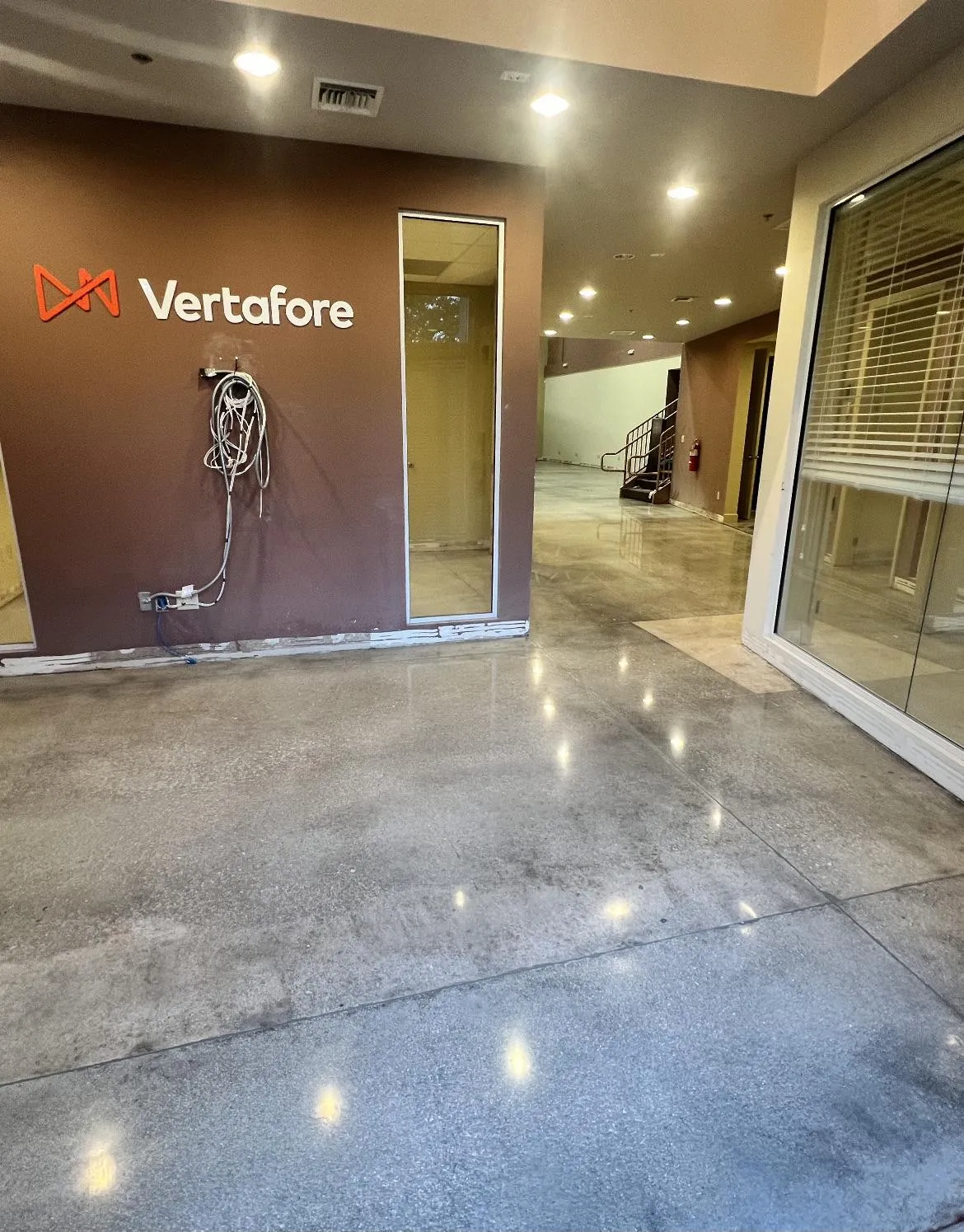
The Architect’s Playbook: How to Specify Polished Concrete Floors for Successful Commercial Projects
Polished concrete floors are quickly becoming the flooring of choice among architects and designers in commercial projects across Port St. Lucie, FL, thanks to their unmatched durability, timeless aesthetic appeal, and sustainability benefits. However, transforming concrete into the beautifully polished, high-performance flooring clients expect isn't simply a matter of pouring concrete and polishing it. The difference between an impressive result and an expensive mistake comes down to how clearly and thoughtfully the polished concrete specifications are crafted.
At Floor Kings, we've seen firsthand how detailed and accurate specifications not only streamline the construction process but significantly improve client satisfaction. With years of experience delivering exceptional polished concrete floors throughout Port St. Lucie, we're sharing this guide to help architects and designers specify polished concrete with confidence—avoiding common pitfalls and delivering floors that consistently surpass expectations.
Table of Contents
Polished Concrete Fundamentals: What Architects Need to Know
Concrete Mix Design: Getting It Right from the Start
Specifying Aggregate Exposure and Gloss Levels Clearly
Addressing Moisture Control and Vapor Barriers in Specifications
Handling Cracks, Joints, and Imperfections in Your Specifications
Specifying Slip Resistance & Ensuring ADA Compliance
Including a Maintenance Plan in Your Specifications
Choosing the Right Polished Concrete Partner
Making Your Polished Concrete Project a Success with Floor Kings
1. Polished Concrete Fundamentals: What Architects Need to Know
Before you dive deep into the technical details, it’s crucial to have a clear, fundamental understanding of polished concrete and why it's become a top choice for commercial architecture projects. Polished concrete is not simply concrete coated with a glossy sealer. Rather, it's a specialized flooring system created by mechanically grinding, honing, and polishing concrete slabs using progressively finer diamond abrasives. The result is a smooth, dense, and highly reflective floor surface that delivers remarkable durability and visual appeal.
Commercial architects in Port St. Lucie increasingly choose polished concrete because it aligns perfectly with modern design trends. It’s aesthetically versatile—easily adaptable to contemporary, industrial, or upscale interiors—and highly practical, offering durability, resistance to heavy foot traffic, ease of maintenance, and even improved indoor air quality compared to carpet or vinyl alternatives.
But here's the catch: specifying polished concrete correctly involves much more than selecting a gloss level or color. The choices you make in your specifications—such as concrete mix, aggregate exposure, moisture control, and safety requirements—have significant, lasting impacts on the final outcome. Clear, detailed specifications help prevent costly errors and misunderstandings, ensuring the finished floors truly reflect your vision and perform beautifully for years to come.
Now, let's examine the critical first step: specifying the ideal concrete mix design for polished concrete success.
2. Concrete Mix Design: Getting It Right from the Start
One of the most crucial—and frequently overlooked—aspects of specifying polished concrete is the concrete mix design itself. While architects often focus heavily on aesthetics, the success of any polished concrete floor begins with the slab beneath it. Without careful attention to mix design, even the most visually stunning floors can suffer from durability issues, inconsistent finishes, or unexpected repairs shortly after installation.
When specifying polished concrete, architects need to pay close attention to three essential mix-design elements:
Water-to-Cement Ratio:
Specify a low water-to-cement ratio (around 0.40 to 0.45). A lower ratio yields a denser, harder concrete surface that polishes more consistently and resists cracking and surface defects. High water content might simplify initial installation, but it reduces durability and results in a porous slab prone to discoloration or uneven gloss when polished.Concrete Strength (PSI):
Commercial polished concrete floors should ideally have a minimum compressive strength of 3,500 to 4,000 PSI. Floors specified below this threshold are more likely to experience surface degradation, premature wear, and difficulty achieving uniform gloss levels. At Floor Kings, we've seen Port St. Lucie projects require expensive re-polishing and repairs because initial PSI specifications weren't adequate for high-traffic commercial spaces.Consistent Aggregate:
Specify a consistent aggregate type, size, and distribution within the concrete mix. Uniform aggregate distribution ensures predictable results in aggregate exposure and visual consistency. Poor aggregate specification often leads to an uneven surface appearance that disappoints clients expecting precise, polished aesthetics.
Consider a recent retail project we worked on here in Port St. Lucie: The initial specification didn't clarify the water-to-cement ratio or aggregate distribution. Once polished, the floor revealed noticeable patches and uneven aggregate exposure, forcing costly grinding and refinishing. Clear specifications could have prevented this scenario completely.
Taking the extra time to specify these details upfront ensures your polished concrete floors not only look incredible but also meet the functional requirements your clients demand. With concrete mix specifications clearly defined, architects can confidently move forward to selecting the ideal aggregate exposure and gloss level for their commercial projects.
3. Specifying Aggregate Exposure and Gloss Levels Clearly
When it comes to polished concrete floors, specifying aggregate exposure and gloss levels might initially seem straightforward—but it’s precisely where architects and designers often run into confusion. Without crystal-clear specifications, contractors and clients can end up with dramatically different expectations, potentially leading to costly and time-consuming misunderstandings.
Let’s first tackle aggregate exposure. Polished concrete floors typically come in four distinct aggregate exposure levels:
Cream Finish (Minimal Exposure):
This finish is achieved by minimal grinding, resulting in a smooth, uniform appearance without visible aggregates. Ideal for modern commercial spaces seeking a subtle, seamless aesthetic.Salt-and-Pepper Finish (Light Exposure):
A slightly deeper grind reveals fine aggregates evenly distributed throughout the slab. It offers subtle texture and visual interest, suitable for retail shops, offices, or restaurants aiming for contemporary elegance.Medium Aggregate Exposure:
A deeper grind exposes medium-sized aggregates, adding greater visual depth and character. It’s commonly specified for commercial spaces that want their polished concrete floors to make a stronger design statement.Full Aggregate Exposure:
Extensive grinding showcases large aggregates, creating a striking, decorative appearance. Often chosen for high-end hospitality venues, boutiques, or luxury showrooms where the floor itself becomes a key design feature.
Beyond aggregate exposure, architects must clearly specify gloss levels. Polished concrete finishes can range from matte and satin to high-gloss:
Matte or Satin:
Offers improved slip resistance and hides minor surface imperfections well, making it practical for high-traffic commercial spaces.High-Gloss:
Reflects light dramatically, enhancing spaces visually. However, high-gloss requires careful consideration regarding slip resistance and maintenance.
To illustrate, Floor Kings recently collaborated on a Port St. Lucie restaurant project that initially specified only “polished concrete floors.” The architect envisioned full aggregate exposure and a satin finish, but without clear documentation, the contractor delivered a basic cream finish. Clarifying these specifications upfront would have prevented additional grinding, polishing, and unexpected project delays.
Always specify aggregate exposure and gloss levels clearly and explicitly in your documentation. Providing visual references or sample mockups ensures everyone—clients, contractors, and your own design team—is aligned from the outset, guaranteeing your polished concrete floors reflect your exact vision.
Next, we'll discuss the essential—but often neglected—area of moisture control and how Florida’s climate makes this a particularly critical consideration for architects.
4. Addressing Moisture Control and Vapor Barriers in Specifications
Architects designing polished concrete floors in Port St. Lucie and throughout Florida must prioritize moisture control as a critical aspect of their project specifications. Given Florida’s subtropical climate—with its high humidity, frequent rainfall, and significant seasonal fluctuations—moisture management isn't just an optional step; it's an essential factor that dramatically impacts polished concrete performance.
Moisture issues typically present themselves as efflorescence (white powdery deposits), surface cloudiness, sealer breakdown, or even more serious delamination. These problems aren’t just cosmetic—they can quickly erode client confidence and lead to expensive, disruptive remediation work.
For instance, Floor Kings recently assisted a commercial client in Port St. Lucie who had previously installed polished concrete floors without specifying moisture barriers or testing protocols. Within months, moisture rising through the slab caused extensive discoloration and surface damage. This unexpected setback required substantial grinding, moisture mitigation, and refinishing—ultimately delaying the opening of the business and significantly exceeding initial budget expectations.
To avoid these types of scenarios, architects should explicitly include moisture testing and vapor barriers in their polished concrete specifications:
Moisture Testing Protocols:
Clearly specify that ASTM-standard moisture tests, such as ASTM F2170 (relative humidity test) or ASTM F1869 (calcium chloride test), must be performed prior to polishing. Results from these tests guide necessary precautions or additional treatments.Vapor Barriers:
Include a high-quality polyethylene vapor barrier (at least 10-15 mil thickness) underneath the slab within your specifications. This barrier significantly reduces the risk of moisture migration, protecting the polished concrete from below.Moisture Mitigation Systems:
If tests indicate high moisture levels, specify mitigation systems such as epoxy moisture barriers or penetrating sealers as part of the pre-polishing preparation phase.
Clearly addressing moisture control upfront in your specifications ensures your polished concrete floors not only look exceptional upon completion but remain beautiful and durable long-term—even in Florida’s challenging climate.
Next, let's explore how clearly addressing cracks, joints, and surface imperfections can elevate your polished concrete designs and prevent costly surprises.
5. Handling Cracks, Joints, and Imperfections in Your Specifications
Many architects and designers mistakenly assume polished concrete floors will naturally conceal cracks or imperfections—but the reality is often just the opposite. Polishing concrete highlights the natural beauty of the material, which also means any cracks, joints, or imperfections will become more noticeable if not properly planned for. This is especially important in commercial settings, where appearance and longevity are equally critical.
Concrete inevitably develops cracks over time. Rather than ignoring or hiding this reality, architects should proactively address it within their specifications. Proper handling of joints and imperfections not only enhances the aesthetic quality of polished concrete floors but also significantly improves their functional lifespan.
For example, Floor Kings recently partnered with a commercial client in Port St. Lucie who initially didn’t specify how to handle joints and cracks. Upon polishing, unexpected surface imperfections became visible, resulting in last-minute design adjustments, additional labor, and significant delays. Clear specification from the outset could have avoided these unnecessary complications.
To ensure a visually pleasing and structurally sound polished concrete surface, consider the following best practices:
Specify Control Joints Strategically:
Clearly indicate in your specifications the locations of control joints to guide potential cracking intentionally, transforming it from a liability into a controlled design feature.Use Joint Fillers and Epoxy:
Specify high-quality epoxy or polyurea joint fillers that stabilize and aesthetically blend cracks or joints with the overall floor surface. Color-matching these fillers can help integrate them seamlessly into the design.Design Decorative Saw-Cuts or Patterns:
Incorporating decorative scoring or saw-cut patterns can intentionally disguise and incorporate cracks or imperfections into your floor design, resulting in a unique and attractive feature.Set Clear Expectations:
Communicate openly with clients about the nature of concrete, ensuring they understand minor imperfections are natural and, when handled creatively, can actually enhance visual appeal.
By specifying upfront how to manage cracks, joints, and surface imperfections, architects ensure polished concrete floors that not only perform exceptionally well but look stunning throughout their lifetime.
In the next section, we'll discuss how architects can effectively specify slip resistance and ensure ADA compliance in their polished concrete projects.
6. Specifying Slip Resistance & Ensuring ADA Compliance
While polished concrete is admired for its sleek, reflective surface, architects must ensure that safety is just as much a priority as aesthetics—especially in commercial spaces with high foot traffic. Without proper slip-resistant specifications, polished concrete floors can become hazardous, particularly when wet. Failing to account for slip resistance doesn’t just increase the risk of accidents; it can also lead to liability issues, non-compliance with ADA (Americans with Disabilities Act) regulations, and expensive corrective work after installation.
At Floor Kings, we’ve encountered commercial projects in Port St. Lucie where polished concrete was initially installed without considering slip resistance. One such project, a high-end restaurant, featured a beautiful high-gloss finish—but after a few months, the owners realized that spills and moisture made certain areas dangerously slippery. To fix this, the floors had to be retrofitted with anti-slip treatments, leading to additional costs and operational disruptions. This could have been avoided with the right specifications from the start.
To ensure safety while maintaining the beauty of polished concrete, architects should include the following elements in their specifications:
Choose the Right Gloss Level:
A high-gloss finish may look stunning, but in areas prone to moisture (entryways, kitchens, restrooms), a satin or matte finish is often a safer choice.Specify Anti-Slip Additives:
Incorporating micro-aggregate slip-resistant treatments can improve traction without compromising aesthetics. These treatments can be integrated into the polishing process or applied as a topcoat.Utilize Selective Surface Texturing:
In high-risk areas, mechanical texturing (such as light grinding or scoring) can increase surface traction while preserving the polished concrete look.Ensure ADA Compliance:
The ADA mandates that commercial flooring meets a specific coefficient of friction (COF) to ensure accessibility and safety. Polished concrete floors should align with these requirements, particularly in areas open to the public.
By proactively specifying slip-resistant measures, architects can create polished concrete floors that are as functional and safe as they are visually appealing.
Next, we’ll discuss why including a clear maintenance plan in your specifications is essential for preserving the longevity and appearance of polished concrete floors.
7. Including a Maintenance Plan in Your Specifications
One of the most common misconceptions about polished concrete is that it’s completely maintenance-free. While it does require significantly less upkeep compared to other flooring materials, architects must include a clear maintenance plan in their specifications to ensure the longevity and appearance of the floor. Without proper care, even the highest-quality polished concrete floors can lose their luster, develop surface scratches, or become stained over time.
At Floor Kings, we’ve seen commercial clients in Port St. Lucie face premature dulling of their polished concrete floors simply because their maintenance teams were using the wrong cleaning products. One high-traffic retail store, for example, regularly used harsh chemicals designed for tile and grout, which degraded the floor’s shine and required costly refinishing much sooner than expected.
To help clients avoid similar issues, architects should include the following maintenance guidelines in their specifications:
Daily Maintenance:
Recommend dry dust-mopping or microfiber sweeping to remove dirt and debris that could cause surface abrasions.Weekly/Monthly Deep Cleaning:
Specify the use of pH-neutral cleaning solutions specifically formulated for polished concrete. Avoid acidic, ammonia-based, or abrasive cleaners, as they can degrade the polished surface.Preventative Measures:
Suggest placing mats or rugs at entrances to minimize dirt and moisture tracking.Periodic Re-Polishing or Burnishing:
Depending on traffic levels, commercial polished concrete floors may require re-polishing or high-speed burnishing every few years to maintain their original gloss.
Providing these maintenance specifications upfront ensures that polished concrete floors continue to look stunning for years while preventing unnecessary restoration costs down the road.
Next, we’ll discuss why partnering with an experienced polished concrete contractor early in the process is essential for achieving the best results.
8. Choosing the Right Polished Concrete Partner
Even with the most precise specifications, the success of a polished concrete project ultimately depends on the expertise of the contractor executing the work. Architects and designers can create a flawless plan, but if the contractor lacks experience in polished concrete installation, the final result may not meet expectations. That’s why choosing the right polished concrete partner early in the design process is critical.
At Floor Kings, we’ve worked with numerous architects and designers in Port St. Lucie who came to us after encountering issues with contractors unfamiliar with the intricacies of polished concrete. One project, a corporate office space, suffered from inconsistent aggregate exposure and an uneven polish due to improper grinding techniques. By the time we were brought in, costly corrective work was required to salvage the floor—something that could have been avoided by selecting the right contractor from the start.
When selecting a polished concrete specialist, architects should look for:
Experience & Portfolio:
Ensure the contractor has a proven track record of successfully completing commercial polished concrete projects similar to yours.Technical Knowledge:
A reputable contractor should be well-versed in concrete mix specifications, polishing techniques, and surface treatments.Transparent Communication:
The best contractors will collaborate with architects early in the process, providing valuable input on feasibility, material selection, and potential challenges.Mock-Ups & Samples:
Always request physical samples or mock-ups before full-scale installation to ensure the final product aligns with the design vision.
By partnering with a trusted polished concrete contractor like Floor Kings early in the project, architects can ensure that their vision translates seamlessly into reality, avoiding costly mistakes and delivering a polished concrete floor that exceeds client expectations.
In the final section, we’ll summarize key takeaways and explain how Floor Kings can help you achieve the perfect polished concrete floor.
9. Bringing Your Polished Concrete Vision to Life with Floor Kings
Specifying polished concrete correctly is the key to ensuring a commercial space has a flooring solution that is not only visually stunning but also durable, safe, and long-lasting. From selecting the right concrete mix and aggregate exposure to addressing moisture control, slip resistance, and maintenance, every detail matters. By clearly defining these elements in your specifications, you set the foundation for a successful installation that meets both aesthetic and functional expectations.
At Floor Kings, we specialize in helping architects and designers bring their polished concrete visions to life. With years of experience working on commercial projects throughout Port St. Lucie, FL, we understand the challenges and technical requirements that come with specifying and installing polished concrete. Our team works closely with architects from the early planning stages through final installation, ensuring that every specification is met with precision and craftsmanship.
Let’s create a polished concrete floor that stands the test of time. Call Mike at 772-370-7938 or email [email protected] to discuss your next project and see how Floor Kings can help you achieve the perfect flooring solution.