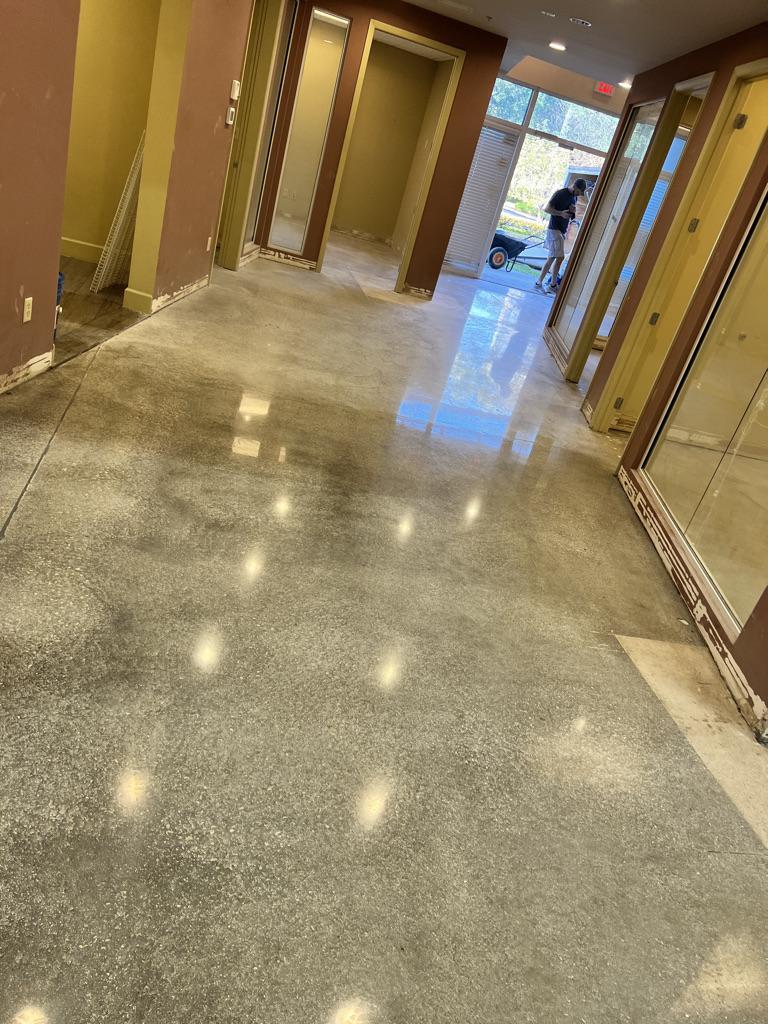
Polished Concrete’s Thermal Edge in Port St. Lucie: A Technical Perspective
Port St. Lucie, known for its subtropical warmth and scenic coastal environs, is a city where comfort and style often blend seamlessly in commercial architecture. Yet, keeping large interior spaces pleasant without soaring utility bills remains a challenge for many businesses. This is where polished concrete floors, combined with the strategic use of thermal mass, can truly stand out as a solution. By harnessing concrete’s heat-storing capability and refining it into a visually appealing, high-performance surface, commercial property owners and architects can enjoy benefits that span stable indoor temperatures and reduced maintenance costs.
In the following pages, we delve deeper into the technicalities that make polished concrete such a valuable flooring option in Port St. Lucie. From examining the physics of thermal mass to applying design strategies unique to Florida’s climate, and from exploring synergy with local humidity to comparing other flooring alternatives, this discussion arms you with the knowledge to make informed choices about polished concrete. The result can be a floor that not only manages temperature swings but endures daily use in a warm, coastal region.
Table of Contents
Thermal Mass Fundamentals and Florida’s Climate
The Core Attributes of Polished Concrete Floors
Port St. Lucie: Climate Opportunities and Flooring Challenges
Heat Transfer Mechanics in Commercial Buildings
Slab Thickness, Insulation, and Densification for Polished Concrete
Reflectivity, Aesthetics, and Surface Chemistry
Installation Nuances: Prepping for a Polished Concrete Finish
Comparing Polished Concrete to Other Solutions
Energy Modeling and Practical Outcomes
Common Questions about Polished Concrete in Coastal Areas
Conclusion: Where Architecture and Practicality Unite
Floor Kings: Bridging Science and Art in Flooring
1. Thermal Mass Fundamentals and Florida’s Climate
Thermal mass, the capacity of a material to absorb and release heat energy, is essential in an environment like Port St. Lucie, which experiences consistent warmth and moisture. Materials with substantial thermal mass can moderate internal conditions by drawing in heat when the air is hot and letting it out when the air cools. Polished concrete floors excel in this capacity, especially because they expose the mass of the concrete rather than insulating it beneath carpets or vinyl.
In a Florida region where air conditioning often runs for extended hours, any measure that helps buffer temperature can save money. By gently absorbing daytime warmth, a polished concrete floor may slightly reduce peak cooling loads. Then, during cooler evenings, it can release some stored heat if the building design allows. While night flushing strategies might be less pronounced in humid conditions, the principle stands that a massive, polished concrete slab moderates extremes in an otherwise warm climate.
2. The Core Attributes of Polished Concrete Floors
Polished concrete is formed by mechanically grinding, honing, and refining a concrete slab until it achieves a chosen level of sheen. The process typically uses diamond abrasives of increasing fineness, with densifiers enhancing surface hardness. Rather than adding a surface layer like epoxy, polished concrete focuses on transforming the slab itself into a dense, reflective, and highly durable finish. This approach allows the slab’s inherent mass to remain fully engaged with the building environment.
Crucially, polished concrete floors offer a near-continuous surface, free of grout lines or seams. From an engineering standpoint, this uniformity supports both mechanical strength and thermal uniformity. Any surface pores or microcracks are minimized during densification, so the floor can withstand forklift traffic, chemical spills, or daily foot traffic without significant wear. In Florida’s humid environment, that sealed, densified top layer helps avoid moisture ingress that could undermine the slab’s stability or performance.
3. Port St. Lucie: Climate Opportunities and Flooring Challenges
In Port St. Lucie, commercial buildings often deal with extended heat and occasional bursts of heavy rain. Polished concrete floors, when executed properly, have the resilience to handle these conditions. They resist moisture better than untreated surfaces, and they maintain their strength despite frequent temperature changes.
While Florida’s nights may not always be dramatically cooler, a polished concrete slab can still contribute to flattening temperature spikes. Even a few degrees of difference between daytime and nighttime can allow the floor to release some accumulated heat, benefiting occupant comfort and potentially shaving off a portion of electricity costs. The key is to design the building’s envelope and ventilation approach to let the floor interact with the outside conditions in a manageable fashion. If the interior is tightly climate-controlled, the polished concrete floor’s mass can reduce how rapidly the space warms up when doors open, or how stable it remains if the AC cycles off after hours.
4. Heat Transfer Mechanics in Commercial Buildings
Polished concrete floors engage in conduction (heat movement within the slab), radiation (infrared exchange between the surface and its surroundings), and some convection (air movement across the surface). The net effect is that heat can be absorbed or released more gradually than in flooring materials with low thermal mass. In commercial applications, such as retail aisles or office hallways, occupant comfort often hinges on stable temperatures. With an effective thermal mass floor, the interior experiences fewer rapid changes when the sun blazes outside or when occupant density fluctuates.
Concrete’s conduction rate is moderate, which is beneficial. If conduction were too high, heat might dissipate too quickly to the ground or out of the building, diminishing any buffering advantage. If conduction were too low, the floor wouldn’t effectively spread the absorbed heat. Polished concrete strikes a sweet spot: it holds large volumes of heat while still transferring it gradually to the environment.
5. Slab Thickness, Insulation, and Densification for Polished Concrete
Slab thickness plays a direct role in how much thermal mass a floor can provide. For big commercial structures, slabs might be 6 to 8 inches or more, enabling more significant heat storage. In some designs, a vapor barrier or insulating layer is placed below the concrete to reduce downward heat loss or moisture migration from the soil. This approach intensifies the interaction between indoor air and the polished concrete slab, maximizing thermal mass effects.
Densification is an integral step in producing polished concrete. By chemically bonding silicates to the top portion of the slab, the floor’s surface gains additional hardness. This densification does not significantly alter conduction in the slab’s deeper layers. Instead, it fortifies the upper zone, ensuring the mass beneath remains in solid contact with occupant spaces while retaining the mechanical strength to handle commercial demands. In a coastal, humid climate, densification also blocks micro-voids, limiting moisture infiltration from above.
6. Reflectivity, Aesthetics, and Surface Chemistry
One hallmark of polished concrete is its potential for a reflective sheen. Polishing reduces surface roughness, enabling light to bounce off the floor. That reflectivity can help commercial interiors reduce overhead lighting requirements, especially in spaces with large window banks. The synergy of bright Florida sun and a luminous polished concrete floor can enhance interior brightness, giving an upscale, modern ambiance.
From a chemistry standpoint, a polished and densified surface also tends to have slightly altered emissivity and absorption characteristics. If the finish is exceptionally glossy and lightly colored, it might reflect more radiant energy, allowing the deeper slab to hold less solar heat. Conversely, a darker dyed or stained polished concrete surface can absorb more infrared radiation, storing it in the mass. Architects and property managers in Port St. Lucie can fine-tune the choice of color, dye, or final polish level to strike a balance between the building’s aesthetic goals and the desire to harness solar gains or avoid excessive heat.
7. Installation Nuances: Prepping for a Polished Concrete Finish
Crafting a polished concrete floor in a commercial setting starts with evaluating the slab’s condition. Surface contaminants, old coatings, or adhesives must be removed thoroughly. Cracks, chips, or spalling areas need repairs that can be blended smoothly once grinding commences. The grinding process advances from coarse to fine diamonds, revealing a progressively smoother surface.
Densifiers are typically applied when the slab is partially refined, so they can penetrate adequately. After the densifier cures, polishing continues with finer diamonds to achieve the target gloss. In Port St. Lucie, where humidity is a factor, it’s crucial that the slab’s moisture vapor emission rate is manageable, preventing any bond failures or efflorescence that would mar the polished concrete finish. Once completed, the floor is a seamless expanse that unites mechanical resilience, reflective beauty, and the beneficial mass that underlies heat moderation.
8. Comparing Polished Concrete to Other Solutions
Many commercial owners ponder whether polished concrete is preferable to epoxy, vinyl, tile, or carpeting. Epoxy can create robust films but may insulate the slab slightly, reducing direct conduction from the air to the concrete mass. Vinyl or carpet further insulate, lowering the slab’s capacity to capture or release heat. Tile can conduct heat but typically lacks the continuous thickness or monolithic nature that polished concrete offers.
From a cost and performance standpoint, polished concrete requires no secondary adhesives, minimal upkeep, and can last for decades. The synergy of aesthetics, durability, and mass-based temperature buffering distinguishes it from other flooring systems that address only one or two of these needs.
9. Energy Modeling and Practical Outcomes
Though Florida nights might not always provide large temperature drops, the consistent sunlight throughout the year can be leveraged by polished concrete floors. Designers sometimes run simulations using software such as IES VE or EnergyPlus to quantify how the floor responds to extended daylight exposure and moderate nighttime cooling. The results typically show modest but meaningful reductions in peak cooling loads and occupant temperature fluctuations, especially in large commercial rooms like showrooms, event spaces, or lobbies.
Real-world data collection often mirrors these modeling results when the building is designed thoughtfully, with window orientations, shading devices, and HVAC cycles that integrate the thermal mass of polished concrete. Over the lifetime of the property, owners may realize savings in energy costs and appreciate the lower maintenance demands of a floor that requires little more than regular cleaning and occasional buffing to retain its polished look.
10. Common Questions about Polished Concrete in Coastal Areas
A frequent concern is moisture, and whether polished concrete floors can withstand high humidity or the salt-laden breezes near the Florida coast. Properly densified floors resist moderate chemical intrusion and do not readily absorb moisture, provided any major infiltration or vapor drive issues are addressed at the slab design stage. Another question revolves around slip resistance. High-gloss polished concrete can appear slick, but finishing techniques, micro-etching, or slip-resistant conditioners can help maintain traction.
Some commercial facilities worry about heavy loads, such as forklifts or rolling shelving units. If the slab is structurally sound, polished concrete is robust enough to handle these loads without gouging or peeling. Repairs or partial re-polishing might be needed after many years of extreme usage, but this is still less disruptive compared to periodic replacements required by less durable flooring materials.
11. Conclusion: Where Architecture and Practicality Unite
Polished concrete floors present a valuable way to tap into concrete’s thermal mass in Port St. Lucie’s subtropical climate. By refining and densifying the slab, property owners gain a surface that remains visually compelling and functionally resilient while still participating in daily temperature moderation. Although the region’s humidity and warm nights may limit the scope of passive strategies, any advantage in reducing extreme indoor temperatures or helping HVAC systems operate more efficiently is beneficial for commercial owners.
The combination of long-lasting durability, relatively low maintenance, and a design aesthetic that can be made to suit myriad styles positions polished concrete as a powerhouse flooring option. Whether it’s about making a spacious hotel lobby more comfortable, elevating the look of a retail showroom, or providing a cost-saving angle for a multi-use commercial building, polished concrete consistently meets the demands of modern architecture and building science.
12. Floor Kings: Bridging Science and Art in Flooring
At Floor Kings, we passionately unite creative design with proven engineering principles in polished concrete floors. For commercial property owners and architects in Port St. Lucie, this means we can deliver a floor that is both a statement piece and a strategic element in managing thermal mass. Our approach spans the entire process: from evaluating the slab and preparing it for polishing to applying densifiers that reinforce surface hardness without diminishing the core mass that characterizes concrete’s thermal capacity.
We view each floor as an opportunity to merge the technical rigor of mechanical and chemical finishing with the natural strengths of polished concrete. Our local expertise ensures we address Port St. Lucie’s challenges of humidity and heat, leaving clients with floors that shine in both appearance and energy-minded functionality. It’s where artistry meets practical performance—every time we polish a slab into a refined surface.
If you’re considering polished concrete as a strategic flooring choice for your commercial property in Port St. Lucie, contact Floor Kings today. Email [email protected] or call 772-370-7938. Let us discuss how a polished concrete floor can store and release heat in alignment with your building’s goals, all while delivering a beautiful, long-lasting surface that complements the Florida coastal lifestyle.