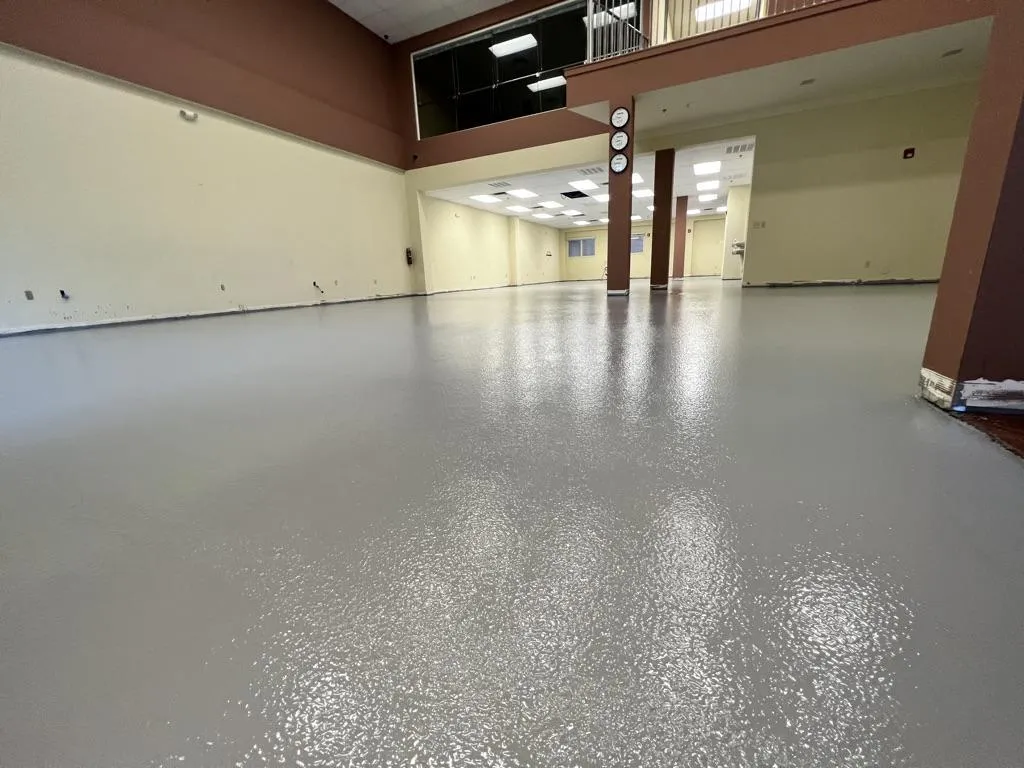
What Ruins Epoxy Flooring in Port St. Lucie: Pitfalls & Prevention
Epoxy flooring has become the go-to choice for homeowners and businesses in Port St. Lucie looking for surfaces that combine style with serious durability. You might see it brightening up residential garages or fortifying high-traffic retail spots, and it’s easy to understand why: epoxy resists stains, holds up under heavy loads, and adds a polished finish that elevates any space. Yet even the best epoxy floors can be compromised by a handful of preventable pitfalls—ranging from sloppy installation to rough daily use. In this blog post, we’ll explore what typically ruins epoxy flooring and how taking the right steps can keep your floors in peak condition for the long haul.
Table of Contents
The Appeal of Epoxy Flooring
Common Problems That Undermine Epoxy Floors
Inadequate Surface Preparation
Unsuitable Installation Environment
Subpar Epoxy Products or Incorrect Formulations
Rushing or Neglecting Proper Curing
Harsh Chemicals, Heavy Impacts, and Misuse
Lack of Maintenance and Improper Cleaning
Florida’s Climate & Local Factors That Can Damage Epoxy
1. The Appeal of Epoxy Flooring
Epoxy flooring has turned heads in Port St. Lucie for good reason. Residents along Florida’s Treasure Coast are discovering that it blends a polished, professional look with the toughness you’d expect from a high-grade protective coating. With proper installation, epoxy stands up to salty air wafting in from the coast, occasional drips of chlorine from pool areas, and the day-to-day wear of an active household or bustling commercial setting. It’s no wonder you see it popping up everywhere—from local auto workshops to stylish residential garages.
Unlike tile or bare concrete, epoxy offers a continuous surface without grout lines or cracks, which makes cleaning as simple as a quick sweep or mop. It’s also highly versatile in design; you can go for a sleek, monochromatic finish that brings modern flair, or choose decorative flakes for added texture and personality. That freedom means business owners can stay true to their brand image while homeowners enjoy floors that match their personal taste.
Of course, even the best epoxy flooring can fail if it’s not treated right. Rather than assume it’s bulletproof, it pays to learn the pitfalls that can undermine its performance. In the sections ahead, we’ll explore the most common mistakes and show you how to avoid them—so you can enjoy a long-lasting, beautiful floor in Port St. Lucie.
2. Common Problems That Undermine Epoxy Floors
Epoxy flooring is known for its durability and sleek finish, but it isn’t indestructible. Certain mistakes can erode its protective qualities, and the result is often a floor that peels, chips, or becomes uneven well before its time. Fortunately, most of these issues are completely avoidable. If you understand what causes epoxy floors to fail, you’ll be better prepared to make informed decisions, whether you’re installing a new floor or maintaining an existing one.
Here’s a quick look at the biggest threats to epoxy flooring:
Poor Preparation of the Concrete Slab
Epoxy can’t bond securely to a surface that’s dusty, greasy, or riddled with cracks. Skipping crucial steps like degreasing and grinding leaves pockets of air and debris that weaken adhesion.Extreme or Uncontrolled Environment
Epoxy is sensitive to both moisture and temperature swings. If there’s too much humidity or the temperature isn’t ideal during application, the coating may not cure properly.Using Substandard Epoxy Products
Bargain-bin kits might seem cost-effective, but they often lack the quality needed to withstand Port St. Lucie’s humidity, salt air, and frequent sunshine.Cutting Corners on Curing Time
Even the best epoxy needs enough time to harden before it’s subjected to foot traffic or heavy machinery. Rushing this step leads to impressions or blemishes that can’t always be repaired easily.Exposure to Harsh Chemicals or Physical Abuse
Although epoxy is tough, concentrated acids, pools of oil, or heavy impacts can still damage an improperly installed or poorly maintained surface. For instance, a simple act like dragging metal equipment across the floor can leave gouges.Infrequent Cleaning and Upkeep
A low-maintenance floor isn’t a “no-maintenance” floor. Allowing debris and spills to linger can wear down topcoats faster than you might expect, ultimately undermining the floor’s overall integrity.
By keeping these common issues in mind, you’re already one step ahead of the game in protecting your epoxy flooring. In the next sections, we’ll unpack each hazard in greater detail, shedding light on why these problems arise—and, more importantly, how you can prevent them in the first place.
3. Inadequate Surface Preparation
When done correctly, epoxy flooring bonds tightly to concrete, forming a seamless surface that can last for years. The key phrase here is “when done correctly,” because preparation is crucial. If the slab isn’t well-cleaned, repaired, and properly profiled, no amount of high-quality epoxy will hold up. Hidden dust, oils, and cracks can undermine adhesion, leading to premature peeling or flaking.
Skipping Essential Cleaning & Degreasing
Epoxy can’t bond well to a surface contaminated with grease, old sealers, or ground-in dirt—much like trying to paint over a dusty wall.
Concrete Degreasers: Specialized cleaners break down stubborn automotive oils, chemical spills, and other residues that ordinary mopping can miss.
Targeted Cleanup: Beyond general cleaning, look for areas where oily residue may have settled—like around workbenches or car parking spots—and tackle these with extra care.
Overlooking Cracks & Surface Defects
Tiny cracks may appear harmless at first, but they can become major weak points. Once epoxy is laid down, any ongoing movement or expansion in the concrete may create visible cracks in the finished floor.
Crack Repair Compounds: Choose fillers specifically designed to bond with both concrete and epoxy, ensuring a seamless transition.
Leveling Low or High Areas: Floors that aren’t reasonably flat can create stress points. If you find obvious dips or rises, correct them so the epoxy layer doesn’t face uneven weight distribution.
Prioritizing a Proper Surface Profile
Epoxy bonds best to a surface that has a slight texture or “tooth.” If the concrete is too smooth, the coating can’t achieve a strong mechanical bond, leading to potential lifting later on.
Mechanical Grinding: Using specialized equipment to roughen the concrete is a tried-and-true method for giving epoxy something to grip. Think of it like lightly sanding wood before painting—the goal is to create a consistent surface that promotes adhesion.
Managing Moisture and Humidity
Port St. Lucie’s subtropical climate often means high humidity and occasional rain. If moisture seeps into the slab or indoor air is too damp, it can jeopardize how well the epoxy cures.
Moisture Tests: Tools like calcium chloride kits or digital meters can measure vapor emissions from the concrete.
Climate Control: Using dehumidifiers or air conditioning while installing epoxy helps keep humidity in check, allowing the coating to cure without trapped moisture.
Why Thorough Prep Pays Off
Shortcuts during preparation lead to some of the most common epoxy failures. Even if you invest in a premium product, skipping a step here—like leaving behind grease spots or ignoring hairline cracks—can quickly turn a promising project into a disappointing one. In the long run, it’s much cheaper and less disruptive to address these details from the beginning than to tear out a failing floor and start all over.
Next, we’ll dive deeper into how environmental conditions—particularly heat, humidity, and dust—can make or break epoxy flooring in a place like Port St. Lucie.
4. Unsuitable Installation Environment
Port St. Lucie’s subtropical climate can be both a blessing and a challenge for epoxy flooring. Warm weather is great for outdoor activities, but excessive heat and humidity can throw off the epoxy curing process if not carefully managed. Dust and airborne particles can also interfere with a flawless installation. Even if you’ve prepped the concrete perfectly, the surrounding environment can sabotage your hard work when conditions are less than ideal.
Humidity and Temperature Concerns
A certain range of temperature and humidity is best for epoxy application. Go too hot, and the material may cure too quickly, leaving behind uneven patches or bubbles. If it’s too cool, curing slows down, inviting dust or bugs to stick before the coating sets.
High Humidity Risks: When the air is laden with moisture, water vapor can get trapped under or within the epoxy, creating cloudy spots or fish-eye imperfections. If you’ve ever seen small, crater-like bubbles on a finished floor, trapped moisture is often to blame.
Heat and Sun Exposure: In garages or commercial spaces with large bay doors, intense sunshine can warm up the floor slab more than you’d expect. If the slab temperature is significantly higher than the epoxy’s ideal range, the coating may skin over prematurely, leaving a tacky mess underneath.
Airborne Dust and Debris
Areas under construction or renovation are notorious for airborne particles. Even in a seemingly clean environment, everyday activities can stir up dust that drifts onto the wet epoxy, creating blemishes.
Foot Traffic: Anyone walking through the space during application can track dust, hair, or other debris onto the coating. It only takes a small speck to disrupt the smooth finish.
Open Doors and Windows: A refreshing breeze might sound appealing, but strong drafts can push in yard debris or sand—especially in a coastal city like Port St. Lucie. Controlling airflow goes a long way toward a pristine surface.
The Role of Ventilation
While you don’t want a wind tunnel blowing contaminants onto your fresh epoxy, a bit of ventilation helps with curing—especially if you’re concerned about fumes in a tight indoor environment. It’s about striking a balance between promoting airflow and protecting the wet coating from dust and unpredictable gusts.
Controlled Airflow: Setting up fans or temporary barriers can redirect or limit outside air without completely sealing off the area. This approach helps dissipate fumes and regulate temperature without introducing constant drafts.
Monitoring During Curing: Keeping an eye on the floor in the first few hours is critical. If you spot debris, carefully remove it before the epoxy sets completely.
Scheduling Your Installation
Timing matters. Some installers prefer working early in the morning or later in the evening when daily temperatures dip slightly and humidity might be lower. By choosing the cooler part of the day, you reduce the risk of the epoxy curing unevenly.
Seasonal Considerations: In Port St. Lucie, summers can be muggy. If possible, you might schedule epoxy work in spring or fall for more stable conditions. That said, an experienced team with the right equipment can still do a quality job year-round.
Why Environment Matters
Even a perfectly prepared slab can fail if the atmosphere isn’t right. Heat, humidity, and dust are not just minor inconveniences—they can undermine everything from how well the epoxy bonds to its final appearance. Paying close attention to the environment during installation sets the stage for a resilient floor that lasts. Next, we’ll discuss how using subpar or mismatched epoxy products can compound these issues and lead to a prematurely damaged surface.
5. Subpar Epoxy Products or Incorrect Formulations
Choosing the wrong epoxy for your Port St. Lucie project can be just as detrimental as botching the concrete prep. Even if you time your installation perfectly and manage the environment well, using low-quality resin or mixing components incorrectly can ruin the floor’s performance. Epoxy formulations vary widely, so it’s worth knowing the differences before you dive in.
Bargain Kits vs. Industrial-Grade Epoxy
It’s tempting to grab a discount “all-in-one” kit and hope it delivers professional results. Unfortunately, most cut-rate kits lack the resilience needed to handle Florida’s humidity, seaside salts, and high foot traffic.
Lower Solids Content: Many cheaper products are less than 100% solids, meaning they include solvents that evaporate as the coating cures. This leads to a thinner, weaker layer prone to peeling.
Limited Chemical Resistance: If the product isn’t formulated for heavy-duty use, even mild chemicals like brake fluid or cleaners can degrade the surface over time.
Mixing Ratios and Hardener Quality
Epoxy typically comes in two parts: resin and hardener. If the ratio is off or the components aren’t well-made, you might see problems like sticky areas, discoloration, or a floor that never fully cures.
User Error: DIY enthusiasts sometimes guess the mixture proportions or eyeball the hardener, which can cause uneven hardness across the surface.
Hardener Variability: High-grade systems use carefully refined chemicals to ensure predictable results, whereas inferior products may have inconsistent curing properties.
Tailoring Formulas to the Application
Certain epoxies are designed for garages, while others excel in commercial kitchens or marine environments. Using the wrong formula is a recipe for disappointment.
Temperature Tolerances: Some blends can handle the heat of a Port St. Lucie summer without curing too quickly, while others are meant for cooler conditions.
UV-Stable Coatings: If your floor will be exposed to sunlight, a topcoat with UV inhibitors helps prevent fading or yellowing over time.
How Inferior Products Falter
Even if a low-grade epoxy looks fine right after installation, microscopic weaknesses can emerge fast. You might notice:
Early Cracking or Chipping: Areas under stress—like tire contact points or heavy equipment—develop micro-fractures in the coating.
Finish Dulling or Yellowing: Cheap epoxies often lose their shine or change color, especially under harsh UV exposure.
Peeling at Edges or Seams: A weak bond leads to gradual delamination, typically starting around the perimeter where moisture or scuffs are most common.
Why It Pays to Invest in Quality
Opting for industrial-grade or professional-level epoxy might cost more initially, but it spares you from premature failures and the hassle of re-coating within a year or two. Locals who turn to trusted installers like Floor Kings benefit from materials that are formulated for Florida’s climate—ensuring a finish that stands up to the elements. High-quality epoxy, combined with proper prep and smart installation timing, sets the stage for a floor that remains smooth and sturdy for years.
Up next, we’ll examine how a rushed or overlooked curing process can sabotage even the best products, emphasizing why patience and controlled conditions during curing are non-negotiable.
6. Rushing or Neglecting Proper Curing
A perfectly installed epoxy floor can still fail if the curing process is rushed or interrupted. Epoxy doesn’t just “dry”—it undergoes a chemical reaction that hardens it into a tough, seamless surface. If that reaction is cut short, the floor may never reach its full strength, leading to weak spots, bubbling, or even complete delamination.
Why Curing Time Matters
Unlike paint, epoxy doesn’t simply air-dry. The curing process happens in stages, and each one must be completed before the floor is ready for use:
Initial Set (First 12-24 Hours): The epoxy becomes tack-free but is still soft underneath.
Full Cure (3-7 Days): The coating reaches its maximum hardness and chemical resistance.
If traffic is allowed on the floor too soon, whether it’s foot traffic or vehicles, it can leave permanent impressions or cause the layers to separate.
Common Mistakes That Ruin the Curing Process
Even with the right epoxy and good preparation, curing mistakes can undo all the hard work. Here’s what often goes wrong:
Walking on the Floor Too Soon: Even if the surface feels dry, the layers underneath are still bonding. Walking on it too soon can create dull patches or weak spots.
Driving on the Floor Too Soon: Garages need extra cure time before they’re ready for cars. Tires can leave indentations or even pull up uncured epoxy.
Humidity and Moisture Exposure: Port St. Lucie’s humid climate can slow down or interfere with curing. If moisture gets trapped beneath the surface, it can cause bubbling.
Temperature Swings: Drastic temperature changes, such as a cold night followed by a hot day, can affect how evenly the epoxy sets.
The Right Way to Cure Epoxy Floors
To ensure a proper cure, follow these best practices:
Respect Manufacturer Guidelines: Every epoxy system has a recommended cure time—stick to it.
Block Off the Area: Keep people and pets off the floor for at least 24-48 hours, and avoid placing heavy objects for several days.
Control the Climate: Using air conditioning or dehumidifiers in humid conditions can speed up curing without compromising quality.
Wait for Vehicles: If you’re coating a garage floor, don’t park on it for at least 5-7 days to allow full chemical hardening.
What Happens If Epoxy Doesn’t Cure Properly?
A poorly cured epoxy floor may look fine at first, but problems will emerge quickly:
Soft or Sticky Areas: Some sections might remain slightly tacky, never fully hardening.
Peeling or Lifting: The bond between layers weakens, and parts of the floor may start lifting, especially near high-traffic zones.
Scuffing and Damage: Because the floor never reached full hardness, it wears down much faster than a properly cured installation.
The best epoxy floors take time to develop their full durability. While it might be tempting to rush back into the space, giving the floor the proper time to cure ensures it will last for years instead of months.
Next, we’ll discuss how daily wear and tear—especially from chemicals, heavy impacts, and improper use—can ruin epoxy flooring if not managed correctly.
7. Harsh Chemicals, Heavy Impacts, and Misuse
Epoxy flooring is built for durability, but that doesn’t mean it’s invincible. While it can withstand a lot more abuse than traditional concrete, certain chemicals, excessive weight, and improper use can wear it down over time. Understanding what epoxy can and can't handle helps you avoid preventable damage and extend the life of your floor.
Chemical Exposure: What Eats Away at Epoxy?
Epoxy floors are highly resistant to chemicals, but prolonged exposure to harsh solvents, acids, and oils can degrade the protective topcoat and weaken the bond to the concrete.
The biggest culprits include:
Battery acid – Found in car batteries and some industrial equipment, battery acid can cause etching and discoloration if left to sit.
Brake fluid & gasoline – Auto shops and home garages must be careful, as petroleum-based chemicals can wear away the protective layer.
Industrial degreasers & harsh cleaners – Not all cleaning products are epoxy-safe. High-pH or solvent-based degreasers can strip the finish over time.
Salt & chlorine – Port St. Lucie’s coastal air carries salt, which can dull epoxy if not cleaned regularly. Chlorine from pool areas can also degrade the finish if allowed to build up.
How to Prevent Chemical Damage:
Clean spills immediately—don’t let harsh liquids sit.
Use epoxy-safe cleaners (pH-neutral solutions work best).
If using strong chemicals in your workspace, apply an extra protective topcoat for added durability.
Heavy Impacts and Dropped Objects: What Epoxy Can (and Can’t) Handle
Epoxy flooring is incredibly strong, but high-force impacts can still cause chips, cracks, or dents. While this isn’t an issue for normal foot traffic or rolling carts, certain conditions can push the limits.
Things that can damage epoxy floors:
Dropped heavy tools or weights – A wrench, dumbbell, or jackhammer hitting the floor at the wrong angle can cause a chip.
Forklifts & heavy equipment – While industrial-grade epoxy can handle forklift traffic, repeated sudden impact in the same spot can weaken the floor.
Dragging sharp or metal objects – Metal racks, pallet jacks, or furniture with rough legs can scrape the surface if dragged without protection.
How to Prevent Impact Damage:
Use rubber mats in areas where heavy tools are handled frequently.
Lift, don’t drag furniture or equipment across the floor.
For commercial or industrial settings, consider a thicker epoxy coat to absorb impacts better.
Misuse: What Epoxy Floors Aren’t Meant For
Epoxy flooring is versatile, but using it for the wrong purpose can lead to early failure. Here are some common mistakes:
Using indoor epoxy outdoors – UV exposure can cause standard epoxy to fade and yellow. If using epoxy outside (e.g., on a pool deck or patio), choose a UV-resistant polyaspartic or polyurethane topcoat.
Skipping the proper topcoat – Some people apply epoxy without sealing it with a UV-resistant or chemical-resistant topcoat, leaving it vulnerable.
Exposing epoxy to excessive heat – While epoxy can handle moderate heat, welding sparks, hot tires, or open flames can discolor or even soften the surface.
How to Prevent Misuse Issues:
Choose the right epoxy for the environment (e.g., industrial-grade for shops, UV-stable for outdoor areas).
Always apply a topcoat—this extra layer protects against heat, chemicals, and scuffing.
Keep open flames and welding equipment off epoxy—use a protective mat in those areas.
Why It Matters
Epoxy flooring is one of the most durable options available, but knowing its limits is key to keeping it in top shape. By protecting against harsh chemicals, preventing unnecessary impact damage, and using it correctly, you can extend the life of your floor and avoid costly repairs.
Next, we’ll discuss how neglecting maintenance and using the wrong cleaning methods can slowly degrade your epoxy floor—even if it was installed perfectly.
8. Lack of Maintenance and Improper Cleaning
Epoxy flooring in Port St. Lucie may be known for its resilience, but it still requires a basic level of care. The misconception that epoxy can be ignored indefinitely is a fast track to a worn-out surface. While epoxy is less demanding than carpet or tile, skipping routine cleaning and upkeep opens the door to scratches, dull patches, and lingering stains that gradually undermine the floor’s appearance and integrity.
Why Epoxy Still Needs Attention
Even if your floor looks spotless, tiny particles of dirt, sand, or salt can scuff the protective coating over time. Port St. Lucie’s coastal environment is beautiful, but the fine grains of beach sand people track in can act like sandpaper underfoot. Regular sweeping or vacuuming not only keeps the floor looking sharp but also preserves its finish.
Common Cleaning Mistakes
Some cleaning habits can do more harm than good. Here are a few pitfalls to avoid:
Using Harsh Chemicals: High-pH or acidic solutions can strip the finish, especially if they’re allowed to sit. Bleach and ammonia-based products are prime culprits.
Scrubbing with Abrasive Pads: Steel wool or harsh scouring pads can leave behind swirl marks and dull spots.
Letting Spills Linger: An epoxy floor won’t immediately absorb liquids, but acidic or oily spills can mar the surface if they’re left to pool.
Simple Ways to Maintain Epoxy Floors
A little effort goes a long way toward keeping your epoxy floor in prime condition:
Frequent Sweeping or Vacuuming: Removing abrasive debris helps prevent tiny scratches that build up over time.
Gentle Mopping: A mild, pH-neutral cleanser and a soft mop are usually all you need. This removes surface grime without degrading the topcoat.
Spot Cleaning: Address spills promptly. Even something as mundane as juice or soda can become sticky, and certain chemicals may leave permanent discoloration if ignored.
Periodic Inspection: Catching early signs of wear—like small chips or dull spots—lets you schedule touch-ups before they worsen.
Ignoring Maintenance Costs More in the Long Run
Replacing or refinishing a damaged epoxy floor is far more expensive than regular cleaning. What starts as minor scuffing can evolve into large-scale peeling or cracking if dirt and moisture infiltrate weak spots. By establishing a consistent cleaning routine and using the right products, you’ll preserve the seamless beauty and protective qualities that make epoxy flooring a standout choice in Port St. Lucie.
Up next, we’ll take a closer look at how Florida’s unique climate can add to these challenges—and what you can do to ensure your epoxy floor weathers local conditions without a hitch.
9. Florida’s Climate & Local Factors That Can Damage Epoxy
Living in Port St. Lucie means embracing sunshine, sea breezes, and occasional storms. While these elements make the area feel like paradise, Florida’s climate can be unforgiving on certain types of flooring—epoxy included. Understanding these challenges helps you choose the right materials and maintenance routines to keep your floor looking new.
Heat, Humidity, and Frequent Rain
Port St. Lucie summers can be hot and muggy. That moisture in the air can creep into small cracks or the concrete slab itself, weakening the bond between the epoxy and the floor. If the epoxy wasn’t sealed correctly or had moisture trapped underneath, you might see bubbling or discoloration after a season of high humidity.
Dehumidifiers and Air Conditioning: Running climate control during and after installation can reduce the chance of moisture compromising the final result.
Ventilation Without Overexposure: Allow enough airflow to keep condensation at bay, but avoid strong drafts that blow in dust or debris.
Salty Air and UV Rays
Coastal living offers ocean views and a laid-back vibe, but salt-laden breezes can be tough on surfaces not built to withstand corrosion. Epoxy floors that see frequent contact with salt, such as those near open garage doors or sea-facing patios, may require a topcoat formulated for coastal conditions.
UV Resistance: If direct sunlight hits your epoxy floor, you’ll want to consider a UV-stable topcoat. Prolonged sun exposure can cause yellowing or fading in standard epoxy without extra protection.
Storms and Hurricanes
Florida isn’t a stranger to tropical storms. In the event of flooding or high water, even epoxy can suffer if it’s not sealed around the edges or if water seeps under the slab.
Waterproofing Measures: Sealant around the perimeter helps block water intrusion.
Quick Cleanup: If water does breach the area, removing it and drying the floor promptly is essential to prevent moisture pockets from forming beneath the coating.
Taking a Proactive Approach
Rather than waiting until your epoxy shows obvious wear, consider local factors from the start. Talk with your installer about moisture mitigation, UV-stable products, and salt-resistant coatings if you’re close to the coast. By tailoring your epoxy floor to Florida’s unique conditions, you’ll ensure it stands up to the sun, sea, and storms that make Port St. Lucie one of the Sunshine State’s most appealing destinations.
Epoxy flooring is one of the most reliable, visually appealing solutions you can choose for your home or business in Port St. Lucie, but it only lives up to its reputation when installed and cared for properly. You’ve seen how factors like poor prep work, extreme weather, harsh chemicals, and rushing the curing process can undermine even the best floors. The good news is that all of these issues are preventable with the right approach and a bit of local know-how.
If you’ve been thinking about upgrading your garage, workshop, or commercial space with epoxy flooring in Port St. Lucie, we’d love to help you get it done right the first time. At Floor Kings, we’ve tackled countless projects under the Florida sun—from residential kitchens dealing with frequent spills to coastal garages that face constant salt exposure. We know what works in this climate, and we’re committed to delivering a surface that stands strong for years.
Ready to take the next step? Call Mike at 772-370-7938 or drop a note at [email protected]. We’ll talk about your space, your style preferences, and how to avoid the pitfalls that can ruin epoxy floors. Let’s transform your floor into a feature you’ll be proud to show off—without the worry of peeling, chipping, or hidden flaws. Whether it’s a sleek showroom look or a heavy-duty finish built for serious workloads, we’ve got you covered.