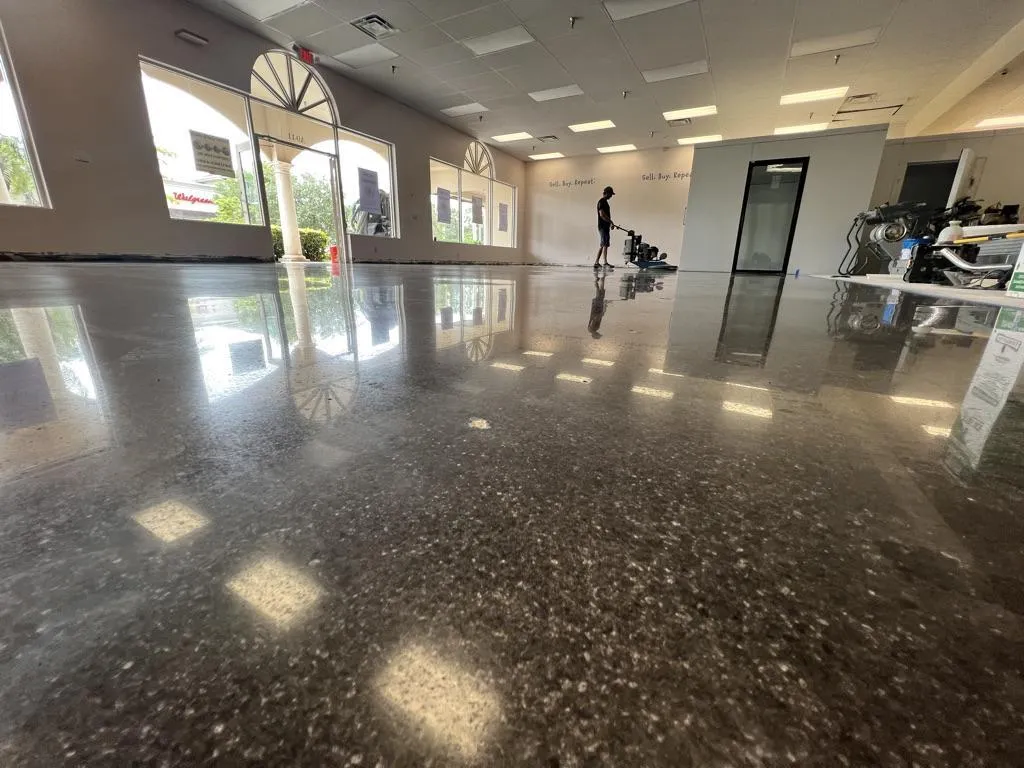
The Ultimate Guide to Polished Concrete for Commercial & Industrial Spaces in Port St. Lucie, FL
Polished concrete is quickly becoming the go-to flooring solution for commercial and industrial spaces across Port St. Lucie—and for good reason. It’s durable, low-maintenance, cost-effective, and built to handle the real demands of Florida businesses. In this guide, we’ll break down everything you need to know before choosing polished concrete for your facility.
Table of Contents
The Rise of Polished Concrete in Port St. Lucie
Understanding Polished Concrete: What It Is and Why It Matters
The Polished Concrete Process: From Start to Finish
Applications in Commercial & Industrial Settings
Advantages of Polished Concrete in Florida's Climate
Maintenance and Longevity: Keeping Your Floors Pristine
Cost Analysis: Investment vs. Long-Term Savings
Choosing the Right Contractor: Why Floor Kings Stands Out
Frequently Asked Questions
Let's work together
1. The Rise of Polished Concrete in Port St. Lucie
Port St. Lucie isn’t just growing—it’s evolving. Warehouses are expanding. Distribution centers are breaking ground. Office parks, schools, and medical facilities are being renovated or built from scratch. The one thing they all have in common? They need floors that can keep up.
For years, polished concrete was seen as a no-frills option. A bare-bones solution for back-of-house industrial spaces. Not anymore. Across Florida—and especially here in Port St. Lucie—polished concrete has become the go-to flooring solution for commercial and industrial environments. Why? Because it delivers real performance, low maintenance, and long-term value that other surfaces simply can’t match.
A City on the Move Needs Floors That Work as Hard as Its Businesses
Port St. Lucie has become a hotbed for logistics and industrial development. With proximity to I-95 and the Florida Turnpike, plus massive population growth across the Treasure Coast, the demand for warehouse space, light manufacturing, healthcare infrastructure, and commercial real estate is exploding.
And that means new construction—and lots of it.
But this isn’t just about building fast. Developers, general contractors, and business owners are demanding smarter, more cost-effective building materials that reduce lifecycle costs and minimize maintenance headaches. Enter: polished concrete.
Floor Kings has seen this shift firsthand. We’ve installed polished concrete floors across commercial spaces of every shape and size—spaces where forklifts roll 18 hours a day, where foot traffic never stops, where spills happen, and cleanliness matters.
We’ve watched business owners make the switch from coated surfaces and tile to polished concrete because it just makes more sense—financially and functionally.
Why Now? Timing, Climate, and Cost
There’s a reason polished concrete is hitting its stride right now in Port St. Lucie.
Climate: Florida’s humidity and heat don’t play nice with floor coatings. They peel, bubble, and fail over time. Polished concrete doesn’t rely on a coating—it is the finish.
Cost Pressure: With inflation and labor costs rising, property managers and developers are looking for materials with low maintenance demands and long lifespans. Polished concrete checks both boxes.
Design Expectations: Let’s face it—today’s commercial spaces need to look good. From office lobbies to retail storefronts, polished concrete offers a sleek, professional look that rivals tile and luxury vinyl—without the price tag.
In other words, the market is ready for it. And at Floor Kings, we’re already ahead of the curve.
Why Commercial Clients Are Making the Switch
We’re not just talking about warehouses anymore. Here’s where we’re seeing polished concrete gain serious traction:
Big-box retail: Long hours, carts, spills, and demanding cleaning routines? Polished concrete thrives.
Medical and lab spaces: Seamless, sanitary, and easy to clean—no grout lines or adhesive failure.
Schools and government buildings: Cost-effective over decades, not just months.
Auto dealerships and service centers: High-traffic, heavy-use areas with aesthetic demands? This is where polished concrete shines—literally.
We’ve had conversations with architects, facility managers, and business owners who all say the same thing: “I’m tired of replacing floors every few years.” They want something that lasts. Something that won’t turn into a money pit.
Polished concrete is the answer, and Port St. Lucie is full of properties that are ready for it.
Built for Florida. Installed by Floor Kings.
This guide is designed to walk you through everything you need to know about polished concrete for your commercial or industrial space here in Port St. Lucie.
We’ll cover:
How the process works
What it costs (and what it saves you)
Where it works best
Maintenance best practices
How to choose the right finish for your needs
And why Floor Kings is the right contractor to get it done right the first time
You need a floor that performs, holds up, and looks good doing it. Whether you're managing a warehouse expansion in Tradition or retrofitting a medical office near US-1, we’ve got the experience and the tools to deliver.
2. Understanding Polished Concrete: What It Is and Why It Matters
If you're considering polished concrete for your business, the first thing to understand is this: it's not just bare concrete with a shine. Polished concrete is a carefully engineered flooring system that transforms an ordinary slab into a dense, durable, low-maintenance surface—built for the real world, not just showrooms.
What Exactly Is Polished Concrete?
Polished concrete is created by mechanically grinding and honing the surface of a concrete slab using progressively finer diamond tooling, followed by the application of a densifier to harden the surface, and finally polishing it to the desired level of sheen.
There’s no coating. No wax. No top layer to peel or flake. The polish is built into the concrete itself. That’s what makes it ideal for commercial and industrial spaces across Port St. Lucie—especially where durability and low upkeep are non-negotiables.
When done right, you’re not just getting a smooth finish. You’re getting:
A densified surface that resists abrasion, impact, and traffic
A sealed matrix that prevents dusting and simplifies cleaning
A refined appearance that enhances light reflectivity and improves visibility
It’s not cosmetic—it’s structural.
What It Isn’t: Don’t Confuse It With Coatings
Let’s clear up a few misconceptions. Not all concrete floor treatments are created equal, and we’ve seen plenty of property managers make expensive mistakes by choosing the wrong system for their space.
Here’s what polished concrete is not:
It’s not epoxy.
Epoxy is a coating that sits on top of the concrete. It can look great, but over time it’s prone to chipping, scratching, and peeling—especially in Florida’s hot, humid climate or in areas with heavy forklift traffic. Polished concrete? Nothing to peel. Nothing to delaminate.It’s not sealed concrete.
Sealing is a basic treatment often used on garage slabs. It involves applying a film-forming product that helps resist stains. But sealers wear off. Polished concrete, on the other hand, chemically strengthens the slab and doesn’t rely on a film or membrane for protection.It’s not burnished concrete.
Some contractors “fake” a polish by applying a coating and burnishing it with heat. That’s not polishing—it’s temporary shine. And it won’t last under commercial conditions.
If you’re running a business, you need a floor that’s built for punishment. Polished concrete delivers real performance, not just surface-level shine.
Why It’s a Smart Fit for Port St. Lucie Businesses
Between the salt air, high humidity, and constant foot traffic in Florida’s coastal cities, most traditional flooring systems are fighting an uphill battle. Tile grout gets dirty and cracks. Vinyl lifts. Epoxy yellows and blisters when exposed to heat and moisture.
Polished concrete stands up to it all.
Humidity resistant – there’s no adhesive to break down
Mold resistant – there are no layers or materials that trap moisture
UV stable – nothing to yellow or fade
Low maintenance – simple cleaning keeps it looking sharp
Budget friendly – no need to recoat or replace every 5 years
Whether you run a warehouse, a car dealership, a grocery store, or a public facility, these benefits make polished concrete a long-term win—especially when installed by a crew that knows what they’re doing.
It’s Not Just About Strength—It’s About Looks Too
This isn’t your average “industrial grey.” Today’s polished concrete offers a range of design options, from matte finishes with salt-and-pepper aggregate to high-gloss showroom-grade mirrors. You can even add dyes, scoring, or decorative borders to match your brand or interior finish.
Floor Kings has delivered polished concrete that holds up under forklifts but still turns heads in client-facing spaces. It's not one-size-fits-all—we tailor each job to your space, your needs, and your aesthetic goals.
Why Experience Matters
Polishing concrete isn’t just a matter of running a machine over the floor a few times. It’s a detailed process that requires understanding the slab’s hardness, condition, moisture content, and use case.
Cut too deep and you’ll expose too much aggregate. Skip a grit and you’ll get swirl marks. Use the wrong densifier and the surface won’t hold up.
That’s why it pays to work with specialists like Floor Kings who’ve polished millions of square feet of commercial and industrial floors across Florida. We know how to read a slab. We know how to adjust to local climate conditions. And we know how to deliver floors that meet spec—every time.
3. The Polished Concrete Process: From Start to Finish
A polished concrete floor might look simple when it’s done, but the process behind it is anything but basic. At Floor Kings, we’ve spent years refining a system that produces durable, consistent, and professional results on every commercial and industrial project we touch in Port St. Lucie.
We don’t cut corners. We don’t rush. We follow a tried-and-true process that transforms concrete from rough and dusty to strong, dense, and smooth as glass. Here’s how it works.
Step 1: Evaluate the Slab
Every job starts with a walkthrough. We assess the condition of the existing concrete and ask the right questions:
Is the slab new or old?
Are there coatings, tile glue, or paint that need to be removed?
Are there cracks, pits, or spalls that need repair?
Is there moisture present?
What level of polish is appropriate for the space?
No two slabs are the same. That’s why this evaluation is critical—we’re not just polishing a floor; we’re engineering a finish that fits the environment.
Step 2: Surface Preparation
Prep is everything. Without it, the final result won’t last—and won’t look right.
This is where we:
Remove old coatings, adhesives, or sealers
Fill cracks, joints, and surface defects
Flatten the floor if needed to eliminate high spots
Address moisture issues if present
We use industrial-grade grinders with vacuum systems to keep dust controlled. Our team understands how to work around ongoing operations—we’ve completed countless projects in active businesses where coordination and cleanliness are key.
Step 3: Initial Grinding
The first grinding pass is all about opening up the concrete. We use coarse diamond tooling (usually 30–70 grit metal-bond diamonds) to remove the surface layer, clean off contaminants, and begin exposing aggregate.
This is also where we determine your desired finish:
Cream finish (minimal exposure)
Salt and pepper (light exposure)
Full aggregate exposure
The deeper the grind, the more labor and time it takes—but the more decorative potential it unlocks. We’ll walk you through your options and help you choose the right one based on aesthetics, use, and budget.
Step 4: Densification
Once the surface is opened up and leveled, we apply a densifier. This is a chemical hardener—usually a lithium silicate—that reacts with the calcium hydroxide in the concrete to form calcium silicate hydrate.
That’s not just chemistry talk—it matters. This chemical reaction:
Hardens the surface
Increases abrasion resistance
Helps prevent dusting
Locks down the matrix for polishing
A floor without densifier might shine on Day 1—but it won’t hold up under forklift tires or shopping carts six months down the road.
Step 5: Honing and Polishing
Now the real transformation begins. Using progressively finer grits of resin-bond diamonds, we refine the floor—removing the scratch pattern from the metal-bond passes and bringing out the desired sheen.
Typical progression includes:
100 grit
200 grit
400 grit
800 grit
1500 grit
3000 grit
The higher we go, the glossier the floor. But gloss isn’t everything—we help clients in Port St. Lucie choose the right finish for their environment. A warehouse doesn’t need a mirror finish. A showroom or retail lobby might. We match performance with purpose.
Every grit is methodical. We don’t skip steps. Each pass builds on the last, and we inspect the floor continuously as we go.
Step 6: Guard Application (Optional)
For clients who want extra stain protection—especially in retail, healthcare, or food service environments—we apply a penetrating guard. This adds a slight sheen boost and helps protect against oil, acids, and spills without creating a film.
It’s completely breathable and won’t peel or flake like traditional coatings.
We’ll be straight with you: some spaces don’t need it. Others do. We’ll tell you the truth, not just upsell.
Step 7: Final Polish and Cleanup
Once the floor hits its final finish, we burnish (if needed), vacuum, clean, and walk the site with the client. Every edge is finished. Every surface is clean. We don’t leave until you’re satisfied.
You’ll get:
Cleaning and maintenance guidelines
Recommendations for autoscrubbers and pH-neutral cleaners
Follow-up options for periodic touch-ups or guard reapplication
What About Timeline?
Here’s what most Port St. Lucie clients ask:
“How long will it take?”
It depends on:
Square footage
Slab condition
Desired level of finish
Small retail jobs (under 5,000 sq. ft.) might take 2–3 days.
Large industrial floors (50,000+ sq. ft.) can take 1–2 weeks, depending on complexity and logistics.
We work efficiently—but never rush. We’ll give you a schedule up front and stick to it.
Why It Pays to Hire Pros
Polishing concrete isn’t plug-and-play. One wrong move—skipping a grit, using the wrong pad, misreading a slab—and you’re stuck with swirl marks, blotchy sheen, or worse, a surface that fails.
Floor Kings has been polishing concrete in Port St. Lucie for years. We’ve worked in warehouses, medical offices, city buildings, dealerships—you name it. Our team is trained, insured, and obsessed with quality.
We don’t do second-rate. We do concrete right. The first time.
4. Applications in Commercial & Industrial Settings
Polished concrete isn’t a one-size-fits-all solution—it’s a flooring system that adapts to the needs of different industries. Whether you're managing a logistics facility, building out a retail space, or remodeling an office building, this surface works hard and looks good doing it.
In Port St. Lucie, where industrial growth is surging and retail developments are expanding fast, the demand for long-lasting, low-maintenance flooring systems has never been higher. Polished concrete delivers exactly that—and more.
Let’s break down how it performs in different commercial and industrial environments.
1. Warehouses & Distribution Centers
Heavy traffic. Forklifts. Constant movement. Dust control. Warehouses ask a lot of their floors—and polished concrete delivers.
Why it works:
Extreme durability – stands up to forklifts, pallet jacks, and rolling equipment without grooving
Dust-free surface – densified concrete eliminates surface dust and protects stored goods
Low maintenance – no waxing, no coatings, and minimal cleaning required
Bright finish – high reflectivity improves lighting conditions, which is critical in large, high-bay spaces
Whether you're operating out of a single-unit facility in Port St. Lucie or managing a multi-tenant industrial park, polished concrete helps reduce operational costs and keeps the space clean and efficient.
2. Big-Box Retail & Grocery Stores
Retail is all about first impressions. And polished concrete creates a clean, modern, and professional look that holds up to daily wear from carts, feet, spills, and displays.
What makes it ideal:
Attractive appearance – sleek, neutral aesthetic that complements any retail design
Stain resistance – optional guard application protects against spills, oils, and cleaning chemicals
Ease of maintenance – quick to mop or scrub, with no grout lines or adhesive seams
Long-term value – outlasts vinyl, tile, or carpet by years—without the recurring replacement costs
Bonus: It’s also great for acoustics in open retail layouts. With the right finish and layout design, you can reduce echo and improve overall customer experience.
3. Automotive Showrooms & Service Bays
This is one of the top spaces where form and function both need to show up. And polished concrete nails both.
In showrooms, you get:
High-gloss mirror finishes that reflect vehicles and lighting beautifully
Custom logos or inlays (if desired) to add branding and detail
Durability under tire scuffs and customer traffic
In service bays, you get:
Resistance to wear, oils, and heavy equipment
Slip-resistant finishes for employee safety
Easy-to-clean surfaces that hold up under real use
Polished concrete helps dealerships present a clean, high-end image—while simplifying maintenance in the back of house.
4. Offices, Lobbies & Public Buildings
If you want your commercial space to feel modern and intentional without blowing the budget, polished concrete delivers.
Ideal for:
Corporate offices and creative workspaces that want a clean, minimalist look
Municipal buildings and schools that need cost-effective, long-term solutions
Medical and professional suites where hygiene and simplicity matter
Why it works:
Smooth, seamless finish that avoids trip hazards and wear paths
Dye options and scored patterns to create subtle visual interest
Easy maintenance in high-foot-traffic areas
And for Port St. Lucie’s growing municipal and civic construction pipeline, polished concrete is an obvious fit—especially in lobbies, corridors, and public-use spaces that demand both appearance and performance.
5. Restaurants, Breweries & Event Spaces
These spaces walk a fine line: they need a floor that looks upscale, handles spills, and survives constant foot traffic. With the right finish, polished concrete checks every box.
You get:
Custom color dyes or aggregates for visual branding
Anti-slip additives or lower sheen finishes for safety
Durability in both front-of-house and kitchen/service areas (when paired with proper slip-resistant finishes)
In Florida, where salt air, moisture, and sand can chew up vinyl and wood in months, polished concrete offers an edge that holds up through hurricane season, tourist season, and everything in between.
6. Fitness Centers & Multi-Purpose Facilities
Big open spaces, high foot traffic, sweat, cleaning agents, and occasional dropped weights—if your flooring isn’t built right, you’ll know it fast.
Polished concrete offers:
Strong impact resistance
No grout lines or seams to trap bacteria
Low maintenance with no coatings to reapply
Moisture resistance in locker rooms and weight rooms (with optional guard or densifier protection)
It also works great in multipurpose municipal spaces—think city rec centers, gyms, performance spaces, and flex-use buildings. Clean. Durable. Low cost to maintain.
The Bottom Line
Every commercial and industrial space has its own set of demands. Some need heavy-duty performance. Others need design appeal. Many need both. That’s where polished concrete stands out: it adapts.
And when Floor Kings installs it, you’re not getting a cookie-cutter finish—you’re getting a flooring system tailored to the use case, installed by a team that understands your priorities and timeline.
We’ve worked across industries, and we’ve seen what works—and what fails. If you want your floors to last, look sharp, and stay low maintenance for the long haul, you’re in the right place.
5. Advantages of Polished Concrete in Florida’s Climate
Port St. Lucie has a lot going for it—sunshine, growth, ocean access. But when it comes to building materials, Florida’s environment is relentless. High humidity. Salt air. Intense heat. Sudden downpours. And let’s not forget the hurricane prep and recovery cycles.
Some flooring systems just aren’t made for this. Adhesives fail. Vinyl bubbles. Coatings peel. Grout molds. That’s where polished concrete pulls away from the pack. Because unlike surface treatments or fragile finishes, polished concrete is part of the slab itself—no layers to lift, no glue to break down, no surface to delaminate.
Here’s how it holds up—and why it’s the smart long-term play for commercial and industrial spaces in Florida.
No Adhesives = No Moisture Problems
Let’s start with the biggest one: moisture.
Florida slabs are notorious for high vapor emissions, especially in buildings without proper under-slab barriers (which—spoiler alert—are more common than you’d think). Most flooring systems rely on adhesives to bond to the concrete. But when vapor pushes up from the slab, it breaks those bonds over time.
The result?
Tiles pop
Vinyl curls
Epoxy peels
Carpet backing breaks down
Polished concrete skips that risk entirely. There’s no adhesive, no overlay, and nothing to trap vapor beneath the surface. It’s breathable. It’s stable. And it’s built to last—even if your slab sweats year-round.
UV-Resistant and Color-Stable
Outdoor light is no joke in Port St. Lucie. The sun’s intensity fades wood, vinyl, and many resins fast—especially in lobbies, storefronts, and bay doors with a lot of exposure.
Polished concrete? It doesn’t yellow, fade, or break down in sunlight.
And if you add integral dye or stain, the color is embedded into the slab—not just sitting on top like a painted finish. With the right guard or sealer, it’ll keep its tone for years without reapplication.
This makes it ideal for:
Retail spaces with front-facing windows
Industrial doors that stay open all day
Showrooms or auto spaces with natural light
No UV degradation. No color shift. No “sun shadow” effect you get with vinyl or coatings.
Heat-Reflective and Thermally Stable
Here’s something people don’t always expect: polished concrete can actually reduce cooling costs.
How? Because the high reflectivity of polished concrete bounces ambient light, improving interior brightness and reducing heat absorption. It doesn't hold radiant heat the way darker finishes or soft flooring can.
And unlike epoxy or urethane coatings, it doesn’t soften or discolor in hot areas. Polished concrete holds its structural integrity whether your AC’s working overtime or you’re in an uncooled warehouse space in August.
In Florida, that thermal stability makes a real difference.
Mold & Mildew Resistant
High humidity and porous flooring are a dangerous mix. Florida buildings are constantly at risk of mold growth, especially in floors that trap moisture—like carpet, laminate, or anything with seams, underlayment, or fiber.
Polished concrete is inorganic, seamless, and nonporous at the surface. There’s nowhere for mold to latch on, and nothing in the system that feeds it.
That makes it an excellent choice for:
Medical offices
Fitness centers
Schools
Restaurants and food service environments
Add in the fact that polished concrete is easy to clean, disinfect, and maintain, and you’ve got a flooring system that fights back against one of Florida’s biggest environmental risks—without chemicals or coatings.
Withstands Storm Cleanup and Recovery
Let’s talk hurricanes. When water gets in, most flooring has to come out. Wood swells. Vinyl lifts. Adhesives fail. Carpet becomes a biohazard.
Polished concrete doesn’t absorb water. It doesn’t trap contaminants. Once the space is dried out, the floor is still there—still solid. Maybe it needs a buff or a spot polish, but you’re not ripping out thousands of dollars in flooring every time there’s a leak, flood, or storm surge.
In Port St. Lucie, where storm prep and cleanup are part of life, that’s a big deal. It’s not just about durability—it’s about resilience.
Built for Florida. Backed by Floor Kings.
Flooring in Florida can’t just look good. It has to survive year-round humidity, summer heat, salt exposure, and the unexpected. Polished concrete was made for this environment. And Floor Kings has spent years tailoring every install to the realities of building in Port St. Lucie.
From warehouses in industrial parks to retail spaces off US-1, we’ve seen what works—and what doesn’t. And when it comes to commercial flooring, this one works. Period.
6. Maintenance and Longevity: Keeping Your Floors Pristine
Let’s be honest—no one wants to babysit a floor. Especially not in a commercial or industrial setting where uptime, cleanliness, and cost control matter. That’s where polished concrete really earns its reputation.
It’s one thing for a floor to look good the day it's installed. It’s another for it to still perform five, ten, even twenty years later—without constant maintenance contracts, re-coats, or shutdowns.
Polished concrete doesn’t just hold up—it gets better with time when treated right. Here’s how.
No Wax. No Strip. No Recoat.
Say goodbye to the recurring service calls and floor crew appointments. With polished concrete, there’s no topical coating to reapply. You don’t need to strip and wax. You don’t need to re-seal every few months.
Why?
Because the finish isn’t on top of the slab—it is the slab. Once that concrete is ground, densified, and polished, you’re working with a hardened surface that maintains its appearance and integrity without extra layers.
That means:
No downtime for chemical stripping
No peeling or flaking issues
No yellowing or discoloration from aged coatings
No strong odors from recoating products
You just clean it—and it keeps performing.
Daily & Weekly Maintenance: Simple and Low-Effort
Here’s what routine maintenance looks like for a typical commercial space in Port St. Lucie:
Dust mop daily using microfiber mops to remove dirt, sand, and grit
Wet mop or auto-scrub as needed (usually 2–3 times a week) with a pH-neutral cleaner
Avoid harsh degreasers, bleach, or acidic cleaners, which can dull the surface over time
That’s it. No special polishes. No buffing unless you want to restore the sheen. And even then, a quick pass with a burnisher can bring the shine right back.
For industrial facilities, we recommend investing in an autoscrubber with the proper pads—especially in high-traffic zones like loading docks and main aisles.
For retail, offices, and lobbies, regular cleaning keeps the floors looking polished and professional with minimal time and budget.
High Gloss? High Payoff—with a Little More Care
If you’ve gone for a high-gloss finish in a showroom or public-facing space, just know this: the shine looks incredible—but it’s also more revealing.
High-gloss floors can show:
Footprints
Smudges
Dust
So, keep up with daily cleaning and occasional burnishing (every few months in high-traffic areas) to maintain that crisp, reflective look. It’s worth it. And it still costs far less to maintain than vinyl or tile with waxing cycles.
Floor Kings will walk you through the best care plan based on your chosen finish level and the function of your space.
Handling Spills, Stains & Wear
Polished concrete is stain-resistant—not stain-proof. But when treated properly, it’s incredibly forgiving.
Here’s how to keep it in top shape:
Clean spills quickly—especially oil, grease, or acidic products
Use mats at entry points to trap sand and water before it hits the floor
Add a guard application in sensitive areas for extra protection (offices, food prep, medical, etc.)
Check joints yearly—filling or resealing control joints prevents edge spalling
In high-wear environments like warehouses, we sometimes recommend a maintenance polish every few years. It’s fast, affordable, and keeps the surface looking uniform without a full regrind.
Compared to Other Flooring Systems? No Contest.
Let’s be real—other flooring systems in commercial and industrial environments can be maintenance nightmares.
Vinyl Tile (VCT):
Requires stripping and waxing quarterly or semi-annually
Shows wear paths fast
Prone to lifting in humid or wet areas
Epoxy Coatings:
Look great at first, but chip and peel under wheel traffic
Require full reapplication every 5–7 years in heavy-use environments
Sensitive to surface prep and moisture intrusion
Tile:
Grout stains, cracks, and traps dirt
Repairs are patchy and expensive
Not ideal for forklifts or heavy carts
Polished Concrete:
Doesn’t peel, chip, or lift
Zero waxing, ever
Seamless surface, no grout
Long-term durability with simple cleaning
That’s why more Port St. Lucie businesses are ditching short-term fixes and going with one flooring system that lasts.
How Long Does It Really Last?
A professionally installed, properly maintained polished concrete floor can easily last 20 years or more in commercial settings. In industrial applications, you’re still looking at 15–20+ years—depending on traffic, usage, and care.
There’s no reinstallation. No tear-outs. Just a solid slab doing its job year after year.
And if the surface ever starts to dull or wear in certain areas? We don’t replace it—we just re-polish it. That’s a one-day service, not a full flooring overhaul.
Floor Kings Sets You Up for Success
We don’t just install the floor and leave you guessing. After every project, we provide:
Customized cleaning instructions
Recommended products and equipment
Maintenance tips based on your industry and use case
Optional follow-up service plans for long-term clients
Because a great floor isn’t just about install day—it’s about everything that happens after. And Floor Kings is with you every step of the way.
7. Cost Analysis: Investment vs. Long-Term Savings
If you’re managing the budget for a commercial or industrial space in Port St. Lucie, you’re always looking at the big picture. It’s not just about the upfront cost—it’s about how much a flooring system will cost you over the next 5, 10, or 20 years.
That’s where polished concrete really sets itself apart. It may not always be the cheapest to install on Day 1, but when you look at the total cost of ownership, it consistently comes out ahead.
What You Can Expect to Pay in Port St. Lucie
For a typical commercial polished concrete project, here’s what you can realistically expect:
Basic finishes, like matte or light polish with minimal prep, usually fall between $4 to $5.50 per square foot.
Mid-range finishes with moderate aggregate exposure or dye can run $5.50 to $7 per square foot.
High-end finishes—think full aggregate exposure, custom scoring, logos, or decorative borders—can go from $7 to $10+ per square foot.
These numbers depend on the size and condition of the space, but they include everything—grinding, patching, densification, polishing, cleanup, and post-install instructions. Floor Kings doesn’t hide costs or tack on fees halfway through the job.
Factors That Affect Pricing
Several variables can push the price up or down:
Slab condition: Older or damaged concrete needs more prep, grinding, and repair, which adds time and labor.
Coating removal: If we’re taking up old tile, glue, carpet adhesive, or epoxy, that adds to the workload.
Finish level: The higher the gloss or the more exposed the aggregate, the more grinding passes are required.
Size of the space: Bigger jobs tend to bring the cost per square foot down due to efficiencies in setup and workflow.
Custom touches: Logos, scoring, color dyes—those are value-adds, but they do add time and cost.
We give you a clear quote up front. You’ll know exactly what you’re paying for, why it costs what it does, and what to expect at every stage.
Why the Investment Makes Sense
Let’s talk about real-world return on investment.
Polished concrete holds its own against any commercial flooring system when it comes to lifecycle cost. It requires minimal upkeep, has no coating cycles, and doesn’t need to be replaced every 5–7 years like tile, VCT, or carpet. That adds up fast in savings.
Plus, it’s incredibly resistant to wear and tear. With basic maintenance—dust mopping and auto-scrubbing—it easily lasts 15–20 years or more in commercial settings. Compare that to other flooring options, and you’re replacing or repairing them two or even three times during that same period.
Additional Savings You Might Not Have Considered
There are also hidden ways polished concrete saves you money:
Lighting efficiency: Polished floors reflect ambient light, reducing the need for excessive overhead lighting.
Fewer janitorial hours: You don’t need a specialized crew to strip or wax the floor. Your team can clean it with basic tools and neutral cleaners.
Reduced downtime: No need to shut down for recoating or repairs. If touch-ups are ever needed, they’re usually localized and fast.
Disaster resilience: After floods or hurricanes—which Florida is no stranger to—you’re not replacing flooring. Polished concrete survives where wood, vinyl, and carpet don’t.
What’s the Payback?
In our experience, Port St. Lucie businesses typically recoup the upfront cost of polished concrete within 2 to 4 years—just from avoiding material replacement and minimizing maintenance expenses.
After that, it keeps paying you back every year you stay operational without floor-related headaches. We’ve seen it firsthand. Customers who switched from epoxy or tile tell us it’s the best flooring decision they’ve ever made.
Floor Kings Doesn’t Just Install Floors—We Deliver Value
We’re not here to be the cheapest bid. We’re here to be the most valuable partner. Our quotes are designed around real performance. We price based on what your slab needs, not what makes the spreadsheet look good temporarily.
If your goal is to stop dealing with floor failures, save money in the long run, and get a durable, good-looking system that fits your operations, we’ll help you get there.
8. Choosing the Right Contractor: Why Floor Kings Stands Out
Here’s the truth about polished concrete: the product is only as good as the people installing it. You can have the best concrete in the world, the highest-grade densifier, and the top-tier grinding equipment—but if the contractor doesn’t know what they’re doing, none of that matters.
A poorly installed polished concrete floor will:
Show swirl marks and patchy gloss
Wear unevenly under traffic
Fail to harden correctly
Crack, pit, or dust within a few years
That’s not just disappointing. It’s expensive. And avoidable.
In Port St. Lucie and the surrounding area, Floor Kings has built a reputation for getting it right the first time. Our floors don’t just shine—they last. And that’s because we take the process seriously from the moment we walk your site.
Experience That Matters
We’re not new to this. Floor Kings has been serving commercial and industrial clients across Port St. Lucie for years. We’ve handled:
Warehouses and distribution centers
Medical offices and labs
Showrooms and retail stores
City and county buildings
Office lobbies, gyms, and public-use facilities
We understand the difference between polishing a 2,000-square-foot storefront and a 150,000-square-foot logistics facility. The workflow changes. The logistics change. The expectations change. Our crews are trained for that—and they deliver.
Site-First Approach, Not “One Size Fits All”
Some flooring contractors show up with one system and try to make it work for every slab. That’s not how we operate.
We start with:
A full walkthrough and assessment of your slab’s condition
A clear understanding of your goals—traffic type, finish level, timeline, budget
Real recommendations tailored to your space—not a recycled spec sheet
We’ll tell you what’s possible, what’s realistic, and what will give you the best value long term. We don’t oversell. We don’t install something that won’t last.
Our Process Is Built on Precision
At Floor Kings, we don’t guess our way through your project. Every crew member is trained on:
Concrete hardness testing
Moisture evaluation
Correct tooling and pad selection
Precision grinding and cross-hatching techniques
Surface densification and curing procedures
Finish level matching and quality control
We follow a tight, repeatable process that delivers consistent results across every square foot of your facility.
And we don’t subcontract. Our crews are our own—trained, insured, and experienced.
We Show Up When We Say We Will
Look—we know how construction timelines go. Delays, no-shows, poor communication... it’s frustrating. When we commit to a start date, we’re there. On time. With the right equipment. Ready to go.
We don’t bounce from job to job. We focus on your project until it’s done—and done right.
Support That Doesn’t Stop After the Last Grit
When we finish polishing your floor, we’re not walking away and ghosting you. You’ll get:
A walkthrough of the final product
A full care and maintenance plan
Guidance on cleaning products and equipment
Options for follow-up polishing or spot repairs if needed
If anything comes up after install, we’re a phone call away—not a voicemail box.
Trusted by Local Businesses
We’ve earned the trust of local contractors, property managers, and business owners throughout Port St. Lucie because we do what we say we’re going to do.
You want a floor that:
Lasts for decades
Performs under pressure
Looks sharp for your clients
Doesn’t drain your maintenance budget
We build that floor. Every time.
When you hire Floor Kings, you’re not getting a couple of guys with a rented grinder. You’re getting a polished concrete partner with the experience, professionalism, and commitment to back your project with real results.
9. Frequently Asked Questions
1. How long does it take to install polished concrete?
It depends on the size of the space, the condition of the existing slab, and the finish you’re aiming for. Smaller jobs (under 5,000 sq. ft.) can take 2–3 days. Larger jobs (50,000+ sq. ft.) may take a week or more. If your facility needs to remain partially operational during install, we’ll work in phases to keep disruptions minimal.
2. Can you polish existing concrete, or does it have to be new?
Absolutely—we polish existing concrete all the time. In fact, most of our projects in Port St. Lucie are refurbishments of older slabs. As long as the slab is structurally sound, we can grind down surface imperfections, fill cracks, and restore it to a high-performance finish.
3. What kind of maintenance does it need?
Day-to-day maintenance is simple: dust mopping and regular scrubbing with a neutral cleaner. That’s it. No wax, no stripping, no coatings to reapply. We’ll give you a cleaning schedule tailored to your facility’s use and traffic patterns.
4. Is it slippery when wet?
When finished properly, polished concrete meets or exceeds slip-resistance standards—even in wet conditions. If your space requires additional traction (like food prep areas, service bays, or gyms), we can adjust the gloss level or apply traction-enhancing treatments during the install.
5. Can I add color or patterns to polished concrete?
Yes. We can apply integral color dyes in a wide range of tones—greys, browns, reds, blues, and more. We can also add scored lines, decorative borders, or even embed logos. Keep in mind that color may vary slightly depending on the slab’s makeup, but we’ll test everything before we commit.
6. What happens if the floor gets damaged?
Good news: polished concrete is incredibly easy to repair. In most cases, we can spot-grind and repolish the affected area without tearing out the whole floor. If a forklift leaves a scuff or a chemical stain appears, we can fix it fast with minimal disruption.
7. How long will it last?
With proper care, a polished concrete floor can last 15 to 20+ years in commercial settings—longer in low-traffic areas. There’s no need for replacement or full resurfacing unless there’s major structural slab damage.
8. Can I polish my warehouse floor while staying open?
Yes, depending on the space and layout. We often work in phases or during off-hours to minimize impact on operations. Our crews are trained to work around active job sites, and we use vacuum systems for dust control to keep the space clean and safe.
9. Is polished concrete environmentally friendly?
Yes—polished concrete is one of the most sustainable flooring systems available. It uses the existing slab (no added materials), produces no VOCs, reduces lighting energy use through reflectivity, and doesn’t require harsh chemicals for cleaning. It also qualifies for LEED points.
10. How do I get a quote?
Simple. Give Mike at Floor Kings a call at 772-370-7938, send an email to [email protected] or fill out our contact form. We’ll schedule a site visit, walk your space, discuss your needs, and provide a detailed quote with zero pressure. If the floor’s not a good candidate for polishing, we’ll tell you straight—we don’t do jobs that won’t last.
Let’s Work Together
If you’re running a commercial or industrial facility in Port St. Lucie, you don’t have time for flooring systems that wear out, fall apart, or drain your maintenance budget. You need something that holds up under pressure, looks sharp, and keeps your operations moving.
Polished concrete does exactly that. And when it’s installed by Floor Kings, it’s done right the first time—no cut corners, no guesswork, no surprises. Just proven performance, clean execution, and a team that shows up when we say we will.
Whether you’re building out a warehouse, remodeling a medical office, or upgrading retail space, we’ll walk your slab, give you honest answers, and deliver a polished concrete system built around your goals—not just a glossy finish.
You get:
Expert installation from a trusted local contractor
A floor that’s tough, low-maintenance, and built for Florida’s climate
Support before, during, and after the job
A finished product you’ll be proud to show off
We don’t sell floors. We build long-term value for business owners, facility managers, developers, and builders who expect quality.
Call Mike at 772-370-7938
Email [email protected]
Fill out our contact form
Let’s talk about your project. Let’s walk the space. Let’s build a floor that works as hard as you do.