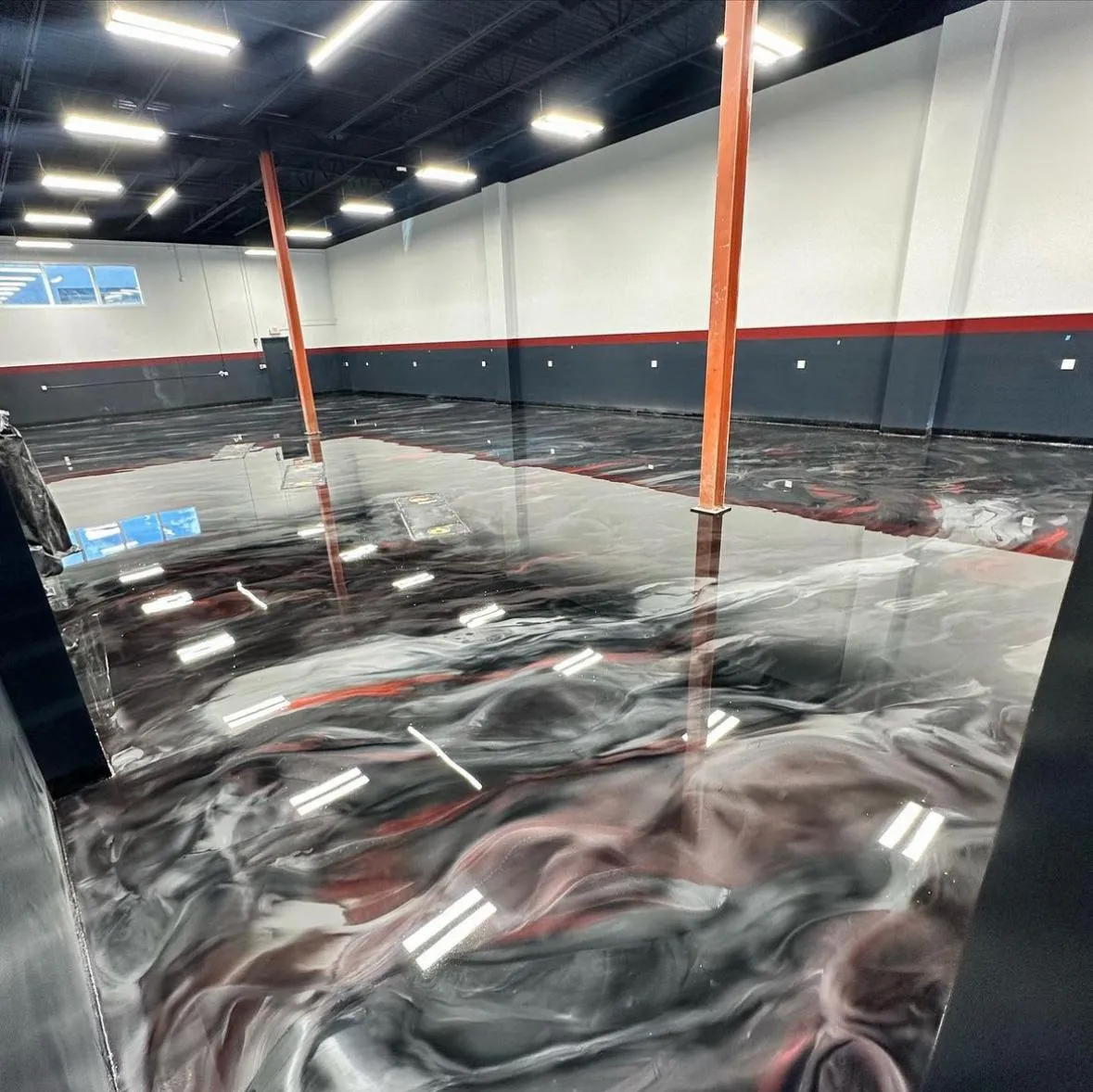
Why Epoxy Coatings Fail: A Comprehensive Analysis for Epoxy Flooring in Port St. Lucie, FL Client: Floor Kings in Port St. Lucie
Epoxy floor coatings boast resilience, chemical resistance, and a sleek finish. Yet, they can still fail when installed without proper site evaluation or technique. In Port St. Lucie, Florida, high humidity, occasional heavy rainfall, and warm temperatures add extra layers of complexity. This article investigates common failure points for epoxy floors, along with proven strategies that Floor Kings uses to guarantee long-lasting results. By blending scientific analysis with real-world examples, we provide actionable insight for anyone in Port St. Lucie seeking a durable epoxy solution.
Table of Contents
Introduction
Epoxy Coatings: Key Concepts
Leading Causes of Epoxy Floor Failures
Moisture and Humidity Concerns
Poor Surface Preparation
Wrong Product or Mix Ratio
Rapid Curing / Temperature Fluctuations
Substrate Movements and Structural Issues
Heavy Wear and Impact Damage
Chemical and UV Exposure
Research Findings on Epoxy Durability
Impacts of Epoxy Floor Failures
Best Practices for Success in Port St. Lucie
Floor Kings’ Approach to Failure Mitigation
Conclusion
1. Introduction
“One tiny pinhole can unravel an entire epoxy floor.” That straightforward assertion may sound dramatic, but it’s true. Epoxy is robust if installed meticulously. However, any oversight—like neglected moisture tests or a single unsealed crack—might create a cascading effect of blistering, peeling, or cracking.
In Port St. Lucie, FL, the coastal climate means humidity rarely dips. Frequent storms can raise groundwater levels, pushing moisture into the substrate. The heat can accelerate epoxy curing to the point where installers have little margin for error. These conditions demand specialized knowledge and protocols.
This deep dive will illustrate exactly why epoxy floors fail, from surface contamination to environmental extremes. We’ll also showcase Floor Kings and the measures we take to overcome these hurdles. Because an epoxy floor shouldn’t just look good—it should endure year after year, no matter what Florida’s climate throws at it.
2. Epoxy Coatings: Key Concepts
Epoxy coatings marry resin and hardener to create a thermoset polymer that bonds to concrete. When done right, epoxy forms a seamless layer capable of withstanding foot traffic, vehicle loads, and chemical spills. It’s widely used in garages, factories, dealerships, and even upscale residential spaces seeking a glossy, modern aesthetic.
Epoxy’s strength is impressive, but it doesn’t adapt easily to dynamic changes. The material is rigid, so it doesn’t handle substrate movement well unless steps are taken to mitigate that. Moisture also remains a key concern; epoxy doesn’t like to bond to a wet surface, nor does it hold up against vapor rising from below. Understanding these intricacies is step one in preventing failures.
3. Leading Causes of Epoxy Floor Failures
3.1 Moisture and Humidity Concerns
Port St. Lucie sits in a humid subtropical climate. Rainstorms can saturate the ground, raising moisture levels under slabs. Concrete can act like a sponge, wicking water upwards. If epoxy traps that moisture, vapor pressure builds. Eventually, the coating can bubble or delaminate.
High ambient humidity also affects curing. If water condenses on a curing floor, it can create amine blush or a cloudy surface. That’s why controlling both substrate and ambient conditions is critical in coastal Florida regions.
3.2 Poor Surface Preparation
Grease, oil stains, or existing sealants can all sabotage a new epoxy coating. If the floor isn’t ground or shot-blasted properly, the epoxy’s mechanical bond to concrete is weak. That weakness often leads to peeling. Even old paint or tile adhesives need to be stripped away thoroughly.
Surface preparation also includes addressing cracks and holes. These need filling with appropriate patch materials that don’t shrink. If left unfilled, they become weak points. Epoxy can’t patch them effectively unless they’re handled beforehand.
3.3 Wrong Product or Mix Ratio
Some epoxy systems are low-viscosity. Others are high-build. Others incorporate polyaspartic or urethane topcoats. Not every system works well under punishing heat or high moisture. Choosing a cheap product or failing to adapt to climate conditions can doom an installation.
Ratio errors are just as pernicious. Epoxy must be mixed in the exact ratio specified by the manufacturer. A slight deviation can lead to a floor that never fully hardens or that cures in a brittle manner. Thorough mixing is also crucial to avoid lumps or unmixed pockets.
3.4 Rapid Curing / Temperature Fluctuations
Florida weather can shift quickly. A morning that starts at 75°F might climb to 90°F by early afternoon. If the epoxy begins to set too quickly, installers might not achieve an even spread. They can’t properly degas or smooth out the surface. That can leave bubbles, roller marks, or incomplete coverage.
During cooler weather, it might cure too slowly, allowing contaminants to settle onto the surface. Striking the right balance means choosing the correct product for the day’s forecast and sometimes using fans or air conditioning to maintain stable conditions.
3.5 Substrate Movements and Structural Issues
Concrete slabs may crack over time. Settlement, minor earthquakes, or even fluctuations in the water table can cause subtle shifts. Epoxy doesn’t flex. When the substrate moves, cracks can telegraph right through. If control joints or expansion joints aren’t respected, the epoxy might tear along those lines.
Some installers try to bury or fill joints incorrectly, expecting the epoxy to hold everything together. That’s a mistake. Joints exist for a reason. They allow sections of concrete to move independently without causing widespread damage.
3.6 Heavy Wear and Impact Damage
Garages that see heavy vehicles, commercial loading docks with forklifts, or industrial facilities using metallic wheels can stress an epoxy floor to its limit. If the floor thickness isn’t chosen to match the load, or if the topcoat lacks adequate abrasion resistance, it can scuff and degrade prematurely. Once scuffs form, water, dust, and chemicals can reach the substrate.
3.7 Chemical and UV Exposure
Epoxy fares well against many chemicals, but repeated exposure to corrosives can erode it. Acids, aggressive solvents, or certain oils may degrade the polymer matrix over time. UV rays can cause yellowing if the epoxy is not UV-stable, which is a risk in areas with open doors or outdoor extensions. Proper product selection solves most of these issues, but ignoring them leads to advanced wear.
4. Research Findings on Epoxy Durability
Studies measuring the pull-off strength of epoxy coatings often highlight how a properly prepped substrate yields bond strengths of 400 psi or more. In contrast, neglected surface prep can drop bond strength under 150 psi, leading to early delamination. One Florida-based study reported that moisture-related blistering caused 70% of coating failures in coastal installations.
Another piece of research reveals that incorrect mixing ratios can cut the epoxy’s tensile strength by up to 40%. That’s the difference between a floor lasting ten years and one that fails in two. Such data underscores why precision matters for every aspect, from substrate readiness to final cures.
5. Impacts of Epoxy Floor Failures
When an epoxy floor fails, the repercussions can be costly and inconvenient. Business owners may face downtime, halting operations or turning away customers until repairs are complete. Homeowners might lose the use of their garage or living area. Safety hazards also escalate if peeling pieces become trip hazards or if cracked areas hold stagnant moisture. Reinstalling epoxy isn’t just a quick fix, either. Usually, you must remove the old coating entirely, re-prepare the surface, and start again.
In financial terms, a typical commercial epoxy floor can range in cost from a few thousand to tens of thousands of dollars, depending on the square footage. A complete reinstallation adds to that expense. Repeated failures can tarnish a property owner’s confidence and lead to frustration. Thus, doing it right the first time is far more efficient.
6. Best Practices for Success in Port St. Lucie
Port St. Lucie’s environment presents challenges that can be overcome with discipline and planning. We recommend the following:
Comprehensive Moisture Testing
Even if the slab seems dry, measure moisture vapor emission. If it’s too high, use moisture mitigation primers or address drainage issues.Mechanical Surface Prep
Diamond grinding or shot blasting is standard. The goal is a clean, roughened surface free of contaminants or previous coatings.Climate Control
For large-scale jobs, controlling indoor temperature and humidity can be essential. Portable AC or dehumidifiers might be necessary, especially in summer.Product Selection
Choose epoxy formulations rated for Florida’s humidity and temperature range. Consider polyaspartic or polyurethane topcoats in areas exposed to direct sunlight.Precise Mixing
Measure carefully, using weight or volume guidelines. Stir thoroughly for the recommended time. Discard any unmixed remnants at the edges of the container.Correct Application
Follow the recommended spread rate. Watch for pot life. Quickly address any bubbling by rolling or spike-rolling. If in doubt, consult the manufacturer’s specs.Joint and Crack Management
Fill cracks with semi-rigid products designed to handle subtle movement. Respect expansion joints, using flexible fillers where needed.
7. Floor Kings’ Approach to Failure Mitigation
At Floor Kings, we recognize that no two floors are identical. Some see heavy forklift traffic, while others serve as a family’s recreation room. Port St. Lucie’s climate also demands vigilance. Here’s how we handle it:
Site Assessment
We begin by evaluating the slab’s condition and the environment. This includes moisture tests, checking for cracks, and understanding the property’s usage patterns.Customized Preparation
If old tiles or coatings exist, we remove them. We grind the surface to an ideal profile. If the substrate has damage, we repair it with high-quality fillers. We thoroughly vacuum and wipe away dust, ensuring a contaminant-free area.Moisture Barrier
When testing reveals elevated vapor emission, we apply a moisture-tolerant primer or epoxy specifically made for damp conditions. This is essential in areas prone to high water tables or frequent rainfall.Targeted Product Selection
We offer various epoxy systems, including polyaspartic topcoats for UV stability or chemical-resistant finishes for industrial environments. Each selection is deliberate, matching real-world conditions.Expert Mixing and Application
We use calibrated containers and mechanical mixers to achieve a perfect ratio. We track the pot life carefully, ensuring we apply the epoxy before it begins to set. Our installation crew is trained to identify and eliminate bubbles on the fly.Controlled Curing
We monitor the floor’s temperature. If conditions spike above recommended levels, we’ll schedule the pour for cooler times or use climate control. We also keep foot traffic off the floor until it’s fully cured. No shortcuts.Ongoing Support
After the project, we guide you on proper cleaning methods, safe chemicals, and early detection of minor issues. We’re always available for maintenance or repairs, if needed.
These steps have allowed us to deliver epoxy floors that stand the test of time, even in Florida’s challenging climate. We see epoxy as a science. Variables matter. By controlling them, we achieve consistency and reliability.
8. Conclusion
Epoxy flooring can fail, but failure is not inevitable. In Port St. Lucie, the main threats—humidity, heat, and substrate movement—can be mitigated through rigorous planning and execution. Moisture testing, mechanical surface prep, accurate mixing, and climate-conscious application are non-negotiable steps. Short sentence: There are no shortcuts. Longer sentence: Every stage of an epoxy installation, from the initial inspection of the concrete’s condition to the final topcoat’s cure, shapes how well the floor will perform over the coming years.
Floor Kings employs a structured approach. We adapt to Florida’s warmth, cope with humidity, and choose products wisely. The result? Floors that resist peeling, delamination, or bubbling. A well-executed epoxy system isn’t just about aesthetics; it’s about delivering confidence and longevity in a region where weather is often unpredictable. Done right, epoxy becomes a true investment, offering a clean, durable surface that can transform any residential or commercial property.
If you’re ready for an epoxy floor solution in Port St. Lucie that truly lasts, get in touch with Floor Kings. We cater to both residential and commercial clients, adapting each installation to the demands of the space.
Contact: Mike
Phone: 772-370-7938
Email: [email protected]
Let us assess your project and outline a plan to prevent the pitfalls common to epoxy flooring in Florida’s climate. Reach out today for a consultation or a quote. Don’t wait until a failed floor causes costly downtime. Let’s do it right from day one.