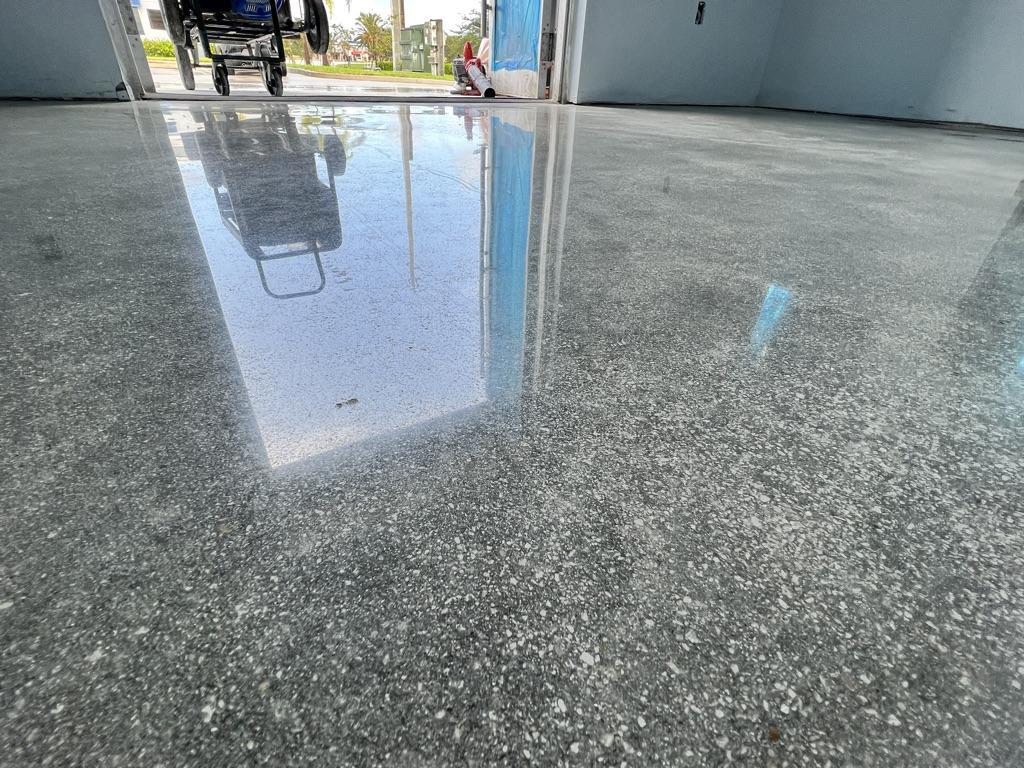
Polished vs. Epoxy Floors: Which One’s Right for Your Space in Port St. Lucie?
The Great Flooring Decision
Whether you're building out a new garage, renovating a commercial space, or just tired of dealing with stained concrete, one thing’s clear: you’ve got options. Two of the most popular? Polished concrete and epoxy flooring. Both look sharp. Both hold up well. And both are available right here in Port St. Lucie.
But they’re not interchangeable.
At Floor Kings, we hear this question all the time: “Should I go with polished concrete or epoxy?” The answer isn’t about which one is better — it’s about which one is better for your specific space and how you plan to use it.
The best choice depends on a handful of factors: durability needs, maintenance expectations, the condition of your slab, your budget, and the look you’re after. In this post, we’ll break it all down to help you make the right call — no fluff, no sales pitch, just straight talk from people who install these floors every day.
What Is Polished Concrete?
Polished concrete is exactly what it sounds like — your existing concrete slab, refined through a multi-step grinding and polishing process until it shines. There’s no coating on top, no paint, no overlay. What you’re seeing is your actual concrete, densified and polished to a smooth, reflective finish.
The process starts with heavy-duty grinders that remove surface imperfections and level out the slab. Then we apply a densifier, which hardens the concrete surface and helps prevent dusting and wear. After that, we move through progressively finer diamond grits until we hit the desired gloss level — matte, satin, or full mirror shine. It's customizable, but it's still raw concrete at its core.
In Florida, where moisture and humidity are constant battles, polished concrete has a big advantage — there’s no coating to peel or flake. Once it’s polished and sealed properly, it holds up incredibly well, especially indoors.
This flooring is common in warehouses, retail spaces, restaurants, and even high-end residential settings like modern living rooms or minimalist garages. It’s sleek, clean-looking, and has that industrial vibe a lot of homeowners are after these days.
What Is Epoxy Flooring?
Epoxy flooring is a resin-based coating system that’s applied over concrete to create a durable, seamless, and chemical-resistant surface. Unlike polished concrete, which works with the raw slab itself, epoxy is a protective layer that sits on top of it — and that layer can be customized for performance, style, and safety.
A standard epoxy installation involves prepping the concrete (usually by grinding), then applying a two-part epoxy resin that cures into a hard, plastic-like surface. Depending on the system, we may add colored flake chips, metallic pigments, non-slip textures, or multiple topcoats for extra protection.
What makes epoxy so popular in garages, shops, and commercial settings? Durability. A well-installed epoxy system can resist oil, salt, chemicals, hot tires, heavy equipment — even forklifts. It also creates a sealed surface, so there’s no dusting or absorbing spills like bare concrete.
Epoxy flooring shines in garages, warehouses, medical offices, restaurants, and auto shops — anywhere you need a clean, low-maintenance surface that won’t stain or degrade over time. And here in Port St. Lucie, it handles the Florida climate like a champ when installed properly with the right materials and prep.
Appearance: Sleek vs. Seamless
Both polished concrete and epoxy flooring look sharp — but they give off very different vibes. If style and aesthetic are high on your priority list, this is where the decision starts to take shape.
Polished concrete has a natural, industrial look. It reflects light beautifully, especially at higher gloss levels, and highlights the texture, character, and imperfections of the existing slab. If you're going for that modern, minimalist style — think loft apartment, showroom, or high-end retail — polished concrete brings that clean, architectural feel without looking like a coating.
Epoxy flooring, on the other hand, is all about customization. You can go with solid colors, flake systems that mimic granite or terrazzo, high-gloss metallics, or even custom logos for businesses. It creates a completely uniform, sealed finish with zero variation from the underlying concrete. That makes it great for garages, kitchens, and commercial spaces where a clean, consistent surface matters.
So, if you love the look of raw concrete and want to embrace it, polished might be your lane. If you want something with color, texture, or a bit of flash — epoxy gives you more freedom to express that style.
Durability & Performance
When it comes to long-term performance, both polished concrete and epoxy flooring are known for being tough — but they handle wear and tear in very different ways.
Polished concrete is durable because it is the concrete. There's no surface coating to chip or peel. Once it's densified and polished, it becomes highly abrasion-resistant and can withstand heavy foot traffic, shopping carts, forklifts — you name it. That’s why you see it everywhere from big box stores to airport terminals.
But there’s a catch: it’s still porous. If you spill oil, wine, or chemicals and don’t clean it quickly, it can stain. There are penetrating sealers we can apply to help with that, but the surface isn’t completely sealed the way epoxy is.
Epoxy flooring, on the other hand, creates a true barrier on top of the concrete. It’s 100% non-porous, meaning it won’t absorb spills, oils, or chemicals — just wipe it clean. And depending on the system, you can add slip resistance, UV stability, chemical resistance, and even thermal shock resistance for places like commercial kitchens.
When installed correctly, epoxy can take a serious beating — dropped tools, hot tires, heavy equipment — without cracking or flaking. It’s the go-to for spaces where protection and cleanability are non-negotiable.
So if you're planning to abuse your floors — think garages, workshops, kitchens, or auto shops — epoxy is usually the better fit. For lower-impact spaces with a focus on aesthetics, polished concrete holds its own.
Maintenance & Upkeep
No one wants a high-maintenance floor — and luckily, both polished concrete and epoxy are solid choices if you’re looking to keep things simple. But again, they take different paths to get there.
Polished concrete is about as low-maintenance as it gets — no wax, no stripping, no coatings to reapply. Just regular dust mopping and the occasional wet mop with a pH-neutral cleaner. That’s it. Over time, it may lose some of its shine in high-traffic areas, but it can be re-buffed or lightly polished without a full redo. If you treat it right, it’ll last decades with very little effort.
Epoxy flooring is also easy to clean — spills, oil, dirt, and even salt from the beach rinse right off. But depending on how the surface is used, you might need to recoat the top layer every 5–10 years, especially in heavy-use commercial settings. And while epoxy is durable, it can scratch or scuff under heavy impact if no topcoat or slip-resistant additive is used.
In Florida’s climate, humidity and sand can be brutal on all types of flooring. The good news? Both polished concrete and epoxy hold up far better than tile, carpet, or wood. But in terms of long-term simplicity, polished concrete wins for passive durability, while epoxy wins for barrier protection.
Cost Considerations
Let’s be honest — budget plays a big role in any flooring decision. But if you’re looking for a straight answer like, “Polished concrete is cheaper than epoxy” (or vice versa), it’s not that simple.
Polished concrete can be more affordable if your existing slab is in good shape. Since it uses the concrete you already have, there are no added coating materials. But if the floor is uneven, stained, or soft from poor finishing, the polishing process gets more involved — and costs go up. You’re paying for labor and time, not product.
Epoxy flooring, on the other hand, involves more materials — resins, flakes, primers, and topcoats — and more application steps. That said, it often requires less surface perfection before install. In some cases, it can actually be more cost-effective if your slab isn’t polish-ready.
Customization also affects pricing. A simple gray epoxy system will cost less than a high-gloss metallic flake floor with a polyaspartic topcoat. Likewise, a basic grind-and-seal concrete finish won’t cost the same as a multi-step full polish to 3,000 grit.
Bottom line? The best value comes from choosing the right system for the job — not the cheapest upfront price. A bad floor is expensive no matter how “affordable” it was.
Which One’s Right for You?
If you’re choosing between polished concrete and epoxy flooring, the right answer comes down to what your space demands — and how you want it to look and perform over time.
Want something sleek, modern, and almost maintenance-free for a clean indoor space?
Go polished. It’s low-fuss, durable, and timeless — perfect for showrooms, retail, and upscale garages.
Need something that can take abuse, resist chemicals, and clean up fast?
Go epoxy. It gives you more design flexibility and creates a sealed, protective barrier that stands up to the toughest environments.
And if you’re not sure? That’s where we come in.
At Floor Kings, we’ve installed both systems across Port St. Lucie — from minimalist homes to heavy-use shops. We’ll look at your slab, your goals, and your budget, and tell you straight what’ll work best for your space.
Talk to Floor Kings for an Expert Recommendation
Still weighing your options? Give Mike at Floor Kings a call at 772-370-7938 or email [email protected]. He’ll walk you through the pros and cons based on your space — no pressure, no guesswork. Just honest answers from people who know concrete like the back of their hand.