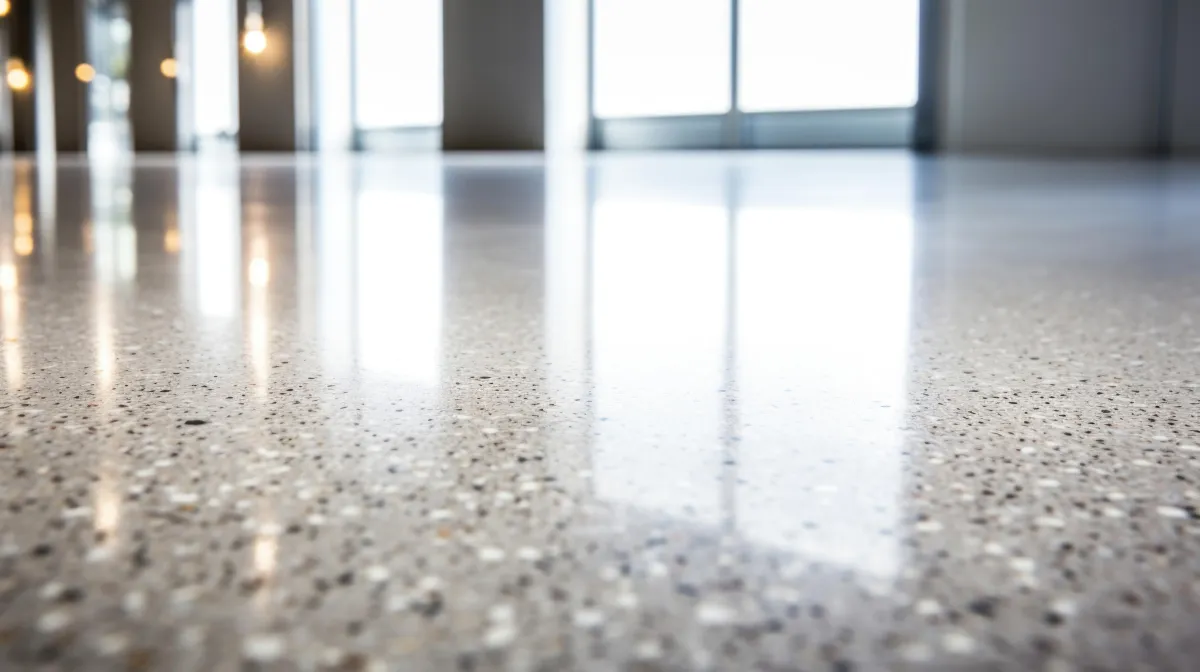
Six Mistakes That Hinder Polished Concrete in Port St. Lucie, FL—Advice from the King of Floors
“According to a study in Concrete Construction Magazine, well-executed polished concrete can reduce lifecycle costs by up to 20% compared to traditional flooring options, thanks to lower maintenance and longer service life.”
That’s an impressive figure, and it’s one of the reasons polished concrete is gaining traction in Port St. Lucie, FL. With the city’s warm climate and diverse architectural styles—ranging from contemporary coastal to traditional Floridian—property owners want durable, easy-care flooring solutions that still look great.
However, achieving a gleaming polished concrete finish isn’t guaranteed. At Floor Kings, we’ve seen projects go sideways because of improper moisture management, skipping crucial grit steps, or ignoring ongoing maintenance. These mistakes can dull your shine, cause uneven coloration, or lead to future troubles like efflorescence—especially if the slab lacks a proper vapor barrier. Below, I’ll explore six of the most common pitfalls and offer workable strategies to steer clear of them.
(If you’d rather entrust your floor to pros or need targeted advice, reach out to Mike at Floor Kings: 772-370-7938 or [email protected] we're here to help Port St. Lucie floors look their best!)
1) Underestimating Moisture Vapor Problems
Florida’s humidity can be relentless. And while polished concrete can thrive here, a slab that continuously draws moisture from below will pose challenges. Without a proper vapor barrier—or if that barrier has degraded—moisture vapor travels upward. This is more than an aesthetic concern; excessive moisture hampers densifier absorption and weakens the stain guard’s efficacy.
Efflorescence is another potential side effect. If you spot a white, powdery substance on the surface, that’s likely mineral salts carried up by moisture. It’s not just unsightly—it’s a sign you need to address the underlying moisture source. Failing to do so can lead to repeat occurrences, which get tougher to remove with each buildup.
Practical Tip
Vapor Emission Tests: Conduct a calcium chloride test or use RH probes to measure moisture levels in the slab. If levels are high, consider a professional moisture mitigation strategy.
Assess Drainage: Ensure that exterior drainage around your Port St. Lucie property is adequate. Standing water near the foundation can exacerbate vapor migration.
2) Minimal Surface Prep
No matter how fancy your grinder, if you haven’t removed old paint overspray, adhesives, or superficial damage, the final finish will suffer. Polishing will magnify, not hide, imperfections. We’ve encountered jobs where the owners were shocked to see old tile outlines faintly visible in the newly polished floor.
Starting with a coarse grit is almost always the way to go—30 or 40 grit to strip away unwanted residues. Progress systematically through finer grits only after you’re certain the surface is free from contaminants. You can’t rely on medium or high grits to do the heavy lifting of removing deep scratches, leftover glue, or surface irregularities.
Practical Tip
Mechanical Removal: Use a dedicated set of metal-bond diamond tools for the initial pass. Chemical strippers might not fully eliminate certain residues, and they can complicate densifier application later.
Spot Repairs: If you find damage like spalling or small cracks, repair them before moving into finer-grit polishing.
3) Skipping Crucial Grit Levels
Polishing concrete is a step-by-step refinement process. Skipping grits is like applying a top coat of paint without priming or sanding: it might look okay from afar, but close inspection reveals glaring flaws. Some contractors or DIYers jump grit levels to save time, only to discover swirl marks or persistent scratch patterns near the end.
In Port St. Lucie, where many commercial properties use large open spaces, it’s tempting to try and rush. But if you race through the grit ladder, you’ll spend more time (and money) correcting those blemishes later. Worse, you may never fully get them out, forcing you to settle for a subpar floor or restart entirely.
Practical Tip
Document the Process: Keep a clear record of your grit progression. This is especially important for larger projects or if multiple team members are polishing in shifts.
Examine in Sections: After each grit, pause to look for uniform scratch removal across a test area. Any leftover marks mean you need another pass.
4) Inconsistent Densifier or Stain Guard Application
Using a densifier is critical for developing a harder, more durable surface that’s less prone to wear. Stain guard adds an extra layer of protection against spills, foot traffic, and everyday dirt. But these products only work if they’re applied correctly. Too much moisture in or on the slab can dilute or block their reaction.
Applying densifier too late—once you’re already at a very fine grit—limits penetration, as the pores are nearly closed. Conversely, applying it too early can lock in surface debris or residues, causing bonding issues. The sweet spot often lies between 100 and 200 grit. Follow manufacturer guidelines and watch for changes in the floor’s sheen or slip resistance to gauge when the reaction is complete.
Practical Tip
Uniform Spread: Use a pump-up sprayer to distribute densifier or stain guard evenly, then use a microfiber pad to ensure consistent coverage.
Time It Right: If the product specifies a 15-minute dwell time, don’t cut corners. Let it fully react. Squeegee or auto-scrub any unabsorbed residue to prevent streaks.
5) Neglecting Detail Work Around Edges and Corners
When people think of polished concrete, they often picture large machines gliding across an open slab. The reality is that finishing edges, corners, or areas around columns is painstaking. Some skip or half-heartedly address these sections, creating a noticeable difference in shine. That abrupt transition can cheapen the entire appearance of the floor.
In Port St. Lucie’s upscale retail environments, for example, any mismatch becomes glaring under spotlights or sunlight through storefront windows. If your client or boss is particular about aesthetics, expect them to notice. Ultimately, edge work can’t be an afterthought.
Practical Tip
Dedicated Edge Grinders: Invest in small, specialized hand tools. Your main grinder can’t reach tight corners effectively.
Layered Grit Approach: Mirror your main polishing sequence in these small areas. If the main floor stops at 800 grit, do the same for the edges.
6) No Maintenance Plan
Even the best-polished floor dulls over time if treated negligently. Dust, dirt, and sand (especially in coastal Florida) can abrade the surface, dulling its shine. A simple dust-mop every day—plus a weekly or bi-weekly damp mop—goes a long way. Think of polished concrete like a high-end car finish: it might be durable, but it’s not indestructible.
For commercial sites, a more rigorous schedule—possibly including a monthly high-speed burnish—can keep that mirror-like reflection. If you’ve applied a stain guard, follow the manufacturer’s refresh or reapplication guidelines. Spot repairs on cracks or minor damage should also be tackled quickly to maintain a seamless appearance.
Practical Tip
Train Staff: If you’re working in a commercial environment, train the cleaning crew on which products to use (neutral pH cleaners) and which to avoid.
Burnish Periodically: High-speed burnishing helps rejuvenate the floor’s gloss, especially in high-traffic corridors or public-facing areas.
Key Takeaways
Watch for Moisture: Florida’s humidity can push moisture vapor up through the slab. Without proper barriers, densifiers and stain guards may fail.
Prep Methodically: Remove all unwanted residues and debris before polishing.
Don’t Skip Grits: Each stage refines and erases previous scratches; shortcuts spell trouble.
Apply Densifier & Stain Guard Correctly: Timing, uniform coverage, and moisture control are key.
Detailing Matters: Edges and corners deserve the same attention as main floor areas.
Maintenance is Ongoing: A solid cleaning and upkeep routine keeps polished concrete floors in top shape for years.
FAQs (10 Questions)
Is polished concrete suitable for outdoor patios in Port St. Lucie?
It can be, but be aware that high humidity and rain can accelerate wear. Plus, moisture vapor from the ground can cause issues if no vapor barrier exists.Does polished concrete get slippery?
It’s comparable to other hard surfaces when dry. Water or spills can create slippery conditions, so proper cleaning and optional slip-resistant conditioners are advisable.How do I remove efflorescence from an existing floor?
Efflorescence removal typically involves specialized cleaners and brushing. But the long-term fix is addressing the moisture source.How long does the densifier need to cure?
Many densifiers require a specific dwell time, followed by polishing steps. Cure times can vary—read the label carefully and allow for at least the recommended period.Will polishing fix uneven spots in the slab?
Minor unevenness can be mitigated by initial grinding, but major dips or structural flaws require more extensive repair first.Why is my polished concrete turning cloudy in certain areas?
Uneven densifier application, leftover residue, or high moisture content can cause cloudy patches. Additional buffing or a light re-grind might be needed.How long does a complete polishing job take?
It varies by floor size, condition, and desired gloss level. A standard commercial floor might take several days to a week.Is it okay to use bleach for cleaning?
Avoid harsh chemicals like bleach or vinegar. They can degrade stain guard or densifiers and etch the surface. Neutral pH cleaners are best.Do I need to re-polish after a few years?
Many commercial spaces opt for periodic burnishing or light polishing refreshes. The frequency depends on traffic volume and the effectiveness of routine maintenance.Can I apply a stain or dye before polishing?
Yes, many people color their concrete before the final polish to achieve decorative effects. Just ensure you follow the dye manufacturer’s guidelines for drying and subsequent polishing.
Contact Floor Kings
Location: Port St. Lucie, FL
Phone: 772-370-7938 (Ask for Mike)
Email: [email protected]
Looking for polished concrete services in Port St. Lucie? Floor Kings can guide you through every step—from initial moisture testing to the final gloss—so you can avoid these six pitfalls and enjoy a flawless floor.